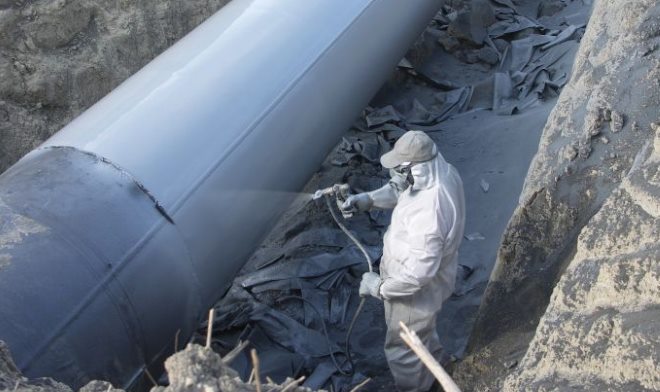
Cold galvanizing of metal: technology, warehouses, GUEST
Cold galvanizing is a technique, by means of which the surface of a metal product can be effectively protected from corrosion. The essence of this technology is, that a special mixture is applied to the metal, in the chemical composition of which a large amount of zinc.
Cold galvanizing of the main gas pipeline
You can get acquainted with the requirements of GOST for the process of cold galvanizing, by downloading the document in pdf format at the link below.
GUEST 9.305-84 The only system of protection against corrosion and aging. Metallic and non-metallic inorganic coatings
Download
An alternative to traditional galvanizing methods
Galvanized, according to most experts, is one of the best ways of corrosion protection of metal structures. Application of methods of galvanic and hot-dip galvanizing allows to provide anticorrosive protection of metal for decades (to half a century). Meanwhile, it is not always possible to use such galvanizing methods, as it requires significant financial investment in special equipment and technological equipment.
In all cases, when the use of traditional methods of coating metal with a layer of zinc is associated with certain difficulties, a good alternative is cold galvanizing of metal. When cold surface galvanizing on a metal product is applied zinc-containing composition. As a result of such processing the layer is formed, anticorrosive properties of which are almost unmatched by the characteristics of coatings, obtained by other methods of galvanizing.
Among the most significant benefits, which has the technology of cold galvanizing, should include the following.
- Paint, used for cold galvanizing, has good adhesion to the surface of the workpiece, and to coatings of any other type.
- Constructions, galvanizing which is carried out by means of a cold method, can have any geometric parameters and shapes.
- The method of cold galvanizing does not require significant financial costs to prepare products for processing.
- Metal details, which have been galvanized by this technology, well amenable to welding.
- The composition for cold galvanizing can be applied even at home, for which you can use a spray gun, paint roller or even an ordinary brush.
- This method of zinc metal coating does not require dismantling of the workpiece, there is no need to transport it to the place of processing, and then deliver back and perform installation.
Galvanized, conducted by cold technology, has another important advantage. It is, that such a process can be carried out in a fairly wide range of temperatures: from -20 up to + 40 °. Meanwhile, the zinc protective layer, obtained by this technology, characterized by insufficient resistance to mechanical damage, which can be considered a disadvantage of this method of galvanizing. However, given that fact, that the damaged coating can be repaired at any time, using a composition for cold galvanizing, such a shortcoming can be considered insignificant.
Features of technology
Used for cold galvanizing paints - various zinc-containing mixtures. Requirements for them, as with any zinc coating, obtained by various technologies, regulated by GOST 9.305-84. So, this document states, that cold galvanizing can be performed on any metal products and structures, except those, made of high-strength steels or magnesium alloys.
That as a result of performance of cold surface galvanizing to receive on a metal product or a design a layer with high protective properties, it is necessary to carefully prepare the treated surface.
This is the preparation, according to the Guest, in performing the following procedures.
- Coked areas are removed from the treated surface, pollution of various natures, salt residues, damage, caused by the influence of natural factors.
- The metal is given the required level of roughness, for which abrasive jet can be used, hydroabrasive or hydrodynamic treatment. In this way, oxidation and rust products can also be removed from the product.
- Finishing manual cleaning of metal is carried out, performed to remove welding splashes from it, sharp edges and burrs.
- Products with dust residues are removed by a stream of compressed air.
Stages of cold galvanizing
In order for the galvanized layer to have good adhesion to the treated surface, it should be free of grease and oil stains. If there are such spots, they must be removed before cold galvanizing, for which solvents of the hydrocarbon group are used. GUEST, in particular, determines the following requirements for the quality of preparation of the treated surface.
- The number and size of dust particles, preserved on the surface of the product after dedusting, must meet the requirements of the ISO standard 8502-3.
- The level of degreasing of the surface, which is checked by means of a luminescent technique, must meet Gost 12.2.052.
