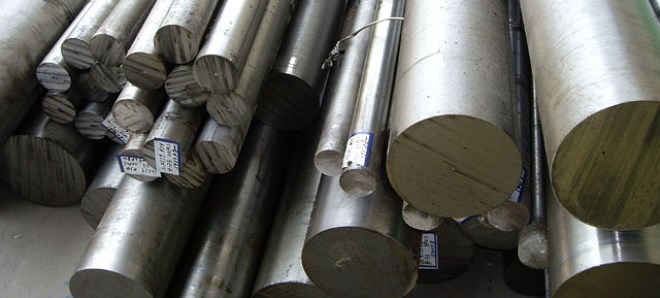
Tool steels - brands and areas of application
Wear-resistant tools and parts, the strength of which is subject to increased requirements, involve the use of tool steels, having a number of important differences from structural steels.
Round blanks of tool steel
Areas of application of tool steels
Tool steel is an alloy, the carbon content of which is not less 0,7%. Its structure may be pre-eutectoid, ledeburite or eutectoid. Інструментальні сталі з різною структурою відрізняються наявністю вторинних карбідів. In alloys with pre-eutectoid structure there are no secondary carbides. Meanwhile, carbides must be present in each of these structures: they are formed by eutectoid modifications or are the result of the decay of martensite.
Scheme-classification of tool materials
У сучасній промисловості інструментальні сталі знайшли широке застосування. They are used for production:
- working parts of stamps, working on the principle of cold and hot deformation;
- high-precision products;
- cutting tool;
- measuring instruments;
- foundry molds, working under pressure.
Depending on the field of application of tool steels, there are certain requirements for them. However, there are eligibility criteria common to all brands:
- sufficient viscosity (this characteristic is especially relevant for details, exposed to shocks during operation);
- high strength;
- durability;
- high level of hardness.
Options for using tool steels (on the example of carbon)
NameBrain steelApplication
carbon instrumental | U7 U7A |
Hammers, core, screwdrivers, teeth, blacksmith's tool, hair |
carbon instrumental | U8 У8А |
Scissors, chopping knives, hand carpentry tools, frame saws |
Carbon instrumental, high hardness | У10 U10A |
Drills, cutters of small diameter, band saws, sweeps |
Carbon instrumental, high hardness | U12 U13 |
Turning wood cutters, hacksaw blades on metal, files, files, engraving tool |
Brands of alloys, intended for use in conditions of cold deformation, must, in addition to everything else, have a smooth working part, ability to maintain size and shape, as well as differ in the limit of fluidity and elasticity. And tool steel, suitable for hot deformation, must have high thermal conductivity, resist the holidays and be resistant to temperature fluctuations. Steel grades must also meet special requirements, used for the production of cutting tools.
Requirements for tool steels
The following requirements apply to all carbon tool steels, as:
- well processed by metal cutting;
- low sensitivity to overheating;
- low susceptibility to the processes of adhesion and welding to workpieces;
- well polished;
- susceptibility to calcination;
- plasticity in the hot state;
- ability to resist decarburization;
- resistance to cracking.
Types of tool steels
All brands of steel for the production of tools are divided into 5 main groups.
Heat resistant and viscous
Usually, it's for- і доевтектоїдних сталі, which contain molybdenum, tungsten and chromium. The carbon content in such alloy tool steels corresponds to medium and low values.
Highly hard and viscous, not heat resistant
Such alloys are characterized by a low content of alloyed elements and medium - carbon. They are also characterized by low hardenability.
Highly hard, heat-resistant and wear-resistant
До таких маркам відносяться швидкорізальні леговані сталі (the content of alloying elements in them is very large), as well as alloys with ledeburite structure, containing more than 3% carbon.
Wear-resistant, високотверді і середньої теплостойкості
Це сталі з заевтектоідной і ледебуритного структурою, which includes 2-3% carbon and from 5 to 12% chromium.
Високотверді і нетеплостойкі
Склад таких інструментальних сталей з заевтектоідною структурою або взагалі не містить легованих елементів, or contains them in small quantities. The level of hardness of such alloys is provided by a large amount of carbon in their composition.
Classification of tool steel in the form of a diagram
An important parameter of tool steels is the level of their hardness. Usually, високотверді сталі небажано застосовувати для виробництва інструменту, which in the course of operation is exposed to shock loading. This is due to the fact, that such alloys have low viscosity and significant brittleness, which may damage the tool, which of them is made.
