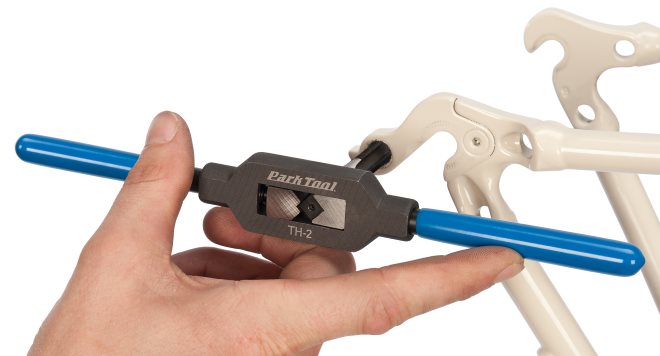
The diameter of the drill for threading: table of sizes according to GOST
Though, that cutting an internal thread does not belong to complex technological operations, there are some peculiarities of preparation for this procedure. So, it is necessary to accurately determine the dimensions of the preparatory hole for cutting the thread, and also choose the right tool, for which special tables of diameters of drills for threads are used. For each type of thread, you need to use the appropriate tool and calculate the diameter of the preparatory hole.
The diameter of the thread and the through hole must meet the standards, otherwise, the grooves will be too small and the threaded connection will be unreliable
Types and parameters of the thread
Parameters, according to which carvings are divided into different types, is:
- diameter calculation units (metric, inch, etc);
- number of thread events (one-, two - or three-west);
- form, in which profile elements are made (triangular, rectangular, round, trapezoidal);
- direction of lifting turns (right or left);
- place of placement on the product (external or internal);
- surface shape (cylindrical or conical);
- appointment (fastening, fastening and sealing, undercarriage).
Metric thread parameters
Depending on the parameters listed above, the following types of threads are distinguished:
- cylindrical, which is denoted by the letters MJ;
- metric and conical, denoted by M and MK, respectively;
- trumpet, for which the letters G and R are used;
- with a round profile, named after Edison and marked with the letter E;
- trapezoidal, denoted by Tr;
- round, used for installation of sanitary fittings, - Cr;
- tenacious and stubborn strengthened, labeled as S and S45 respectively;
- inch thread, which can also be cylindrical and conical, – BSW, UTS, NPT;
- used to connect pipes, installed in oil wells.
Thread types according to GOST standards
Application of the tap
Before starting threading, it is necessary to determine the diameter of the preparatory hole and drill it. To facilitate this task, the corresponding DSTU was developed, which contains tables, that allow you to accurately determine the diameter of the hole for the thread. This information makes it easy to choose the size of the drill.
To cut a metric type thread on the inner walls of the hole made with a drill, a tap is used - a screw-shaped tool with cutting grooves, made in the form of a rod, which can be cylindrical or conical in shape. There are special grooves on its side surface, are located along its axis and divide the working part into separate segments, which are called combs. The sharp edges of the combs are precisely the working surfaces of the tap.
Mitchik: construction and parameters
So that the turns of the internal thread come out clean and neat, and its geometric parameters corresponded to the required values, it should be cut gradually, by gradually removing thin layers of metal from the treated surface. That is why taps are used for this purpose, the working part of which is divided along its length into sections with different geometric parameters, or sets of such tools. Single taps, the working part of which has the same geometric parameters along its entire length, needed in those cases, when it is necessary to restore the parameters of an already existing thread.
Minimal set, with the help of which it is possible to perform the processing of the holes for the thread with sufficient quality, there is a set, consisting of two taps - draft and clean. The first cuts a thin layer of metal from the walls of the hole for cutting the metric thread and forms a shallow groove on them, the second not only deepens the formed groove, but also cleans it.
Types of taps for threading and their differences
Minimum set of taps
Combined two-way taps or sets, consisting of two instruments, used for thread cutting in holes of small diameters (to 3 mm). To process holes for a metric thread of a larger diameter, it is necessary to use a combined three-pass tool or a set, consisting of three taps.
For manipulations with the tap, a special device is used - a turner. The main parameter of such devices, which may have different design, is the size of the landing hole, which must exactly match the tool shank size.
Some varieties of collars for taps
When using a set of three taps, which differ both in their construction, and geometric parameters, the sequence of their application should be strictly followed. They can be distinguished from each other by special risks, applied to the shanks, as well as by structural features.
- Mitchik, with which the hole for cutting the metric thread is processed in the first place, differs in the minimum diameter among all tools of the set and cutting teeth, the upper part of which is strongly cut.
- The second tap has a shorter intake part and longer ridges. Its working diameter is intermediate between the diameters of other tools in the set.
- The third tap, with which the hole for cutting the metric thread is processed last, characterized by full ridges of cutting teeth and diameter, which must exactly match the size of the formed thread.
A set of three taps
Taps are mainly used for cutting metric type threads. Much less often, than metric, tags are used, intended for processing the inner walls of pipes. They are called tubular in accordance with their purpose, and you can distinguish them by the letter G, present in their labeling.
Internal thread cutting technology
As mentioned above, before starting work, you need to drill a hole, the diameter of which must fit exactly under the thread of a certain size. It should be borne in mind: if the diameters of the holes, intended for cutting metric threads, selected incorrectly, then this can lead not only to its poor performance, but also until the tap breaks.
Given that fact, what a tick, forming helical grooves, not only cuts metal, but also overcomes it, the diameter of the drill for threading should be slightly smaller, than its nominal diameter. Example, the drill bit for threading M3 should have a diameter 2,5 mm, under M4 - 3,3 mm, for M5, you should choose a drill with a diameter of 4,2 mm, for M6 thread - 5 mm, M8 – 6,7 mm, M10 – 8,5 mm, and for M12 – 10,2.
Table 1. The main diameters of the holes for the metric thread
Table 2. Hole diameters for inch threads
All diameters of drills for threading are given by GOST in special tables. In such tables, the diameters of drills for threading are specified as with the standard one, and with a reduced step, it should be kept in mind, that for these purposes holes of different diameters are drilled. in addition, if a thread is cut in products made of brittle metals (such, example, like cast iron), the diameter of the drill for the thread, obtained from the table, must be reduced by one tenth of a millimeter.
Familiarize yourself with the provisions of DSTU, which regulate the cutting of metric threads, it is possible, by downloading the document in pdf format at the link below.
GUEST 19257-73 Holes for cutting a metric thread. Diameters
Download
The diameters of drills for metric thread can be calculated independently. From the thread diameter, which needs to be cut, it is necessary to subtract the value of its step. The threading step itself, the size of which is used in performing such calculations, can be found out from special compatibility tables. To determine, what diameter hole must be made with a drill in that case, if a three-way tap will be used for threading, the following formula should be used:
Do = Dm x 0,8, where:
To is the diameter of the hole, which must be done with a drill,
Dm - the diameter of the tap, with which the drilled element will be processed.
Scheme of tapping the internal thread with a tap
collars, into which a threaded tap is inserted, can have the simplest design or be equipped with a ratchet. Work with such devices with tools fixed in them should be done very carefully. To get high-quality and clean carving, clockwise rotation of the tap, done in a half-turn, it is necessary to alternate with turning it one fourth of a turn against the direction of the thread.
The thread will be cut much easier, if lubricant is used during this procedure. Oil can play the role of such a lubricant when cutting threads in steel products, and when processing aluminum alloys - alcohol, turpentine abo gas. If such technical fluids are not at hand, then you can use ordinary machine oil to lubricate the tap and cut the threads (however, it has less effect, than the substances listed above).