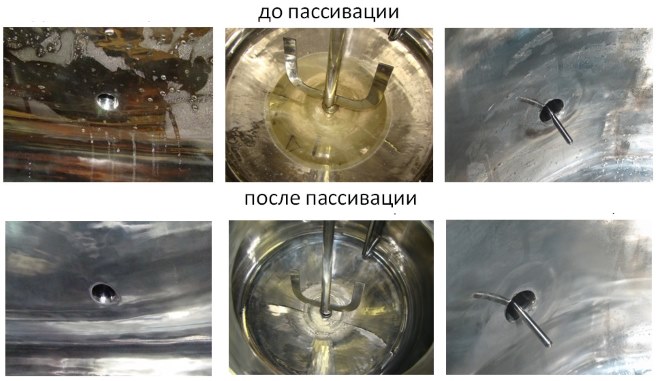
Passivation (passivation) metals: technology and methods
Though, that stainless steel is highly resistant to corrosion, additional protection, which allows you to get such a technological operation, as passivation, it is desirable for her. In some cases, when even products are at high risk of corrosion, made of stainless steel, the need for such a procedure is beyond doubt.
Examples of stainless surfaces, subject to corrosion, and the results of the passivation
What is the reason ??high corrosion resistance of stainless steels
The essence of this phenomenon, as corrosion, is, that the surface of the metal under the influence of negative external factors and the environment begins to collapse. What is characteristic, corrosion due to constant oxidation affects the metal layer by layer, gradually destroying the internal structure of steel. In many cases, it no longer makes sense to locate the affected areas of the internal structure of the metal, therefore, steel products have to be replaced with new ones.
Passivation (or passivation) as technology, that allows to provide reliable protection of steel against corrosion, is the basis for creating such a unique metal, which is stainless steel. In the chemical composition of the vast majority of steels, belonging to the stainless category, may contain different elements:
- nickel;
- molybdenum;
- cobalt;
- niobium;
- manganese.
However, the main alloying element of such steels, the number of which in their composition may vary within 12-20%, is chrome. The addition of various alloying elements to the composition of stainless steels allows them to provide the necessary physical and chemical characteristics, but it is chromium that is responsible for the corrosion resistance of the steel alloy.
Influence of chromium on the properties of stainless steel
Stainless steel alloys, which contains 12% chromium, show high corrosion resistance only when interacting with ambient air. If the amount of chromium in the chemical composition of stainless steel increase to 17%, then its products will be able to easily interact with nitric acid, that without losing its performance characteristics.
To make the metal resistant to even more aggressive environments, which include salt, sulfuric and other acids, it not only increases the quantitative content of chromium, but also add to its composition such elements, like copper, molybdenum, nickel and others. In other words , perform passivation of the metal, that is, increase its passivity to corrosion processes.
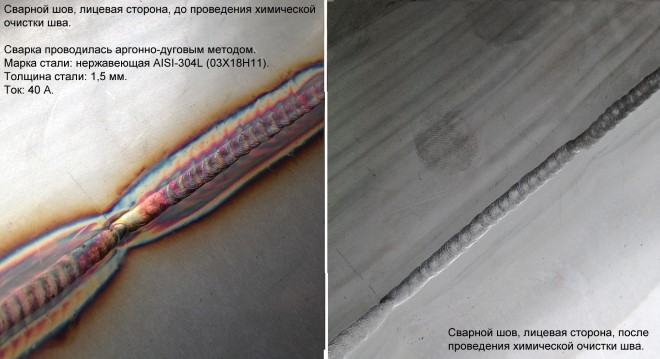
In the process of passivation of the weld zone, a strong film is formed
Passivation, in which the chemical composition of stainless steel add the appropriate alloying elements, - this is not the only condition for high corrosion resistance of the metal. That the protective properties of stainless steel remain at a high level, oxide film on its surface, consisting mainly of chromium oxide, must be intact, have a homogeneous chemical composition and thickness.
Causes of corrosion
Though, that the chemical composition of stainless steel must contain a passivator, significantly increase its corrosion resistance, its surface and internal structure may corrode.
The main reason, on which stainless steel begins to break down, there is insufficient or uneven content in its chemical composition of chromium. Contact with metal can also cause corrosion, which is much less resistant to oxidation. Stainless steel products are often subject to destruction, which were interconnected by welding technology.
Corrosion of heated towel rail pipes, resulting from the dishonest execution of the weld by the manufacturer
What is characteristic, even if the stainless steel is of very high quality, after welding it may be covered with a layer of rust. To avoid such negative phenomena, welds, which are used to connect stainless steel products, must be carefully cleaned and polished. This procedure allows you to remove from the surface of the weld and the stainless steel products remnants of less corrosion-resistant metal, which was used to perform welding work.