According to the level of hardness, two categories of tool steels can be distinguished:
- with a high level of viscosity (carbon content within 0,4-0,7%);
- with high wear resistance and hardness (they contain more carbon: 0,7-1,5%).
Detail of a hydraulic hammer made of high-strength steel
Grades of steels are classified according to the degree of their hardenability. За даним критерієм розрізняють леговані сталі з підвищеною (possible annealing diameter 80-100 mm), high (50-80 mm) and low (10-25 mm) hardenability.
About marking of tool steels
Knowledge of marking is required to determine the type of tool steel, which includes both letters, and digital symbols. It is easy to understand this. The letter "U" is very common in the marking of alloys. She means, that in front of you is carbon steel. Figures, following such a letter, talk about the carbon content in the alloy, computational in tenths of a percent. Occurs in the marking of carbon tool steels and the letter "A", which indicates, that the alloy is of high quality.
Marking of tool steel (on the example of carbon) indicating the content of additional elements
A large category of tool steels are high-speed alloys, denoted by the letter "P". This letter is followed by numbers, which can determine the content of the main alloying element for steels of this category - tungsten.
The content of other elements in the composition of high-speed alloy steels (molybdenum, vanadium and cobalt) determined by numbers, next to the corresponding letters in their labeling - "M", "F" and "K". Chromium is a must in high-speed alloys, but its quantity is determined by default - no more 4%.
Very often the marking of tool steels begins with a number (example, 9HS, 9X, 6CHB), which indicates the content (in tenths) in their composition of carbon, if it does not exceed 1%. In that case, if the carbon in the alloy is close 1%, then the figure at the beginning of their labeling is not put at all. On the content of other elements (in whole parts) indicate the numbers, which are marked with letters, denoting the corresponding alloying element.
Hardening and tempering of carbon tool steels
U GOST 1435 stipulated as the composition of carbon steels, and their main characteristics. The carbon content in such alloys (that can be determined by their brand) is from 0,65 to 1,35%. In order to obtain the optimal structure and the required hardness, these alloys are annealed before tool production begins. For tool steels with zaeftektoidny structure annealing of spheroidizing type is carried out.. The heat treatment carried out by this technology leads to the appearance of granular cementite. And to get grains of the required size allows the cooling rate, which can be easily adjusted.
Виробничий процес гарту сталі
After, how the tool will be made, tool steel is subjected to hardening and the next holiday. This makes it possible to obtain the material of the required hardness. Adjusting the hardness of the finished tool is also quite easy, this is achieved by selecting a certain temperature for the holiday operation.
So, for tools, exposed during operation to systematic shock loads, the hardness from is optimal 56 to 58 HRC, which receive, vacationing at the temperature 290 degrees Celsius. The strictest requirements are set for the hardness of the dies, engraving devices, files (62-64 units on the HRC scale). It is achieved by performing leave at a temperature of 150 to 200 degrees Celsius.
Hardening increases the hardness of carbon steels for that reason, that it is with its help it is possible to obtain the optimal structure of the alloy of iron and carbon. Options for such a structure:
- carbides with martensite;
- only martensite.
Інструментальна штампова сталь
Metal products, obtained by the method of deformation, can be processed in hot and cold condition. In accordance, and stamps, by means of which such details are processed, are cold and hot deformed. Naturally, that the production of different types of dies requires the use of different grades of tool steel.
So, for stamps cold-deformed type and small thickness (to 25 mm) U10 carbon steels are used, U11 and U12. The hardness of the alloys of these brands is in the range from 57 to 59 HRC units, they have sufficient viscosity, good level of resistance to deformations of plastic nature, ability to withstand wear during operation. For a larger tool (the thickness is greater 25 mm), which undergoes much greater loads during operation, use steels with high chromium content (X9, X, Х6ВФ).
Tool stamped steel in stock
Ware, regularly experience shock loads during their operation, must be of high viscosity (example, 4HS4 and 5HNM). To ensure compliance with this requirement, у виробництві використовують леговані сталі, the composition of which is enriched with special elements, and the carbon content is significantly reduced. in addition, special heat treatment of such tool steels is required.
Hot-deformed dies in the course of the operation are exposed not only to considerable mechanical, but also thermal loads. Naturally, as for tool steels for the production of these dies (example, 5HNM and 4HSMF) special requirements apply, such as:
- increased resistance to cracking under conditions of constant heating and cooling of the tool;
- high level of thermal conductivity and hardenability;
- resistance to scale formation.