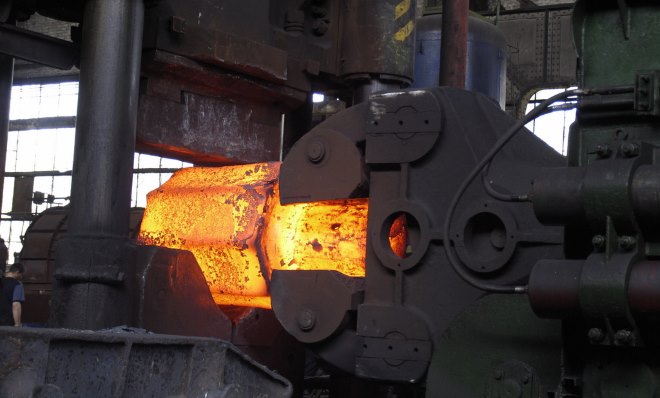
Hot stamping of metal: technology and equipment
Hot stamping, which involves the deformation of the metal workpiece in the heated state, used for that, to change not only the configuration of this workpiece, but also its size. Most often, such a technological operation is used for this, to change geometric parameters in more than one plane, and in several dimensions. In such cases, this procedure is called "hot volume stamping".
Hot stamping is commonly used in mass production, where a large amount of work is required
The essence of technology
The essence of the process of hot stamping is, that the finished metal product is obtained from heated to a certain temperature of the workpiece, affecting it by pressure, for which a special stamp is used. When performing hot stamping, the temperature of the workpiece changes from the state of simply heated surface to the forging. To limit the flow of heated metal in the wrong direction, in some parts of the inner surface of the stamp perform special cavities and protrusions. So, the inner surface of the stamp forms a closed cavity (stream), the configuration of which fully corresponds to the shape of the finished product.
This is what the bottom of a simple one-handed stamp looks like
Hot volume stamping (GOSH) is performed on metal bars of different profile - square, rectangular, round or periodic. In some cases, the production of finished products by hot stamping technology can be performed from a solid metal rod. Initially, its part is formed into a forging with the necessary geometric parameters, and then it is separated by cutting. However, usually, blanks for hot stamping are cut from a metal rod.
The greatest efficiency of stamping of details, provides for their preheating, demonstrates in serial and mass production. In particular, there are a number of advantages in the use of this technology for the production of metal products in large and mass series.
- Metal waste, from which products are made, are reduced.
- Labor productivity increases.
- With this technology you can make products even in very complex configurations.
- Finished products, obtained by hot stamping of metal, differing not only in the special accuracy of geometric parameters, but also high surface quality.
The scheme of technological process of production of a detail like "rod" by a method of hot volume stamping
The technological process of hot stamping includes a large list of operations, performed from the moment of loading of a metal part into the processing area and ending with unloading from the equipment of the finished product. Designing such a process involves following such an algorithm:
- choose a method, on which the product will be made: on stamps with open or closed stream;
- develop a detailed drawing of the finished forging;
- to install, for how many transitions you can make the finished product;
- for each transition to develop a drawing of a molded forging;
- depending on the required capacity for each stage of the technological process to select the appropriate equipment and form stamps;
- heat the workpiece before hot stamping, selecting the heating method and modes of execution;
- depending on the requirements for the quality of the finished product to determine the list of finishing operations, which will be subjected to forging.
At the final stage of development of the technological process it is necessary to calculate its economic and technical indicators.
At the final stage of development of the technological process it is necessary to calculate its economic and technical indicators
Metal processing, performed by hot stamping, can be carried out by different technologies, features of the implementation of which depend on a number of parameters: type of equipment used, geometric parameters and molded material of manufacture of the product. The following types of parts can be manufactured using GOS technology.
Elongated
Shafts of various function can act as such products, connecting rod, levers and other details of a similar design. For their production use a stamping press. They are processed by a method of hot stamping by a plasma, while the original workpiece is subjected to the operation of broaching. The final stage of production is shaping by free forging, performed in prefabricated forging rollers rollers.
Disk
These are gears, bushings, hub, lids and other details of round or square configuration, differing in relatively short length. To make products of this type, use precipitation technology, which is performed at the end of the workpiece. To implement this technology it is necessary to use stamping transitions.
Examples of products, made by hot volume stamping
Stamping streams
When processing preheated steel products, as in the stamping of brass, use stamping streams, which can be:
- linger (with their help increase the length of individual sections of machined parts: from that part of the workpiece, which must be extended, applied frequently, but weak blows, at the same time edging of the processed detail is carried out);
- procurement (their purpose is to shape the workpiece: the metal is redistributed in its total amount for that, to give the finished product such a shape, which ensures minimal waste of material);
- pinch (they are performed to reduce the height of a particular section of the workpiece while increasing its width);
- rolling (streams, in which the metal of the workpiece is evenly distributed along its axis, at the same time the diameter of its separate sites increases);
- bending (in them the workpiece comes with a curved axis, forging is formed, the bending angle of which is 90 °).
Stages of complex stamping in several streams
To stamping streams, in which the manufactured element acquires the desired shape, include:
- previous, or drafts, in which the shape of the workpiece is as close as possible to the configuration of the forging (features of such a stream, which may or may not be used when performing hot stamping, are, that it has a slightly increased depth, also in it, compared with the parameters of the finished product, increased slopes and radii of curvature);
- clean, in which the part acquires its final shape, but its dimensions are increased by the amount of shrinkage of the metal during its cooling (as in such streams on preparation it is necessary to give the maximum efforts, place them in the central part of the stamp).
Technological schemes of stamping
Of the currently used schemes of hot stamping should be distinguished only two.
closed stamping
This is a technological operation, performed in the stamp, the gap between the moving and fixed parts of which is minimal. Hot stamping by this method can be performed on presses, when the upper part of the stamp is equipped with a protrusion, and the cavity - the bottom, or on hammers, when the cavity is at the top of the working tool, and the protruding part - in the bottom. The use of stamps of this type requires it, that the volumes of forging and the finished part exactly match. Stamps of the closed type can have more than one, and two connector planes, located at right angles to each other.
Stamping in the closed stamp one-handed
Open stamping
There is a special gap between the moving and fixed parts of the hot stamping stamp of the open type, in which excess metal is extruded, formed in the process of its deformation. Open type stamps, which is a big advantage, can be used for forgings of any kind.
The scheme of stamping in open dies
The use of closed stamps also has its advantages, which are as follows.
- Finished parts have a more homogeneous internal structure and high quality of the outer surface.
- Due to the lack of shrinkage metal consumption is reduced.
- You can make products from metals, characterized by low plasticity, since such processing is carried out under the influence of high voltage and uneven comprehensive compression.