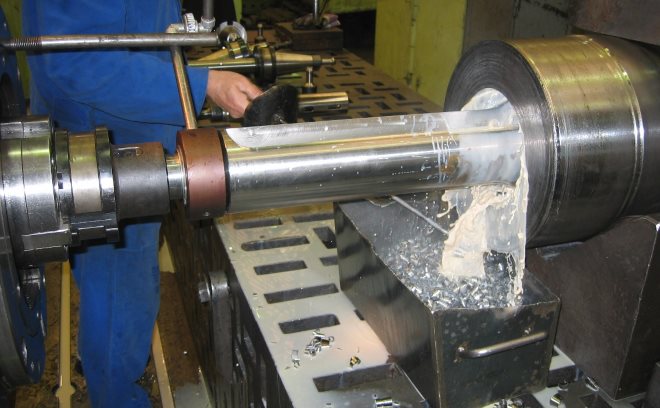
Cannon drills and drills for deep drilling: see, GUEST
The gun drill is a tool, by means of which drilling of through and deaf openings is carried out, differing in considerable depth. Holes of this type are made in shafts for various purposes, in spindles, as well as in other details, characterized by considerable length. Not only gun drills are used for this purpose, but also, in particular, single-edged and double-edged drills with internal chip removal. Drilling with the help of the latter is characterized by low productivity, but deep holes are characterized by high purity, accuracy of geometric parameters and straightforwardness.
The process of deep drilling at the turning and milling center
Features of drilling deep holes
Drilling is called deep in that case, if the depth of the hole exceeds five of its diameters. This technological operation is highly complex and time consuming, and the main condition for its quality performance is effective cooling of the tool, which, usually, carried out under pressure.
To perform deep drilling efficiently and accurately, it is very important to ensure the correct direction of the tool at the very beginning of processing. To do this, use a special conductor sleeve or perform this procedure on pre-made holes of smaller diameter.
Due to technical difficulties, deep drilling should be performed on special equipment
Drill, used for deep drilling, cannot be rotated at full speed outside the workpiece itself: this can shift the cutting part from the required trajectory. in addition, when drilling deep holes with a long drill creates unfavorable conditions for the removal of chips from the processing area, which can also cause the tool to deviate from the specified direction.
Types of drills for deep drilling
As a drill for deep drilling can be used:
- spiral with a cylindrical shank, parameters of which are regulated by GOST 886-77 (on the design spiral drills with a cylindrical shaft concern tools of a long series, with which to create holes with depth, exceeding the value, equal 15 diameters);
- rifles, the cutting part of which is made entirely of hard alloy;
- rifles, on the cutting part of which carbide plates are fixed by soldering;
- rifles, equipped not only basic, but also intermediate carbide plates;
- ejector, which are used to perform deep drilling on machines with a horizontal arrangement of the cutting tool;
- cannon, on the surface of which there is a V-shaped groove, designed to remove chips (machining with drills of this type is an outdated method of obtaining deep holes).
Drills for deep drilling
It is possible to get acquainted with requirements of GOST to drills of a long series, by downloading the document in pdf format at the link below.
GUEST 886-77 Spiral drills with a cylindrical shank. Long series. Basic dimensions
Download
Twist drills with a cylindrical shank, manufactured in accordance with the requirements, which provides GOST 886-77, differ in the extended working part. In accordance with the provisions of the above standard from the 77th year, such an elongated tool can be made entirely of high-speed steel or equipped with cutting inserts, made of hard alloy.
GUEST 886 from the 77th year also determines, that cooling of drills of this type can be provided at the expense not only external, but also the internal supply of coolant. Twist drills, as indicated by GOST 886-77, can be made not only with a cylindrical shank, but also with conical shanks. The process of deep drilling, carried out using such drills, can be performed as with their periodic extraction from the performed hole, what is needed to remove from it formed chips, and without performing such a procedure. If you compare twist drills with armed and cannon, then when using the first drilling performance increases almost in 8 times.
Examples of working heads of rifle drills
Cannon and rifle drills are tools of the single-cutter type, with which you can create deep holes with diameters, in the range of 0.5-100 mm. Cooling of drills of this type is carried out through an aperture, made in their inner part, and the shavings, formed during processing, is taken away by means of a special groove, performed on their outer surface. Cannon and rifle drills, equipped with carbide cutting inserts, differ in the conical configuration of the working part, which provides the best direction of the tool in the area of processing.
Ejector drills are more modern means of deep drilling. Due to the lack of chip grooves on their outer surface, they are highly rigid.
The principle of operation with an ejector drill
How to choose the right tool
Choosing drills for deep drilling, a number of factors should be considered:
- diameter and depth of the hole, which must be performed;
- characteristics of the processed material;
- type of equipment, which will be used to perform processing.
The scheme of calculating the length of the drill when working on a universal machine
It should be borne in mind, that device, on which such drill will be established, should be designed specifically for deep drilling.
Before drilling, the optimum speed of rotation and feeding of the cutting tool should be selected, and ensure its efficient cooling. For processing materials, which in the process of cutting them form a long chip, it is best to use a drill with polished chip grooves.
Rifle drills can be single or double sided cutting
Stages of technology
The process of deep drilling of holes is performed in the following sequence.
- First of all, with the tolerance of H8 perform a pilot hole.
- Tool, rotating at low frequency, brought to the surface of the workpiece.
- Include the required speed of the drill and the speed of its supply, provide the supply of MPA in the processing area.
- The hole is drilled to the desired depth without removing the tool.
- If a very long tool is used for deep drilling, then the first 25 mm depth holes are processed at low cutting modes - 75% from nominal.
- After reaching the required drilling depth, the supply of coolant to the processing area is turned off.
- After drilling, the tool is quickly removed from the machining area and its rotation is stopped.
There are several other technologies for drilling deep holes, but the most common of them are listed above, which is used in most cases.