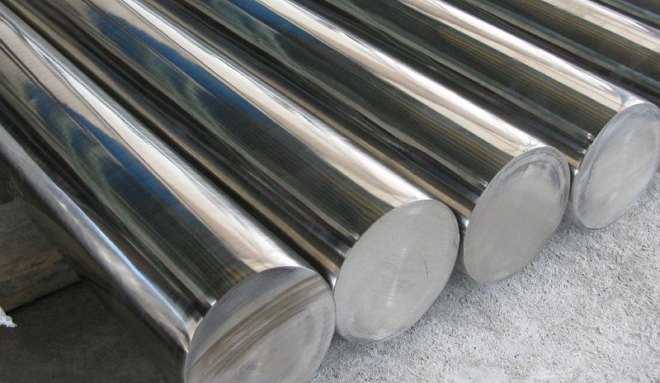
Alloy steel - classification, marking, properties, application
Alloy steel is steel, containing special alloying additives, which can significantly change a number of its mechanical and physical properties. In this article we will understand, which is a classification of alloy steels, as well as consider their labeling.
Round rolled alloy steel
Classification of alloy steels
According to the content in the composition of carbon steel is divided into:
- low carbon steels (to 0,25% carbon);
- medium carbon steels (to 0,25% to 0,65% carbon);
- high carbon steels (more 0,65% carbon).
Depending on the total number of alloying elements in their composition, which contains alloy steel, it can belong to one of three categories:
- low-alloy (not more 2,5%);
- medium alloyed (not more 10%);
- high alloy (from 10% to 50%).
Properties, which have alloy steels, determines their internal structure. Therefore, the classification of alloy steels involves the division into subsequent classes:
- pre-eutectoid - excessive ferrite is present;
- eutectoid - steel has a pearlite structure;
- eutectoid - secondary carbides are present in their structure;
- ledeburite - primary carbides are present in the structure.
According to their practical application, alloy structural steels can be: structural (are divided into machine-building or construction), instrumental, as well as steels with special properties.
Purpose of structural alloy steels:
- Machine-building - are used for the production of parts of various mechanisms, hull structures and the like. They differ, that in the vast majority of cases undergo heat treatment.
- Construction is most often used in the manufacture of welded metal structures and heat treated in rare cases.
The classification of mechanical alloy steels is as follows.
- Heat-resistant steels are actively used for the production of parts, designed to work in the energy sector (example, components of steam turbines), and also from them do especially responsible fastening. Chromium is used as an alloying additive, molybdenum, vanadium. Heat-resistant are medium-carbon, medium-alloyed, pearlitic steel.
- Improved (from the categories of medium carbon, low - and medium alloys) steel, in the production of which use hardening, used for the manufacture of heavily loaded parts, experiencing variable loads. They are sensitive to the concentration of voltage in the working part.
- Cemented (from low-carbon categories, low - and medium alloys) become, as the name implies, are subject to cementation and subsequent hardening. They are used to make all kinds of gears, shafts and other similar parts.
Dependence of the thickness of the cemented layer on the temperature and processing time
Classification of construction alloy steels involves their division into the following types:
- Mass - low-alloy steels in the form of pipes, shaped and sheet rolled products.
- Bridge construction - for road and railway bridges.
- Shipbuilding cold-resistant, normal and high strength - well withstands brittle fracture.
- Shipbuilding cold-resistant high strength - for welded structures, which should work in low temperatures.
- For hot water and steam - operating temperature is allowed to 600 degrees.
- Low-strength high-strength - used in aviation, sensitive to stress concentration.
- Increased strength with the use of carbonitrite reinforcement, creates a fine-grained steel structure.
- High strength with carbonitrite reinforcement.
- Reinforced by rolling at temperature 700-850 degrees.
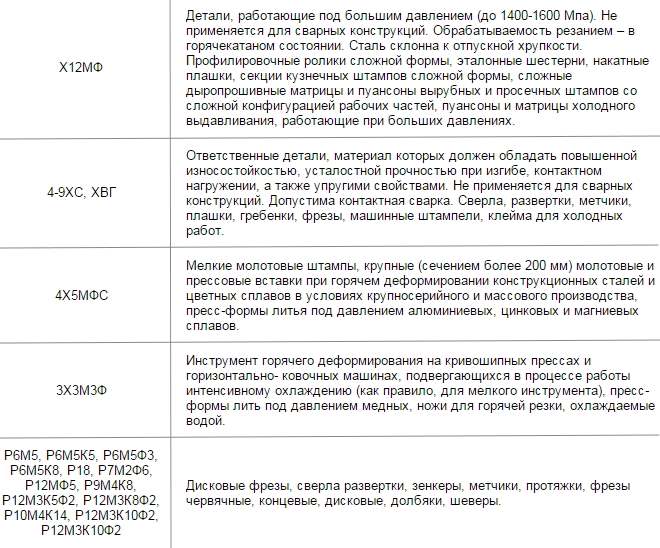
Application of tool alloy steels
Tool alloy steel is widely used in the manufacture of various tools. But in addition to the clear advantage over carbon steel in terms of hardness and strength, alloy steel also has a weak side - higher brittleness. Therefore for the tool, which is actively exposed to shock loads, such steels are not always suitable. However, in the production of a huge list of cutters, shock-die, measuring and other tools are tool alloy steels remain indispensable.
