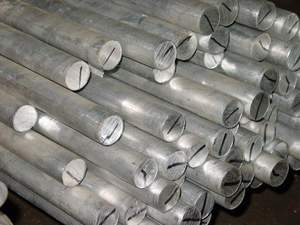
What are the characteristics of duralumin, and where this material is used
Duralumin was developed more than hundreds of years ago, v 1903 year. Then Alfred Wilm, metallurgical engineer, being an employee of a German metallurgical plant, established a certain pattern. It turned out, aluminum alloy with four percent copper after quenching at + 500 ° C and quenching, withstood at room temperature for several days (to 4-5), becomes stronger and firmer, but also does not lose its plasticity. Subsequent experiments led to an increase in the number of constituent elements, which increased the strength of pure aluminum (about 70-80 MPa) to 350-370 MPa.
History of the name
A group of alloys of this type is named after the German city of Duren. Here they began their production on an industrial scale 1909 year, six years after the discovery and study of properties. In addition to the name "duralumin" is also found:
- English version - "duralumin";
- old form - "duralumin";
- "duralumin", as a common name for the "family" of aluminum of this type.
There is an allusion to the Latin word Durus, which means hard, firm. This is how the basic properties of these metals are characterized.
The composition of aluminum alloys: different types
- Al-Mn systems, Al-Mg. The main characteristic is high corrosion resistance (a little less, than pure aluminum). in addition, they are well suited for welding and soldering, but not cutting. These alloys do not harden by heat treatment. Used for the manufacture of tanks, oil pipelines, gas lines, car radiators and tractors, elements of utensils, in construction (depending on the specific species and its characteristics).
Al-Mg-Si family - alloys, which are called corrosion-resistant. Strengthen them with heat treatment. It consists in quenching at temperature 515-525 degrees Celsius followed by cooling in cold water with natural aging at 20 degrees for about ten days. The main property of finished materials of this group is high corrosion resistance in normal conditions and in cases of live operation.
- Al-Cu-Mg alloys are called structural, or duralumin. Their base is aluminum, which is doped in various proportions with copper, magnesium and manganese. Based on them, receive different species with their own characteristics, which can be divided into a number of groups, which will be discussed below.
Dural materials have powerful mechanical properties, but more prone to corrosion, than the second considered type of family of alloys. Manganese partially fights this, which is additionally introduced into the composition. But at operation of duralumin it is necessary to protect it by means of paint and varnish coverings or to subject to anodizing. If the alloy is used for clad sheets, then they themselves have a sufficient degree of corrosion resistance. That is, it also largely depends on the type of treatment.
In addition to the above alloy systems, there are also:
- heat resistant;
- forging;
- heat-resistant forgings;
- high-strength structural alloys.
As we see, Many years of studying the properties of aluminum-based materials have created many different species and types, which have the necessary properties in a particular industry.
Duralumin alloys
There is everything 4 duralumin alloy. All of them in different proportions contain as the main components (copper, magnesium, manganese), and others (Fe, And, You, Zn, Ni).
- D1: copper - 4,4 ±0,4%, magnesium - 0,6 ± 0,2%, manganese - from 0,6 ± 0,2%;
- D16: copper - from 3,8 to 4,9%, magnesium - 1,5 ±0,3%, manganese - 0,6 ±0,3%;
- D19: copper - from 3,8 to 4,3%, magnesium - 2,0 ±0,3%, manganese - from 0,5 to 1,0%;
- VD17: copper - 2,9 ±0,3%, magnesium - 2,2 ±0,2%, manganese - from 0,45 to 0,7%.
Other elements are present in the materials in a total amount of not more than two percent.
Each type of duralumin also requires its own heat treatment mode.
Alloy D1 is hardened at a temperature of 495-510 ° C, and then undergoes the stage of natural aging at 20 ° C for 96 hours and more.
For D16 hardening takes place in two modes (depending on, in what form the source material will be presented). If we are talking about sheets of D16, then it requires a quenching temperature 500 ± 5°C. The aging process can be done at 20 ° C for four days or more, or at 188-193 ° C in a much shorter number of hours - 11-13. If this D16 is then used for extruded products, then the tempering temperature limit drops to 485-503 ° C. Aging can also be done in two ways:
- room temperature - at the same time;
- at temperatures of 185-195 ° C - in the range 6-8 hours.
VD17 hardens in the range of 495-505 ° C, and aging is performed compulsorily at 170 ± 5 ° C for 16 ± 1 hours.
D19, as well as D16, has different conditions for hardening and aging of materials:
- for sheets - t = 505 ± 5 ° C, aging - at 20 ° C for 5-10 days or at 185-195 ° C 13 ± 1 hours;
- pressed virobi - t = 500 ± 5 ° C, aging - similar under room conditions, or when 190 ± 5 ° C for 9 ± 1 hours;