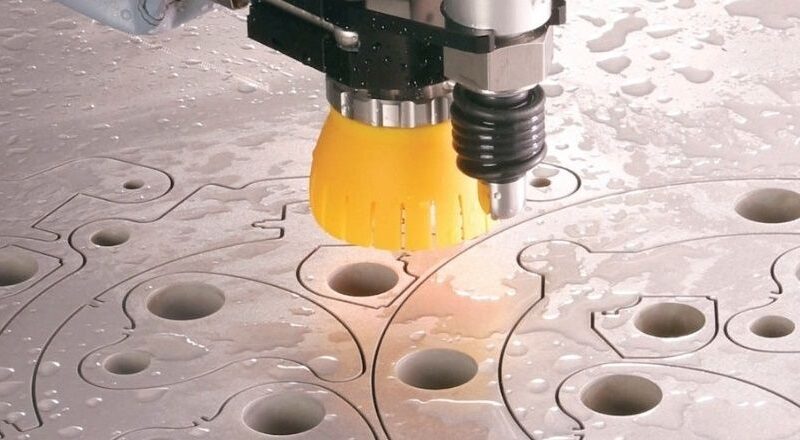
Hydroabrasive cutting of metals - technology, machines, video
Equipment is mandatory at any machine-building and metal-working enterprise, that allows to carry out cutting of sheet metal. Very often the technical capabilities of the most common types of such equipment is not enough, to ensure high quality cut.
The process of cutting hydroforming
The essence of technology
Hydroabrasive metal cutting is not an innovative technology, its use began in the 1960s. The first machine to perform such cutting began to use the American aircraft company. The management of this company made an official statement about this method, describing its advantages and recommended its use for cutting metal and other materials, having high hardness. Since then, abrasive cutting of metal using water has been actively used by enterprises and is gaining popularity.
The essence of this technology is, that water is supplied to the cutting zone under high pressure, which includes abrasive substances. Any installation of hydroabrasive cutting works according to the following scheme.
- Water and abrasive material are fed into the mixer of the device from a special tank, which is used mainly fine sand.
- After mixing, the water with the abrasive enters the nozzle of the installation.
- A thin jet of hydroabrasive mixture is formed in the nozzle, which under high pressure is fed into the cutting zone.
The principle of hydro-cutting
Technology, implemented according to a similar scheme, allows not only to perform cutting quickly and with high quality, but also save significantly on consumables, the most expensive of which is ordinary sand. It should be noted, that the speed of abrasive cutting with water is comparable to plasma technology, and the quality of the resulting cut - with a laser.
Areas of application
This technology has significant differences from all other methods of separating sheet metal. When using this method, the surface of the processed metal does not experience pressure and mechanical impact of another type. Due to this, there is no friction in the cutting area, in accordance, heating of the tool and a surface of a detail is excluded, which has a positive effect on the quality of processing and significantly expands the scope of such technology.
Most often, abrasive cutting with water is used to separate sheet metal, but recently this method is increasingly used for processing other materials, which include:
- natural stones (granite, marble, etc.);
- Ceramic tile, sheets of glass;
- carbon and stainless steel, titanium and other metals;
- reinforced concrete structures;
- various polymeric materials and rubber.
The use of hydroabrasive cutting technology minimizes material consumption, which is its significant advantage. in addition, abrasive and water cutting is the only possible way to separate metal in enterprises with high fire and explosion hazards.
Equipment for hydroabrasive cutting
Essentially, the ability of water to destroy various materials is used in devices for hydroabrasive cutting, noticed in antiquity. To make such destruction more accurate, fast and efficient, it is necessary to increase the pressure, by which water with abrasive affects the material, and also to give the received stream the necessary direction. In modern machines for hydroabrasive cutting, such problems are solved using the following elements and methods.
Hydroforming cutting allows you to cut materials of considerable thickness
High pressure pump
The pump in such devices accumulates liquid with abrasive and delivers this mixture to the surface of the workpiece. Productivity of such machines and thickness of a detail, which they can cut, depend on the power of the pump used.
Power regulator
Hydroabrasive cutting machines with such a regulator can cut using working mixtures of different composition, supplied under controlled pressure, which makes it possible to process them with materials of different thickness and structure. So, for cutting harder materials use three-component hydroabrasive mixtures, and for more viscous ones, they consist of two components.
Changing the nozzle of the device
This technique involves the selection of materials of different thicknesses, composition and density of the nozzle of a certain design.
Use of faucets
It is this element, which every modern hydroabrasive machine is equipped with, is responsible for the quality and uniform composition of the working content and, in accordance, for accuracy and speed of cutting, as well as the ability of the device to process thick parts.
Automation of the cutting process
When cutting metal due to the inertia of the jet of working fluid necessarily forms a conic edge, which is directly proportional to the speed of the processing. To minimize this side effect, on modern hydroabrasive devices automatic systems are used, which, depending on the density of the processed material, adjust the angle of the nozzle.
