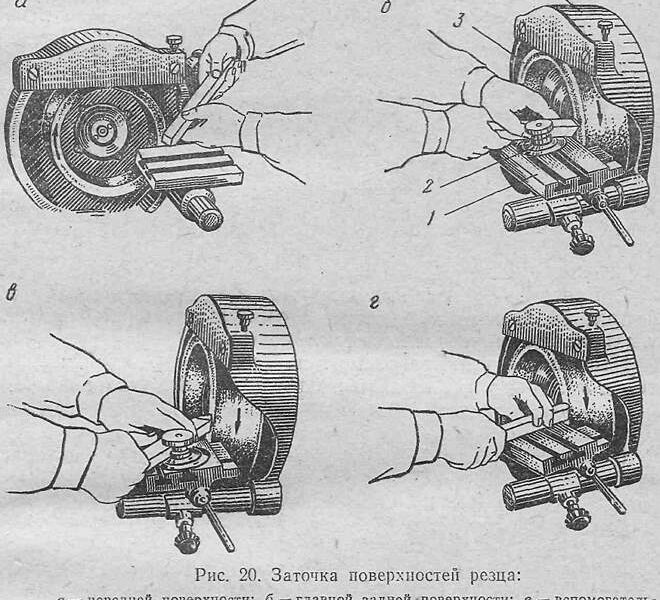
Sharpening of cutters for a lathe on metal: video, because of, nuances
Of all technological operations, made over metal blanks, turning on turning equipment is the most common. That is why sharpening cutters for a lathe, designed to work on metal, is a very important process, to be performed correctly. Features of such a procedure depend on the material, which will need to be processed, and from the type of the cutting tool (shaped, passable, threading, boring and others).
The order of sharpening the surfaces of the cutter
Design of turning cutters
Sharpening of lathe cutters cannot be performed correctly, if you do not understand the design features of such a tool. The main elements of its design are the rod-holder, by means of which the cutter is fixed on the machine, as well as the working head: it is its cutting part and must be sharpened regularly.
Розглянемо більш докладно робочу головку токарного різця. It is formed by two types of surfaces: front and rear. The front is very easy to distinguish: it is on it that the chips are removed. The back sides are the sides of the cutters, to which the workpiece is addressed in the process of its processing. They can be primary or secondary, depending on their location.
The most important element of any cutter (including for the lathe on metal) - its cutting edge - is formed at the intersection of the rear main and front surfaces. An auxiliary edge is present in the design of any cutter, formed by the intersection of its posterior surfaces: main and auxiliary. The top of the tool, which is mentioned in the literature, - is the intersection of its cutting and auxiliary edges.
The main characteristics of metal lathe cutters, that determine their functionality, there are sharpening angles, divided into main and auxiliary. To determine the value of the main, their measurement is made in the plane, which is formed when designing the cutting edge on the main plane.
In general, two planes are used to determine the angles of the cutting tool:
- basic, superimposed on the support side of the lathe cutter, located at its bottom (with respect to the feed direction of the machine, such a plane is parallel);
- cutting plane, located tangential to the surface of the workpiece (this plane intersects with the main cutting edge of the tool).
Elements and planes of a turning cutter
In the design of the working part of the lathe cutter distinguish angles of several types:
- exacerbations - located between the anterior surface of the incisor and the posterior main;
- rear main - are located between the rear main surface and the cutting plane;
- front main - located between the front of the tool and the plane, perpendicular to the cutting plane.
It is quite simple to check the accuracy of their definition: their sum is always 90 degrees.
In addition to those listed above, the design of the working head of the lathe cutter is characterized by several angles between:
- feed direction and projection, which is postponed by the main cutting edge;
- the plane of processing and the front surface of the cutter;
- projections, which set aside the main and auxiliary cutting edges.
Tools for turning equipment
In order to understand the rules of sharpening cutters for lathes on metal, it's not enough to just watch a training video. You need to have an idea of that, how such instruments are classified. The most important parameter, according to which lathe cutters belong to different types, is a type of processing, performed with their help. On this basis, the following types of turning cutters are distinguished.
The main types of turning cutters
checkpoints
Such cutters workpieces are machined along the axis of rotation.
undercut
Using these cutters on a lathe, reduce ledges and perform trimming of workpieces.
grooves
As the name implies, they form the outer and inner grooves on the surfaces of the cylindrical shape. It is possible to create grooves on external parties of preparations and by means of cutting cutters on metal. in addition, such cutters allow to cut off preparations at right angles.
boring
With the help of such tools on the machines perform machining holes.
threaded
Such cutters are specially designed for threading.
shaped
With the help of cutters of this type on the outer side of the cylindrical workpieces form shaped protrusions or grooves.
fasochnye
With the help of these cutters on the workpieces are chamfered.
Operations, made by cutters of different types
Turning cutters are also divided into types depending on, in which direction with their help the workpiece is processed. So, among them are the right (processing is performed in the direction of the front grandmother) and left (processing in the direction of the rear headstock).
Turning tools are also classified according to the material of manufacture, according to the method of connecting the cutting part to the holder, as well as a number of other parameters.
