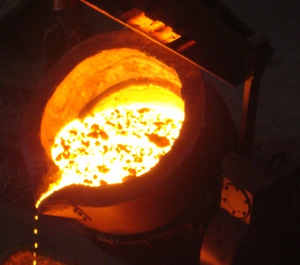
Melting of cast iron: optimal temperature, material classification, comparison with steel
Iron alloy is called cast iron, which contains more 2% carbon. In addition to these components, constant substances are present in the mixture, such as sulfur, silicon, phosphorus, manganese and alloying additives. The material is divided into different types depending on the alloy, which is determined by the structure of the fracture. Cast iron has up to a hundred different brands, among them stands out foundry, it is different from others:texture, purpose and technology of receipt.
Classification of material
This material is more fragile, than steel. It is able to collapse without noticeable deformations. The carbon in the alloy has the form of graphite and cementite or each substance is presented separately. Varieties of cast iron appear due to their shape and quantity:
- White. All carbon is in the form of cementite. This color of the material is visible at the break. It can be described as fragile, but solid. It is processed, mainly, to obtain forging varieties.
- Gray. Carbon in the form of a plastic form of graphite. Characterized as soft, well processed, at which low melting temperatures are used.
- Malleable. This type is called conditionally, as the material is not susceptible to forging. This type is obtained by prolonged firing of white, then graphite is formed. The properties of the material are negatively affected by overheating 900 degrees, as well as the cooling rate of graphite. As a result, the process of welding and processing is complicated.
- High strength. It contains spherical graphite, which is formed by crystallization.
The differences were from cast iron
The difference in materials is expressed as follows:
Cast iron is less hard and durable, like steel.
- Steel is heavier and has a higher melting point.
- Since they have become lower in carbon, it is better processed (forging, cutting, weld, rolling). For this reason, cast iron products are made by casting.
- Porous cast iron products (through Lithuania), therefore their thermal conductivity is lower.
- Artistic steel products have a shine and shine, they are made of cast iron and black and matte.
- Cast iron is the primary product of ferrous metallurgy, and steel - the final.
- Steel, usually, subjected to the hardening procedure.
- Cast iron products are formed during casting, and steel products are forged and welded.
Cast iron: melting point
Pros of the material
This material has good casting properties, has a good fluidity, lower melting point compared to steel and malleable cast iron. These properties are taken into account in the manufacture of the form.
Gaseous flux is most often used for welding brass material. Also use cast iron rods with copper coating, which improve the wettability of the edging surfacing metal. Eutectic cast iron rods are used, its melting point is in the range 1050 — 1200 degrees. Welding also occurs due to the flux, which are used in the form of a paste. If there are no special cast iron rods or brass L-62, then cracks in the parts of this material can be welded with wire, which is made of electrolytic red copper.
Much higher than the melting point of overheating of cast iron, which leads to, that these suspended particles dissolve, perhaps, not fully, and this complicates the formation of graphite. In some cases, it can occur when adding various substances to cast iron, due to which there will be additional centers of crystallization of graphite.
Cast iron has the best casting properties, if we compare it with steel. Convenience in work, as well as good fluidity and filling of the mold is provided by a lower melting point and the final crystallization process at a constant temperature.
The above advantages of cast iron make the material a valuable structural material, which is widely used in machine parts, when they are not subject to significant tensile and shock loads.
Melting point of semi-synthetic material
Semi-synthetic cast iron is melted by melting the charge, while the temperature range varies in the interval 1400-1450 degrees. After melting the charge, the cast iron is stored in the crucible of the furnace with slight overheating, not exceeding the melting point by one hundred degrees. What you need to do to create a slag cover? When the charge gradually begins to melt, glass mirror or calcined quartz sand should be applied to the metal mirror.
Types of welding
Gas welding should be carried out by melting by flame parts of the connecting elements and the rod of filler metal. This welding is used for that, to connect metal parts, non-metallic elements and alloys, which have different melting points, the thickness should not exceed 30 mm. You do not need to resort to electricity to arrange it.
Electric arc welding is widely used. Due to the electric arc the metal is melted, which combines different elements, interacts with the electrode metal, forming a strong seam. That the seam did not oxidize, the electrode is covered with a protective substance, example, for this purpose flux or inert gases are used (argon, helium). Electric arc welding using various methods of action (manually, on semi-automatic and automatic machines) make joints of cast iron parts, structural steels, copper, aluminum and other alloys.
From carbon, which is contained in the material, depends on the melting point. The more of it, the lower the temperature, and the fluidity when heated is higher. From this we can conclude, that the material is liquid, fragile, non-plastic and difficult to process. Its specific weight is equal to 6,9 G / cm3. The melting point is in the range 1150-1250 degrees.