Very often on the surface of stainless steel particles less corrosion-resistant metal fall in those cases, when its processing is performed in the immediate vicinity of steel products. So, if sawed nearby, grind or perform other types of processing of ordinary metal, then its particles, getting on stainless steel, will inevitably become sources of corrosion. They can also appear on stainless steel in that case, if you decide to perform its tool processing, which previously interacted with ordinary metal. That's why tools, especially related to the cutting type, it is desirable to use for processing only the same type of materials.
Corrosion of stainless steel hoods, which occurred as a result of cleaning the product with an iron brush
However, Of course, the most critical place on the surface of stainless steel products in terms of the occurrence and development of corrosion processes is the weld. That is why not only thorough cleaning is important, grinding and polishing of the formed welded joint, but also its passivation, for which various acid solutions are used.
Passivation (chemical passivation), usually, performed using the solution, which is based on nitric acid. Treatment of this solution carefully prepared area of stainless steel allows you to form an oxide film, characterized by high passivity to corrosion processes.
Stainless steel welding, after which chemical passivation is performed, is carried out by means of a metal brush and the grinder. With, as mentioned above, it is important to monitor this, so that the tools used in passivation do not react with ordinary metal, particles of which can become a source of corrosion processes.
To check, is not present on the surface of stainless steel inclusions of ordinary metal, you can use two ways.
Treatment with an aqueous solution of nitric acid and potassium ferrocyanide
Places on the surface of the product, on which there are inclusions of free iron, after such treatment will immediately turn blue. It should be noted, that this method of verification is used mainly in production laboratories.
Wetting with ordinary water
The product is kept in this state for several hours. If the stainless steel has the inclusion of free iron, then areas with such inclusions will be covered with rust.
Types of corrosion
Though, that the corrosion process leads to almost the same consequences, reasons, it is called, may be different. The most common cause of corrosion of stainless steel products, used in domestic conditions, there are applications for their cleaning agents, containing a significant amount of chlorine in its chemical composition. Such funds actively contribute to the destruction of the oxide film on the metal, which leads to the development of a corrosion process on its entire surface (ie general corrosion).
Slit corrosion of stainless steel occurs in those cases, when parts of such metal are in contact with each other for a long time. Corrosion of this type, which is typical, often begins to develop in places of attachment. There are also spot corrosion, which is often called ulcerative. It occurs in those cases, when the oxide film on stainless steel is mechanically damaged.
Underwater corrosion of stainless steel is more common at the joints
If the stainless steel is in contact with dissimilar metal in a conductive medium, corrosion begins to develop, which is called galvanic. Stainless steel products are most prone to this process, operated in sea water and in contact with metals, characterized by a lower degree of doping.
Intergranular corrosion is a very common phenomenon, which occurs in those cases, when the stainless steel product has been significantly overheated. At strong heating (over 500 °) chromium and iron carbides are formed at the boundaries of the stainless steel crystal lattice, which caused a decrease in the strength of the metal.
Corrosion of stainless steel can occur due to the use of chlorine-containing cleaning compositions
There are also erosive corrosion, which arises, if the stainless steel is constantly under the influence of the abrasive environment. Constantly affecting the metal surface, particles of such a medium destroy the protective oxide film, which does not have time to recover.
Passivation of stainless steel
Provide such operating conditions for stainless steel products, so that they do not come into contact with other metals and aggressive media, and were not subjected to mechanical damage, practically impossible. That is why the above-mentioned technological operation is required - passivation. Additional degree of protection, which provides passivation (passivation), often trying to provide:
- stainless steel pipe designs;
- fasteners;
- body elements of structures and mechanisms, operated in seawater.
Meanwhile, passivation is not always appropriate even for products of this purpose.
Passivation of a stainless steel welding seam
Passivation, although it is a method of processing stainless steel, able to provide additional protection against corrosion, in many cases it is impractical and may even impair the protective properties of steel. Therefore, before performing passivation, conditions should be analyzed, in which the product will be operated, to unambiguously decide, whether its surface needs additional protection.
Passivation, if the decision to implement it is made, must ensure a solid and uniform thickness of the protective layer, which is achieved by strict adherence to the technological process. Usually, passivation is performed in those cases, when external protection is required, rather than the inner surface of the stainless steel product.
The essence of this process, as passivation, is, that the surface of the stainless steel product is treated with a special solution, which is based on nitrogen, and in some cases citric acid. Sometimes this solution can be supplemented with a small amount (2-6%) sodium dichromate. The chemical composition of this solution, as well as the following parameters, as heating temperature and holding time, depend on the brand of stainless steel being processed.