Rules of sharpening of the turning tool
That processing of preparations on lathes on metal was effective, high quality and accurate, sharpeners should be sharpened regularly, thereby giving their working part the desired shape and obtaining angles with the required parameters. Sharpening does not require only tools, the cutting part of which is made in the form of a disposable carbide plate. To perform so important ??procedures in large industrial enterprises use machines with special devices, and this is a separate structural unit.
To sharpen a lathe with your own hands on a home machine or do it in a small business, you can use different techniques. This procedure can be performed with the help of chemical reagents or with the use of ordinary grinding wheels. It should be noted, that sharpening of the turning tool on specialized or universal machines, in which the abrasive wheel is used, is the cheapest, but an effective method of giving the cutters the necessary geometric parameters.
Options for sharpening cutters with cutting inserts
Of course, the most high-quality metal lathe cutters are sharpened on a machine specially designed to perform such a procedure. If you do not have such equipment, you can use a universal machine with a grinding wheel. Picking up such a circle, it is important to pay attention to the material, of which it is made ??working part of the processed tool. So, to effectively sharpen the carbide cutter, you will need a circle of carborundum, having a characteristic green color. Tools, the working part of which is made ??made of carbon or high-speed steel, are perfectly processed on machines with circles of average hardness, made of corundum.
Sharpening of lathe cutters on metal can be performed without cooling or with cooling, which is the best. If sharpening is performed with cooling, then the cold water should be evenly supplied to that place, where the lathe cutter is in contact with the grinding wheel. In that case, when cooling is not used during sharpening, after its execution it is impossible to cool down the tool at once sharply: this can lead to cracking of its cutting part.
You can learn to sharpen lathes on a grinder with your own hands on the training video. In the process of performing such a procedure, it is important to follow a certain sequence. First of all, the rear main surface is processed on the grinding wheel, then the rear auxiliary, and in the last turn to sharpen forward. The last stage of sharpening is the processing of the top of the cutter - giving it the required radius of curvature.
In the process of sharpening the cutter is constantly moved in a circle, trying not to press him too hard (this can be seen in the video). It is necessary to follow such a recommendation, so that the surface of the circle wears evenly, and also that the cutting edge of the turning cutter turned out as equal as possible.
Features of sharpening of cutters for the lathe
There are certain nuances, which should be taken into account when sharpening lathes with your own hands using a grinder. So, the processing of the rear surface of the cutter is carried out in three stages.
- First, the rear surface is treated at an angle, equal to the rear corner of the state itself. Usually, it turns out a little more, than the rear cutting angle (about 5 degrees).
- In the second stage, the rear surface of the cutting plate is processed. At the same time it is sharpened at an angle, exceeding the rear cutting angle by 2 degrees.
- The third stage is the formation of the required rear angle with the help of proof. Importantly, that such an angle is not formed on the entire rear surface of the cutter, but only on a narrow bevel, directly adjacent to the cutting edge.
Sharpening of the front surface of the lathe cutter is performed in several stages. So, pre-sharpened at an angle, equal to the angle of the cutting plate. This corner, as in the case of the rear surface, slightly exceeds the front cutting angle. Direct cutting angle, which must be formed on the front surface of the cutter, obtained by finishing or sharpening. A narrow strip is subjected to these processes, adjacent to the cutting edge of the carbide plate.
Use of substrates during sharpening
For greater convenience of sharpening lathes on grinders, and special substrates are used to obtain angles with specified parameters, which are installed between the support surface of the tool and the machine table, where it is located. To achieve even more accurate and high-quality sharpening, you can finish the design of the machine table with your own hands, making it adjustable in height and angle of rotation. After such completion of the machine, the need to use substrates of a certain thickness is eliminated.
When sharpening a lathe cutter, it is important to pay attention to that, so that its cutting edge is flush with the center of the grinding wheel, but not below, than 3-5 mm in relation to it. The direction of rotation of the grinding wheel should also be taken into account. This is necessary for that, to make the sharpening process safer, and to minimize the risk of separation of the cutting insert from the cutter holder. The grinding wheel in the process of sharpening should rotate as follows, to press the cutting plate, rather than tearing it from the state.
Template for checking the correctness of sharpening cutters
Naturally, that after sharpening the cutting tool for the lathe on metal it is necessary to check up correctness of its execution. The easiest way to perform this procedure is with a special template, which can be purchased or made with your own hands. If you buy a ready-made sample is not possible, then make it better yourself from sheet steel, which can be hardened.
High hardness of such a template, which he will receive after quenching, will allow you to use it for a long period. Making a stencil, it is necessary to make cuts on it, corresponding to the most running angles of sharpening. Only after making such cuts, the finished template is hardened. It should be borne in mind, that the accuracy of the manufacture of such a stencil will depend entirely, how well your metal lathe cutter will be sharpened.
After sharpening, the cutting edges of the tool must be brought to the desired state. Small areas of the cutter surfaces are subjected to such proof (width up to 4 mm), directly adjacent to its cutting edges. Copper bars and additives are used to perform the proof, the choice of which depends on the material of the working part of the tool. So, to bring carbide cutters on the bar apply a special paste or boron carbide, moistened with kerosene. For finishing cutters from other materials use bars with a low level of abrasiveness, the surface of which is moistened with machine oil or kerosene.