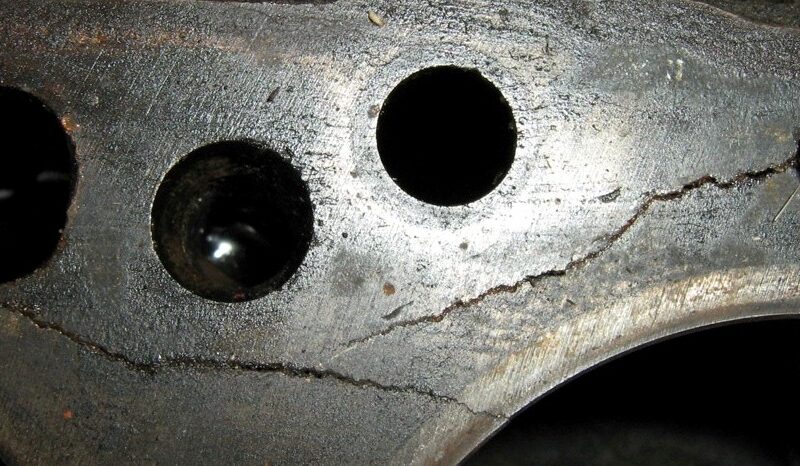
Crack in the cylinder block: What shall I do?
Among the breakdowns of the internal combustion engine should be noted the appearance of cracks in the cylinder block and the cylinder head. Such cracks in the engine housing and other components are quite common. During operation, many components in the design of internal combustion engines are subject to severe mechanical and thermal loads, which create natural wear of the power unit. The unit is also cracking due to accidents, the cylinder block walls or the cylinder head can be pierced by engine parts (connecting rod, etc.. d.) as a result of jamming of the power plant.
We also recommend reading the article about it, what is engine warm-up. You will learn from this article, what are the benefits of installing extra weight in the car.
Removal of cracks in the cylinder block and cylinder head
The blocks and heads of the engine blocks consist of various metal alloys. Today's technology often allows you to repair damaged elements. Next, we will consider ways to fix the breakdown and answer questions, how to remove cylinder block cracks and repair cylinder head cracks. In some cases, the repair of cracks can be done with your own hands.
One of the most widely used ways to eliminate cracks in the cylinder block and cylinder head is to seal the defects of silumin and cast iron blocks by welding.
Welding can be both electric, and "cold". Under cold welding it is necessary to understand clogging of cracks by various materials on the basis of polymers. Almost all cracks can be brewed in the first or second way, except for cracks in the area of the valve seat, cylinder walls, as well as those surfaces, where the fit of the BC and cylinder head.
How to find a crack
The following methods are used to detect cracks:
- method of ultrasonic detection;
- use of magnetically sensitive equipment;
- method of pneumatic pressing;
- search for cracks by means of hydrocontrol;
In practice, the detection of cracks in many garages is carried out by injecting air or water into a faulty engine element.. In the case of air, the part is additionally immersed in the bath and find defects in the bubbles. If the element is pumped water, then the need for immersion is eliminated, since cracks are diagnosed by fluid leakage.
To determine the exact boundaries of the crack on both sides of the split, a pair of magnets are attached, the space between the magnets is filled with special conductive sawdust. The presence of a crack will lead to that, that the magnetic field lines will break, sawdust partially grouped on the surface of the split. This method allows you to clearly detect a crack in the cylinder block or cylinder head.
Repair of cracks by means of welding
It should be noted, that cracks should be eliminated in strict accordance with all recommendations. Residual mechanical stresses in the seam area can lead to a violation of its integrity and the need for re-repair.
The cast iron block is restored by twisting the ends of the crack and subsequent grinding of the entire length of the split at an angle 90 degrees. Drill is necessary for this, to prevent further spread. As for welding, at the initial stage, the cylinder block is heated to 650 degrees Celsius. After that the continuous seam by means of filler pig-iron - copper rod and flux is put.. The final stage is the gradual cooling of the part, for which a special thermal cabinet is required.
We also recommend reading the article about the advantages and disadvantages of installing gas equipment on the car. In this article you will learn about it, whether it is necessary to save on gasoline and what consequences for the motor can arise as a result of driving on gas.
In order not to overheat the unit, you can use electric welding and copper electrodes in a tin wrapper. At the end of the surface of the resulting seam is degreased with acetone and additionally applied a layer of epoxy paste with a special spatula. Epoxy hardens over 24 hours at room temperature about 2 hours when heated to 100 degrees Celsius. The final stage will be grinding of the processed seam.
Alternative ways
Let's start with that, that minor cracks can also be closed by using epoxy paste and fiberglass. Before starting work, the metal surface must be well degreased. Layers of paste and fiberglass alternate when applied, the last layer should be epoxy.
Among the most popular technologies today is also a solution called SEAL-LOCK. The advantages of this method include the absence of the need to dismantle the engine. The method is suitable for repairing serious holes or cracks in the cylinder block. Also, the use of a welding machine is not required for repairs.
The method is based on filling the crack with a special layer of soft metal, which as a result is securely fastened to the surface of the restored part.
- The crack is localized, after which the edges of the split are drilled. Then across the crack drill holes with the established technology step. Clamps are inserted into these holes, connecting both edges of the crack. Brackets are selected according to the type of split, as they can have different lengths and differ in their shape.
- Next, a hole is drilled in the space between the installed brackets, then there is a cutting of a conical carving by means of a special tap. After that it is necessary to carry out processing of the received opening with structure for removal of an oxide film. Then the cone cap is screwed into the machined threaded hole with little effort., the material of which is in active contact with the metal of the repaired part.
- Then part of the cap, which rises above the plane, need a little sawing, then screwing is carried out with great effort, created by a special tool. As a result, the soft plug will break in that place, where previously undercut was made. The protruding residues are additionally ground.
- The next step is to drill the next hole. It drills a hole like that, to achieve partial overlap of the pre-threaded hole with the cap installed. The repair procedure involves filling the entire crack with plugs.
When the work on the installation of all screeds and caps is completed, and also carried out grinding, a seam is formed. This seam must be further compressed (rivet) using a percussion instrument (pneumatic hammer with the ability to change the frequency of vibrations).
Riveting the seam allows you to eliminate possible voids, and also accelerates diffusion of materials of rivets and details. The result will be the appearance of a plastic seam, which has a strong bond with the surface. This seam has a number of advantages over the weld:
- does not suffer from temperature changes;
- able to maintain integrity in working conditions at high temperatures;
- does not receive significant stress;
As for the installation of large patches, which can literally "seal" a cracked cylinder block or engine head, then the method of solving the implementation scheme is similar to that described above.
You need to cut and adjust the metal patch, then its installation is carried out by filling all perimeter with couplers and conical caps. Further check of the finished seam for tightness is carried out by pressing under pressure 6 atmospheres.