Separately, high-speed steel can be noted, distinctive features of which are very high hardness and redness resistance to temperature 600 degrees. This steel is able to withstand heat at high cutting speeds, that allows to increase speed of work of the metalworking equipment and to prolong its service life.
A separate category includes alloy structural steels, endowed with special properties: stainless, with improved electrical and magnetic characteristics. From that, what elements, as well as in what quantities they are mainly contained, they may be chromic, nickel, chromonickelmolybdenum. They are also divided into three, four - and more component in the number of alloying additives contained in them.
Alloying elements and their effect on the properties of steels
Marking of alloy steels indicates that, what additives it contains, as well as their quantitative value. But it is also important to know that, what is the effect on the properties of the metal has each of these elements separately.
Chromium
The addition of chromium increases corrosion resistance, increases strength and hardness, is the main component in the creation of stainless steel.
Nickel
Adding nickel increases ductility, steel viscosity and corrosion resistance.
Titanium
Titanium reduces the grain size of the internal structure, increasing strength and density, improves machinability and corrosion resistance.
Vanadium
The presence of vanadium reduces the granularity of the internal structure, which increases the yield strength and tensile strength.
Molybdenum
The addition of molybdenum makes it possible to improve calcination, increase corrosion resistance and reduce brittleness.
Tungsten
Tungsten increases hardness, prevents grains from growing when heated and reduces brittleness when tempered.
Silicon
When content to 1-15% silicon increases strength, maintaining viscosity. As the percentage of silicon content increases, the magnetic permeability and electrical resistance increase. This element also increases the elasticity, corrosion resistance and oxidation resistance, but also increases fragility.
Cobalt
The introduction of cobalt increases the strength and heat resistance.
Aluminum
The addition of aluminum helps to increase scale resistance.
The purpose table of some types of steel
Impurities and their effect on the properties of steels should be mentioned separately. Any steel always contains technological impurities, since it is extremely difficult to completely remove them from the warehouse. Such impurities include carbon, sulfur, manganese, silicon, phosphorus, nitrogen and oxygen.
Carbon
Has a very significant effect on the properties of steel. If it is contained before 1,2%, carbon helps to increase hardness, strength, yield strength of the metal. Exceeding this value contributes to this, which begins to deteriorate significantly not only strength, but also plasticity.
Manganese
If the amount of manganese does not exceed 0,8%, then it is considered a technological impurity. It is designed to increase the degree of deoxidation, and to resist the negative effects of sulfur on steel.
Sulfur
When the sulfur content is higher 0,65% the mechanical properties of steel are significantly reduced, we are talking about reducing the level of plasticity, corrosion resistance, toughness. Also, high sulfur content adversely affects the weldability of steel.
Phosphorus
Even a slight excess of phosphorus above the required level threatens to increase fragility and fluidity, as well as reducing the viscosity and ductility of steel.
Nitrogen and oxygen
When exceeding certain quantitative values in the composition of the steel inclusions of these gases increase the fragility, and reduce its endurance and viscosity.
Hydrogen
Too much hydrogen in steel leads to an increase in its brittleness.
Marking of alloy steels
A large variety of steels belongs to the category of alloys, which necessitated the systematization of their alphanumeric notation. Requirements for their labeling are determined by GOST 4543-71, according to which alloys, endowed with special properties, are marked with markings, where the letter is in the first position. From this letter it is possible to determine, that steel by its properties belongs to a certain group.
Example of decoding alloy steel markings
So, if the marking of alloy steels begins with the letters "F", "X" or "E" - before us an alloy of stainless steel, chromium or magnetic group. Steel, which belongs to the stainless chromium-nickel group, is denoted by the letter "I" in its marking. Alloys, belonging to the category of ball bearings and high-speed tool, are denoted by the letters "W" and "P".
Steel, relating to doped, may belong to the category of high quality, as well as especially high quality. In such cases, the letter "A" or "W" is placed at the end of the stamp, respectively. Steel, which have the usual quality, they do not have such designations in their marking. Alloys also have a special designation, which are obtained by rolling method. In this case, the letter "H" is present in the label. (hardened hire) or "THAT" (heat-treated rolled products).
The exact chemical composition of any alloy steel can be found in regulations and reference literature, but to obtain such information allows the ability to understand its labeling. The first number makes it clear, how much carbon (in hundredths of a percent) contains alloy steel. After this number in the stamp the letter designations of alloying elements are listed, which are contained in addition.
Designation of alloying elements in steel marking
Each such letter is followed by the quantitative content of the element. This content is expressed in whole fractions. After the letter, denoting an element, may not be a single digit. It means that, that its content in steel does not exceed 1,5%. State standard 4543-71 regulates the designation of alloying additives, which are a part of alloy steel: A - Nitrogen, B - Niobium, B - Tungsten, G - Manganese, D - Copper, K - Cobalt, M - Molybdenum, H - Nickel, P - Phosphorus, R - Bor, C - Silicon, T - Titanium, C - Zirconium, F - Vanadium, H - Chrome, Yu - Aluminum.
The use of alloy steels
Today it is difficult to find a sphere of life and activity, in which alloy steel was not used. Almost any tool is made of tool and structural steels: cutters, cutters, prints, measuring devices, gears, springs, pendants, stretch marks and more. Stainless alloy steels are actively used in everyday life, dishes are made of them, cases and other elements of many types of household appliances.
Alloy steels due to their high cost are used only for the production of the most responsible structures and parts, where products made of other metals simply will not be able to perform the tasks assigned to them.