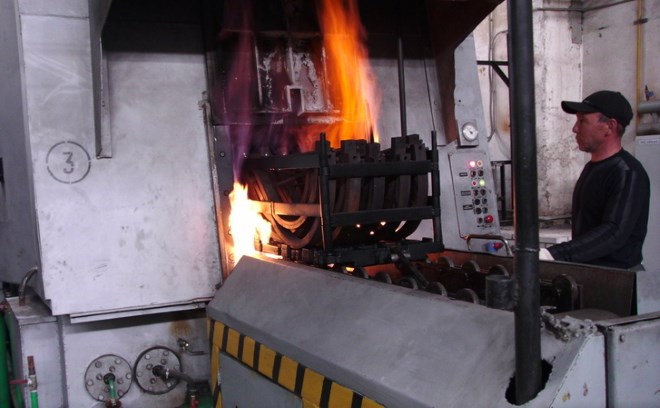
Cyanization and nitrocementation of steel: technology and purpose
Cyanization, the purpose of which is to saturate the surface layers of steel with nitrogen and carbon, is one of the varieties of such a technological operation, as nitrocementation. Compared to conventional cementation, this method of processing steel is more efficient, because it allows you to give steel products special mechanical properties.
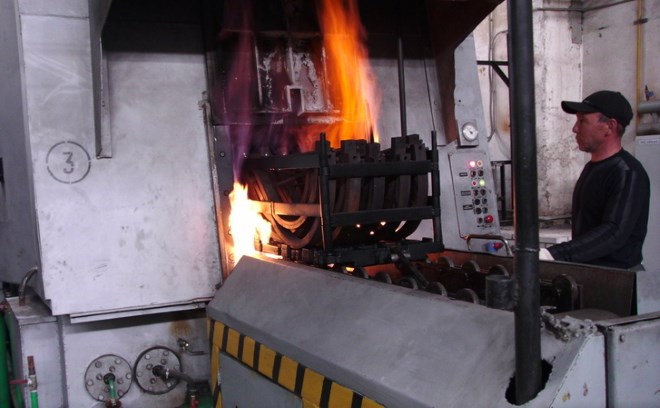
FEATURES OF NITROCEMENTATION AND CYANATION
Although nitrocementation and cyanation pursue the same goal (saturation of the surface layer of steel with nitrogen and carbon), they have one significant difference. It is, that products undergo nitrocementation in a gas environment, and during cyanation, such an environment is a melt of sodium cyanide or other salts.
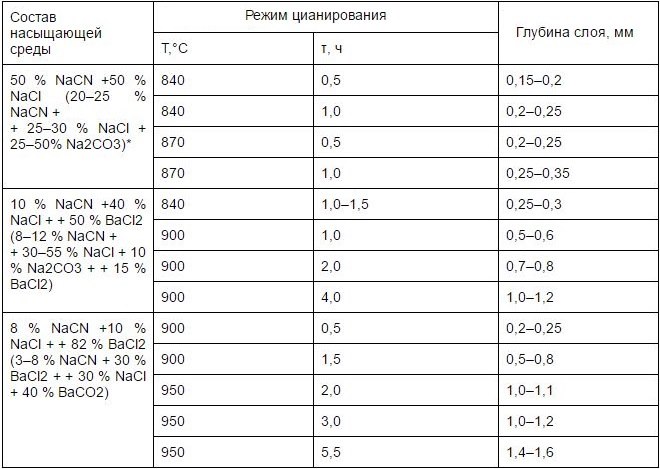
The considered technological operations demonstrate their effectiveness when processing such materials:
- steels, belonging to the stainless category;
- alloyed steel alloys, as well as steel, which do not contain alloying additives and are characterized by an average carbon content in their composition;
- structural steels with low carbon content.
Cyanization of steel, which belongs to one of the above categories, as well as the process of its nitrocementation, occurs at a certain temperature (820-950°), which must be strictly followed. As a result of qualified application of such processing methods, it is possible to solve the following tasks:
- increase the wear resistance of the surface of the product;
- increase its surface hardness;
- increase the endurance limit of the metal.