Prepare water before using it for cutting
The quality of the water used can affect the results and speed of cutting. That is why all modern machines use systems for pre-treatment of water from impurities.
In addition to basic systems and components, devices for hydroabrasive cutting can be equipped with additional equipment, which significantly expands the functionality (it is said, in particular, about execution of figured cuts).
Modern equipment, which performs cutting of materials by a hydroabrasive way, allows:
- perform accurate and high-quality cutting at different angles;
- cut even the most complex parts without human intervention - with software control;
- work with metal parts even of considerable thickness (steel - to 20 mm, titanium - do 17 mm, high-strength alloys - to 12 mm, copper and its alloys - to 5 mm);
- get curly cuts, which is very important in the production of decorative products;
- perform pipe cutting (it is possible on separate models of hydroabrasive devices).
The machine for hydroformative cutting of pipes
Hydroabrasive cutting machines with numerical program control
The machine for hydroabrasive cutting, equipped with numerical program control (ЧПУ), that allows to solve effectively problems on cutting of various degree of complexity. High accuracy, with which carries out cutting such machine allows to make even the most difficult details and considerably to minimize a material expense. The technological process of cutting with this device is as follows.
- Special software is installed on the machine for each part, which controls all cutting parameters: the composition of the working mixture, its pressure, etc.
- Hydroabrasive cutting machine with software control, which provides constant control of quality of a cut and adjusts operating modes, if necessary. Such options of the similar equipment promote it, that no additional processing of finished products, including grinding, after it is not required.
- CNC machines can drill holes, as well as perform a whole list of specific operations.
Hydroabrasive cutting machine - OMAX 60120
Execution of hydroabrasive cutting by manual method
Manual machines for hydroabrasive cutting differ from automated ones, that all processing parameters are set in them, controlled and adjusted by the operator. Despite some inconveniences of operation, compared to CNC equipment, such machines have a number of advantages.
- For maintenance of such machines, characterized by ease of management and minimum functionality, no specialized education required.
- Functionality, which are possessed by manual installations of hydroabrasive cutting, allow to make qualitative and exact details of simple geometrical forms.
- The manual machine for hydroabrasive cutting differs in reasonable cost (on average in 1,5 times cheaper than CNC machines).
Meanwhile, for cutting parts of complex geometric shapes and require particularly high accuracy of the obtained dimensions, it is necessary to use CNC machines.
Cutting complex shapes
Required materials
At hydroabrasive cutting two basic materials are spent, the completion of which must be constantly monitored:
- fine fractional abrasive material, as which pomegranate sand is most often used,differs in especially high hardness (the size of the grains of such sand should not exceed 600 micron);
- water, which has undergone preliminary purification from impurities.
Naturally, that these are not the only materials, necessary for cutting using water and abrasive. Power supply is required for any waterjet machine, supply of compressed air and replacement of worn elements, to which, in particular, include:
- system elements, which is responsible for feeding the abrasive mixture: nozzle, supply tubes, etc.. (if you do not replace the worn nozzle in time, then the hole in it can increase significantly in diameter, which will reduce the accuracy of the dimensions of the molded cut).
- sealing elements of the pump station, sealing elements of the pump station.
It should be borne in mind, sealing elements of the pump station, sealing elements of the pump station, leads not only to a decrease in the quality of finished products, but also to the accelerated wear of cutting machines.
Advantages and disadvantages of cutting with abrasive and water
Evaluate effectiveness, productivity and accuracy of hydroabrasive cutting can be even video of such process. Meanwhile, there are not only visually assessable benefits of this technology, to which they belong:
- exclusion of heating of the processed detail (hence the impossibility of its deformation and, in accordance, high cutting accuracy);
- wide functionality of the equipment, with which you can solve problems of even the highest complexity;
- no need for additional work to refine the resulting products;
- versatility, which has any machine for hydroabrasive cutting (with its help you can cut rubber, plastic, stone or metal, and drill holes in different materials);
- high speed, accuracy and cost-effectiveness of the process;
- exceptional process safety, including its explosion - and fire safety;
- possibility of cutting of details of big thickness, including tubular cross section.
Hydroforming cutting of marble
How effective and efficient was the process of hydroabrasive cutting (div. video at the end of the article), there are disadvantages to this technology. In particular, these include the following.
- When cutting the conicity of the edge of the cut part is formed. This disadvantage is especially noticeable when cutting thick parts. To prevent this defect, it is necessary to use special automated devices, correcting the angle of the nozzle during processing.
- On hydroabrasive machines process as thick-walled, and thin-walled parts with one speed, which somewhat reduces the profitability of such technology. To increase profitability, thin details are cut into several pieces at once, folding them into a bundle.
The use of hydroabrasive cutting is especially advisable in those situations, when it is necessary to cut complex parts with particularly high accuracy, while spending a minimum amount of time.