- The degree of surface roughness, is checked by means of a profilometer or a comparator, must meet the requirements of the ISO standard 8503-1.
Cold galvanizing of a car body by own forces
After checking the quality of preparation for cold galvanizing, you can apply liquid zinc to the product - a special mixture, which contains metal. Using different paints or mixtures with a zinc component, you should pay attention to that, at what air temperature they are recommended by manufacturers. It should also be borne in mind, that the temperature of the treated surface must be at least 3 ° higher, than the dew point. If you ignore this requirement, you can face that, that moisture will condense on the surface of the processed product, which will significantly worsen the characteristics of the applied coating.
To determine the dew point, that is required not only for cold galvanizing, you can use different measuring instruments, which include the hygrometer, thermometer, psychrometer or special measuring devices. Indications of devices, obtained from such measurements, are compared with the data of reference tables. This accurately determines the dew point for a particular case.
Dependence of dew point on temperature and relative humidity
Zinc paint can be applied in several layers. Very important, that each new layer is applied only after, as the former dries to the manufacturer's specified degree composition. Each layer of cold galvanizing paint should be applied as evenly as possible. Cold galvanized, as mentioned above, can be performed using a pneumatic spray or airless method. Usually, the last way, which involves the use of rollers or brushes, used in those cases, when the protective coating must not be applied to the entire surface of the product, but only on its separate sites.
The thickness of the formed protective layer, as well as the degree of its adhesion to the treated surface must be checked, for which special measuring devices are used. in addition, visual control of the applied covering is carried out, which allows you to assess its decorative characteristics, as well as to detect defects and poorly treated areas.
Used compositions
Cold galvanizing can be performed using different compositions, the choice of which is made depending on a number of factors. Such mixtures are used as in production conditions, and for that, to perform cold galvanizing with your own hands at home.
One of the most popular zinc-containing compositions, by means of which cold galvanizing of metalwork is carried out, is "Galvanol". This tool can be processed as external, and internal parts of metal structures, elements of equipment for various purposes.
Packing of structure for cold galvanizing "Galvanol"
Galvanol, which belongs to the category of one-component mixtures, is a liquid solution, containing high purity electrolytic zinc, as well as binders and volatile compounds. "Galvanol" provides a very high degree of protection of the product from cold galvanizing.
To the significant benefits, owned by Galvanol, should be attributed:
- good adhesion to product surfaces, made of ferrous metals;
- speed and ease of application;
- possibility of use in a wide temperature range: from -30 up to + 50 °;
- possibility of drawing on a rusty surface (provided, that the rust on them holds quite firmly);
- possibility of use even at the increased humidity of ambient air.
Technical characteristics of Galvanol composition
Zinc coating, for the formation of which was used "Galvanol", retains its protective properties when interacting with ethyl alcohol vapors, salt solutions, sea and fresh water. It is also important, that such a composition for cold application of zinc provides double protection against corrosion - natural (passive) and cathode (active).
Another common composition, by means of which cold galvanizing is carried out, is "Cinotan". It can be used as a complex protection system, where it acts as a primer layer, and as a separate protective coating. Coating, formed using this zinc-containing composition, retain their protective properties in constant contact with highly polluted atmosphere and salt water.
Technical characteristics of the composition "Cinotan"
Most often, "Cinotan" is used for coating:
- elements of hydraulic structures;
- tanks for storage of refined products;
- elements of enclosing structures;
- tanks and pipes of cold and hot water supply;
- pylons of power lines (LEP);
- industrial structures for various purposes;
- auto - and railway facilities.
An important advantage of "Cinotan" is that, that such a composition can be used in almost all climatic zones of our country. It is no coincidence that the companies made their choice in favor of this composition, who are the leaders of the domestic economy: "RUSSIAN RAILWAYS", Gazprom and others.
When choosing a composition for cold galvanizing should listen to the feedback of people, actually tested the technology
Among the popular mixtures, used to perform cold galvanizing, should also be included:
- "Master AK-100" (used for machining parts of vehicles, including car bodies, various building structures, bridges and transmission line elements);
- "CVES" (components of this composition for cold galvanizing are ethyl silicate and zinc powder, it is used for processing high-alloy steels);
- "Cinoterm" (organosilicon solution, which can be used in combination with various paints and varnishes);
- Cinconol (polyurethane primer, which contains zinc and allows to obtain coatings with high protective properties, increased thermal stability and elasticity).
Deciding, which technology to choose - hot or cold galvanizing, - should be borne in mind, that design, on which the protective zinc layer is formed by the cold method, can last even longer than that, for the processing of which another method was used. The cost of cold galvanizing is lower, and this procedure is much easier, than hot-dip galvanizing or galvanizing.