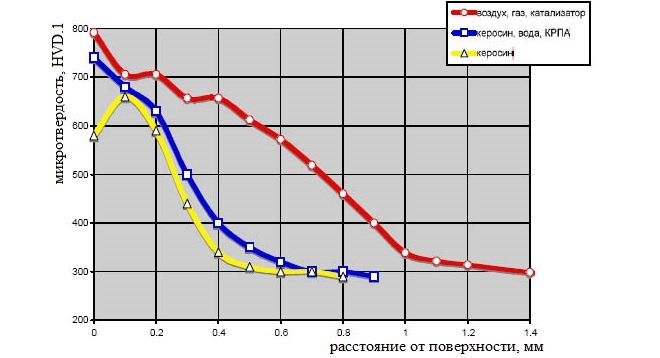
There is another type of cementation, which is called soft nitriding. Such processing, which is performed at a temperature of about 590°, medium-carbon steel is needed to increase the level of their wear resistance and endurance limit. Products made of high-speed steel are also subjected to cyanide, which allows to increase the hardness and wear resistance of their surface layer, and also make it more resistant to the effects of elevated temperatures.
Such a technological operation is also used in the metallurgical industry, as cyanation of gold-bearing ores, which is fundamentally different from all the above methods of processing steels. The purpose of cyanation of ore, the composition of which may contain gold even in very small quantities, there is a release of concentrate from it, characterized by a high content of precious metal. Such a concentrate, after its further processing, can be used for the production of gold products.
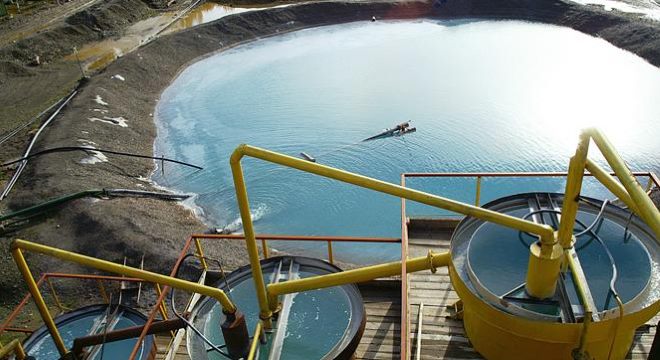
DIFFUSION OF NITROGEN AND CARBON IN THE SURFACE LAYER OF STEEL
Saturation of the surface layer of the steel product with nitrogen and carbon, what is meant by nitrocementation and cyanation, occurs due to the diffusion of these elements into the internal structure of the steel alloy. In the surface diffusion layer of a steel product, the amount of nitrogen decreases when the temperature increases during cyanation, and the quantitative carbon content, vice versa, increases.
The carbon content in the diffusion layer can increase continuously or only up to a certain point, and it begins to decrease only at the last stages of the technological operation. Due to such a feature of the carbon diffusion process, the saturation of the surface layer of the steel product with this element can be fixed at different temperatures of cyanation. The degree of saturation is greatly influenced by the carbonizing ability of the medium, in which this technological operation is performed.
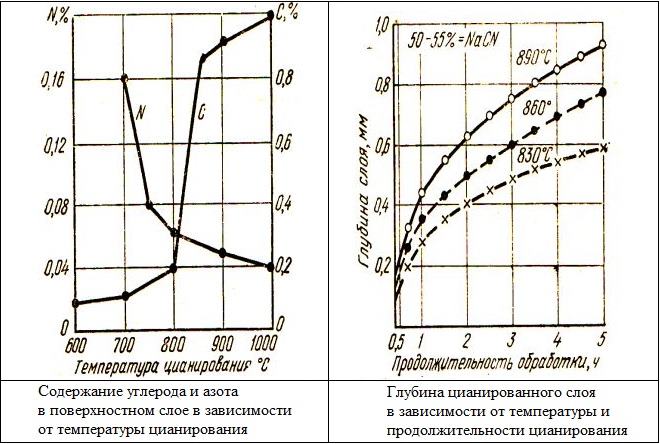
The parameters of the co-diffusion process are seriously affected by nitrogen, from which, in particular, depend:
- the depth of the metal layer, on which carbon diffusion will occur;
- degree of saturation of such a layer with carbon.
Meanwhile, a high nitrogen content in the cyanide medium can lead to, that diffusion of carbon into the steel structure will not proceed actively enough. This is due to the fact, that nitrogen, when there is too much of it in the working environment for cyanation, contributes to the formation of carbonitride phases or formations on the surface of the processed product.
