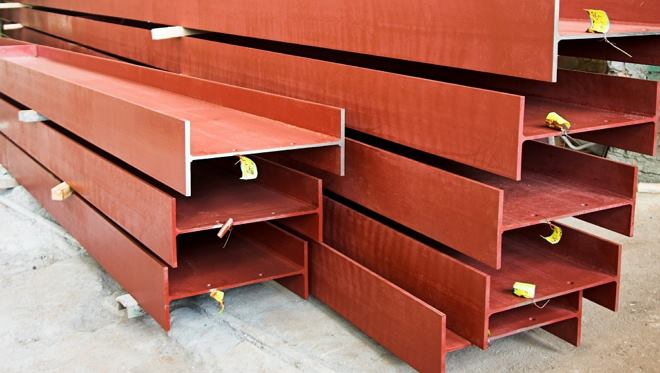
Welded beam - production and welding technology
If earlier beams were used in construction, the elements of which were connected by numerous bolts, pins and rivets, which significantly aggravated the whole structure, now they have been replaced by strong and reliable welded beams, differing in light weight.
Ready I-beams in stock
Advantages of welded I-beams
Nowadays, it is very difficult to find a construction site, which was built without the use of welded I-beams. Beams, having such an intersection, widespread back, that significantly reduce the cost of construction of buildings for various purposes, ensuring high reliability of erected structures.
Welded beam, the cross section of which has the shape of an I-beam, able to withstand significant static and dynamic loads, without losing at the same time, their performance characteristics. An important factor is that, that the use of such welded beams can reduce the weight of building structures, which in turn reduces the load on the foundation of the building and its load-bearing structures.
The use of I-beams in the manufacture of building frames
Welded I-beam is especially indispensable in those elements of building structures, where strength and ability to successfully withstand mechanical loads of different orientations are especially important. To such elements, in particular, frameworks for various designs concern, columns, mezzanine floors, trestle, work platforms and more.
Welded beam is very popular in various branches of mechanical engineering and in the construction of prefabricated buildings, because the technology of its production is very economical.
Though, that to organize the manufacture of welded beams of I-beam section is quite simple, it is economically more profitable to produce them using automated equipment. Automated lines, on which the production of such welded beams is put on stream, allow not only to significantly reduce the cost of production, but also strictly adhere to the technology of its manufacture.
Overlapping on metal I-beams
Technological process of production of welded beams of I-beam section
Technology of manufacturing welded beams, having an I-beam section, consists of several successive processes, each of which has already been perfectly worked out. so, production of high-quality and reliable welded beam of the required cross-section consists of several procedures.
Creating a blank according to the drawing
Thermal cutting equipment is used for its production, on which sheets of metal of the necessary thickness are cut out on the set sizes. The result of such a technological operation are strips, having length and width, due to the drawing. Modern enterprises use CNC machines to perform such an operation, on which cutting of metal can be carried out by several cutters simultaneously.
Edge processing by milling
This operation no longer requires a drawing and it is performed on special equipment (edge milling machines). This stage of production is necessary for that, to ensure better weldability of the wall of the I-beam and its shelves.
Assembly operation
At this stage, the future welded beam is assembled into a finished structure, for which special assembly devices are used, allowing to increase process productivity in 2-3 times compared to manual assembly. When performing the assembly operation before welding the beam, having an I-beam section, it is important to ensure the correct relative position of the I-beam wall and its shelves (symmetry and mutual perpendicularity).
It is best to use special assembly equipment to meet these important requirements, equipped with high-speed clamping elements. It allows not only to accurately position the components of the future I-beam, but also to do it quickly and with high reliability. Assembly technology using such devices consists of two main stages: initially only part of the beam is assembled, component T-shaped profile, then the assembled structure with the help of the device is turned over 180 degrees and complete its second shelf. At modern enterprises, usually, assembly devices with hydraulic clamping mechanisms are used, which makes it possible to reduce the execution time of this technological process.
Welding
We will dwell on the subtleties of this stage in more detail in the next section of our article.
Automatic welding of I-beam elements
Correction of structural elements of the finished product
Production of any designs with the use of welding involves strong heating, which inevitably leads to deformation of individual components of the product. Welded beam is no exception, having an I-beam section. Usually, in such beams after the end of the welding process there is an effect of "mushroom", which is expressed in the violation of the geometry of the shelves of the I-beam. To correct this defect, just the necessary editing operation, which consists in rolling the welded beam through the rollers of a special camp. After performing this procedure, get an I-beam, the geometry of which is clearly observed.
How to weld I-beams
Assembly equipment assembly, used for the manufacture of welded beams, having an I-beam section, determined by the welding method for the formation of belt seams. The choice of such equipment also depends on it, what devices are planned to be used in the production process. At the modern enterprises for formation of long belt seams of I-beam welded beams automatic welding under a layer of flux is most often used.. This method allows you to get welds, differing in high quality and reliability on all their length.
Quarrel beam as a stage of its manufacture
The use for the production of I-beams automated equipment for welding under a layer of liquid flux can not only reduce the cost of finished products, but also to ensure its high quality and reliability. The principle of operation of such equipment provides, that unmelted flux, which protects the welding zone, is under pressure. This minimizes splashing of liquid metal from the welding zone, that allows to carry out this operation qualitatively even at high values of current strength (to 4 thousand Amperes). exept this, flux protects the molten metal from rapid cooling, which contributes to more efficient removal of gas from it.
Meanwhile, welded beam can be made using manual arc and semi-automatic welding. In such cases, special conductors with clamping elements are used for their assembly, or ordinary potholders and clamps. However, it should be borne in mind, that in this case will have to face large losses of molten metal, which will occur due to its spraying and soot. Such losses can reach 30%.
Welding installations, used in the manufacture of I-beams
in addition, that in the manufacture of welded beams of I-beam section it is necessary to perform welding between their main structural elements - shelves and walls, it is also often necessary to connect ready-made beams. In such cases, the beams are joined by butt welding and the following equipment can be used to perform such an operation..
Portal and console type equipment
On such equipment, in addition to the welding head itself, devices can be mounted, providing control over the quality of the resulting seam, supply and removal of flux. The great advantage of such equipment is that, that the quarrel with him is performed at an angle to 45 degrees, which guarantees excellent weldability of parts and obtaining a seam with a good leg.
Cantilever CNC welding machine
Welding manipulators
Welding manipulators allow to automate the welding process, for their complete set it is possible to use various hinged equipment. Example, the working body of such a manipulator can be an automatic head, performing welding in a protective gas environment or under liquid flux. The versatility of welding manipulators allows you to solve a variety of problems, related to the welding process.
Self-propelled welding tractors
The simplest type of equipment, which can be used for welding long I-beams. However, it is advisable to use welding tractors only in the manufacture of beams in small batches.