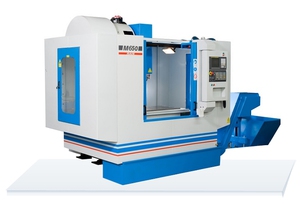
Metalworking: features of the CNC machine, its types, basic elements of equipment
By means of the machine there is a technological process, which is provided on it. The control system is one or more devices, who carry out such action. On machines with numerical program control (ЧПУ) a program is provided for metalworking, which is mounted on electronic media, as a data set. Today, the management of production processes in industry is with the help of programmable logic controllers.
Features of CNC machines
CNC milling machines for metalworking help to process spatial and flat surfaces, having a complex configuration, cams, mold, stamps, at the same time end and face mills are used. On such units it is possible to carry out drilling and razvortochnye works thanks to the special tool, which is mounted in the corresponding working heads.
The design of the CNC machine for metalworking is almost no different from conventional milling units. But installing numerical software control on hardware increases its performance several times, and also increases reliability, accuracy when performing operations with high cutting speed, as well as clear positioning of cutters and other cutting tools.
See
Classification of CNC machines is based on four criteria:
- Automatic or manual feed of working tools for cutting.
- Coordinate movements of the headstock of the device or its working surface.
- The spindle assembly can be located vertically or horizontally.
- Machines can be single-tool or multi-tool.
The division of equipment into different categories depends on its layout, namely: universal, longitudinal milling, cantilever milling, vertical milling. The latter type must be provided with a cross-shaped table.
For the implementation of metalworking CNC systems can be:
- Disconnected. Thanks to the stepper motor there is a clear dosing of process of movement of workers of knots of the device, which eliminates the need to use feedback sensors.
- Closed. Sensors are mounted in the units, which control the operation of the processing operation, as well as the drive, moving the working nodes according to the scheme.
The driving force in modern CNC machines for metalworking are DC electric motors and asynchronous motors. With direct drive, special gear mechanism or belt feed, they direct rotation to the spindle.
The horizontal type of machines is used for processing hull and large products. However, vertical devices are more often used in production, as recognized as more efficient and universal.
The main components of the equipment
The frame is made welded or cast. When you want to get a structure of complex shape it is welded. The cast bed is made in all other cases, as it is characterized by rigidity and high damping potential.
Sliding guides are a must for a versatile machine. Their work is based on sliding friction, which reduces the accuracy of their interpolation and reduces the speed of movement of the workers of the elements. However, they are characterized by increased rigidity.
Excellent accuracy of movements is guaranteed by linear guides, after all, their work is based on the friction of rolling, however, they have a low stiffness.
The spindle of the CNC machine tool for metalworking is divided into two types:
- Electric motor with rotor, which is required for the installation of cutters and any other cutting tools.
- Mechanism, which is connected to the drive by means of a coupling or a belt feed.
The first type is installed on the equipment, which works with molds and intricate stamps, because it is able to work at speeds up to 100 000 rpm. Not more 15 000 revolutions can develop a second type of spindle, its price is much less, therefore, it is widespread. The spindle mechanism on modern CNC machines for metalworking may have hydrostatic, aerodynamic and conventional rolling bearings.
Other important components of CNC units are:
- Electric motor.
- CNC system.
- Shop for working devices.
Processing of blanks
Technology and features
Software control of the milling machine, if configured correctly, allows you to move cutters and other tools on any trajectory in the area of the machine. Thanks to it it is possible to process a product from different parties for its one-time fixing. Most modern CNC machines are capable of performing these types of work:
- Countersinking, deployment, drilling holes.
- Milling curved, cylindrical surfaces and different planes.
- Turning of external surfaces of a cylindrical form.
Machines with three coordinate axes are capable of such work. If the equipment is equipped with the fourth and fifth axes, then it is possible to carry out more difficult processing of metal preparations. Example, perform work on five-coordinate devices, associated with cutting shaped surfaces, and this is done efficiently and quickly.
Equipment with five coordinates is a machine, which makes it possible to rotate the part around a given value of the axis, which is in addition to the main movement of the tool in relation to the workpiece.
Usually the fifth coordinate is replaced by the angle of the axis spindle. If it is changed during operation, resorting to the CNC management program, then for one fixing of a detail on the unit processing of small fillets on radius can begin (transitional surfaces). This operation is performed using conical end mills, having a characteristic rounding in the form of a sphere.
A three-coordinate unit can be easily converted to a four-coordinate or five-coordinate one.. All you have to do is add a turntable to the table. However, this will reduce the working area of the machine.
so, modern CNC machines for metalworking have a wide range of functionalities, they perform many operations efficiently and quickly. Thanks to them time expenses for technological process are reduced, which affects the level of productivity.