The process of saturation of the surface layer of the steel product with nitrogen and carbon during cyanation and nitrocementation takes place in two stages, which have little in common, if we compare their kinetic indicators. So, at the first stage, which can last from 60 to 180 minutes, the surface layer of the product is saturated with nitrogen and carbon. At the next stage, individual nitrogen atoms, already absorbed into the steel structure, can be desorbed, that is, to go back into the gas phase and exit through the surface of the alloy. During the second phase of cyanation, the outer layer of the processed steel continues to be saturated with carbon.
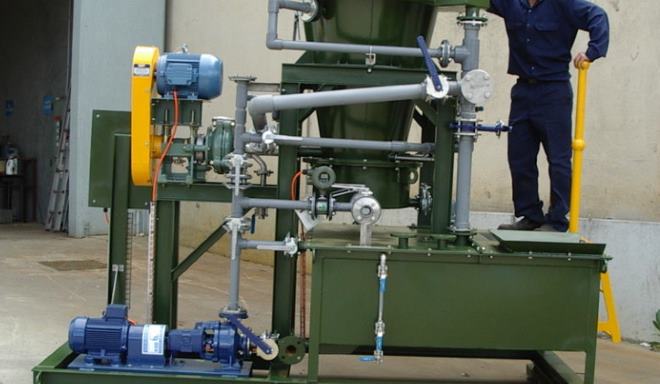
The process of reducing the amount of nitrogen and increasing the carbon content in the processed steel, which occurs when the temperature increases during cyanation, has a linear character. At the same time, such linearity is characteristic only for the upper layer of the diffusion zone, while in the layers of the steel product, located at a greater depth from its surface, it is not observed.
A characteristic feature of cyanation is that, that carbon penetrates into the processed product to a lesser depth, than nitrogen. The depth of penetration of these elements into the steel structure depends mainly on the microstructure of the processed material. Cyanized products of small thickness may differ in higher fragility, if you compare them with details, processed according to standard cementation technology.
ADVANTAGES AND DISADVANTAGES OF TECHNOLOGY
Process of nitrocementation and cyanation, as mentioned above, is carried out at relatively low temperatures, which contributes to less intensive wear of the used equipment, and also does not lead to significant deformations of the processed parts. At the same time, performing technological operations in such modes eliminates the need to cool the processed product to low temperatures.
After cyanidation, the austenite structure of the steel becomes more stable, which improves the annealing of individual areas of the material, which have been subjected to such treatment. In particular, it is thanks to these properties of the cyanidated material that low-alloy steels can be hardened in oil.
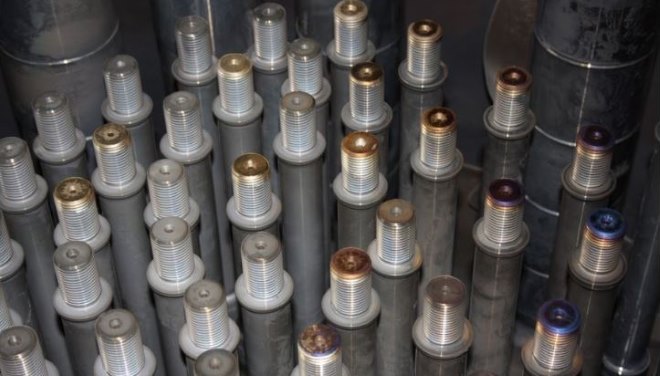
Nitrocementation and cyanation increase the hardness and contact durability of products
Residual austenite, present in steels, which were subjected to cyanation, contributes to the improvement of such characteristics of the material, as:
- bending strength;
- impact strength;
- plasticity;
- fatigue strength.
That is why details are processed with the help of cyanide, which are subjected to significant loads during operation. Here, in particular, include shafts and gears, the core of which should differ not only in sufficient strength, but also with sufficient viscosity. The formation of precisely such characteristics is achieved during cyanation.
Meanwhile, cyanation has a number of disadvantages:
- The size of the surface layer of steel, the characteristics of which are improved as a result of such a technological operation, is only seven to eight tenths of a millimeter.
- When performing cyanation, it is necessary to constantly monitor the degree of nitriding and carburization, which the working environment has.