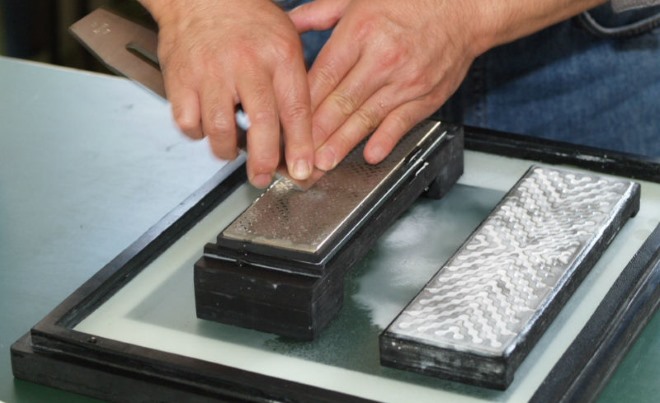
Grinding - finishing the metal surface: grinders, machines
The most efficient technological operation, that allows to bring a surface of details from metal to an ideal condition, there is grinding. Details, the surface of which was subjected to such a procedure, may form airtight or tight connections. The need to form such connections and, in accordance, in technological operation, performed with special tools and materials, is in many areas.
Finishing the blade of the plane on the grinding bars
the essence of technology
Grinding, thanks to which it is possible to receive surfaces with necessary degree of roughness and with the set deviations, involves removing a thin layer of metal from the workpiece, for which, in contrast to the finishing operation of the scraper, not only tools are used, but also fine abrasive powders or pastes. Abrasive material, by which such processing is performed, can be applied as on a surface of a detail, and on a special device, which is called grinding.
schemes of proof
Grinding, performed at a slow speed and with constantly changing the direction of movement, allows not only to reduce the surface roughness to the desired value, but also significantly improve its physical and mechanical characteristics.
Grinding, which is often called proof, can be performed in different ways. So, details of complex configuration, manufactured in single copies, processed completely by hand, and for grinding products, available in small series, use a semi-mechanical method. At the same time giving of a detail in a processing zone is carried out manually, and grinding itself is performed using mechanical devices. In the production of parts in large series and en masse can not do without such a device, as a lapping machine, by means of which and carry out finishing operations.
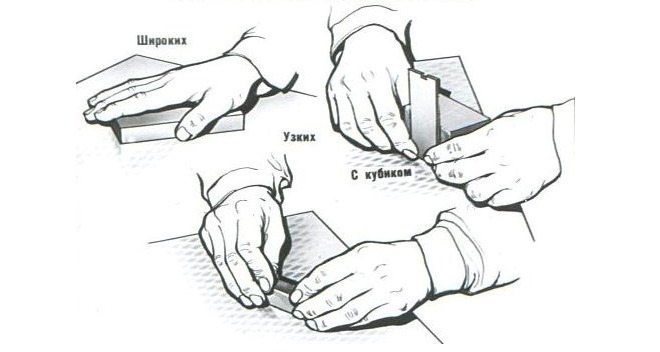
Position of hands when grinding metal surfaces
Special devices and materials
As mentioned above, to perform grinding or finishing, special tool required, which is called grinding. By the shape of the work surface, such devices are divided into the following types:
- flat grinding tool;
- with an inner surface of cylindrical type;
- with an outer cylindrical surface;
- conical tool.
Pneumatic lapping machine for finishing valves
Choosing a material for making a lapping tool, pay attention to that, that its hardness was much lower, than the hardness of the material of the workpiece. This requirement is due to the topic, that abrasive powder or paste, using which perform grinding, could be held by the material of the tool. So, the most common raw material for the manufacture of such devices is:
- gray cast iron;
- copper;
- lead;
- mild steel;
- different species of wood;
- other metals and non-metallic materials.
Special grinders for optical sight sleeves
To perform preliminary and finishing grinding operations, the tool is used as a different design, and made of different materials. Example, to perform previous operations, when using abrasive material of a larger fraction, a tool made of softer materials is used. On the working surface it is pre-cut grooves to hold the abrasive, the depth of which is 1-2 mm. Finishing of products, performed with a fine abrasive, carried out by the device, the working surface of which is absolutely smooth. The material of the tool for finishing operations, mainly cast iron. With the help of grinding tools, which are made of lead and wood, the surfaces of the workpieces are glossy.
Set for manual grinding, consisting of cast iron grinders and diamond paste of different grain sizes
Abrasive powder is the main material, which ensures the efficiency and quality of grinding. Such powders, depending on the material of manufacture, divided into solid (the hardness of the material is higher, than in hardened steel) and soft (their hardness is lower, than in hardened steel). Corundum is used to make powders of the first type, carbocorundum and emery, and the other chromium oxide, Viennese lime, crocus and others. According to the degree of granularity, abrasive powders are also divided into several categories. You can distinguish powders and pastes of different categories from each other even by their color. So, paste, based on coarse powder, have a light green color, medium grain - dark green, paste with fine powder - greenish-black.
The most famous variety of pastes of the latter type, with which to perform finishing lapping operations, there is a GOI paste.
Many homemakers, engaged in metalwork, independently make powders and pastes for grinding. This is quite easy to do: for this purpose it is necessary to grind carefully pieces of an emery wheel in a massive mortar, and then sift the resulting powder through a sieve with very small cells.
GOI paste is used for finishing metal, glass and plastic surfaces
On the efficiency and quality of grinding, in addition to the equipment and abrasive material used, the applied lubricant has a serious effect. Various substances can be used as such material:
- skipidar;
- mineral oil;
- gas;
- animal fats;
- alcohol or aviation kerosene.
The last two substances are used in those cases, when the quality of grinding performance is subject to increased requirements.
Common grinding defects and ways to eliminate them
Tools and accessories
The most common device for finishing operations are grinding plates, which, as mentioned above, can be made ??from different materials. The choice of type and material of such a plate, which is a fairly versatile device, affect as features of the processed details, and the requirements for the quality of the ground surface. Among all types of plates the products became the most widespread, made of cast iron brands, whose hardness (on HB) is in the interval 190-230 units.
Industrial lapping table
The design and dimensions of the plate or lapping tool of another type are affected as design features of the processed products, and the type of processing: rough or finished. Slabs are used as a device for grinding to treat flat surfaces. With, as mentioned above, on the surface of the plates, used to perform roughing operations, special grooves are applied, which may have a spiral configuration. Such grooves not only keep abrasive material in the grinding zone, but also remove waste from it.
Naturally, what to do with a grinding plate of cylindrical surfaces, holes and parts with complex configuration, is not possible. Therefore, devices are made for such purposes, the shape of which is optimal for processing parts of a certain configuration. So, these can be round grinding tools, cylindrical, ring, conical, disk configuration, etc.. In particular, grinding of openings is carried out by the device, which is made in the form of bushings, fixed on special mandrels.
Tool, by means of which grinding operations are performed, also divided into unregulated and regulated. The second type of device is more versatile, its design, consisting of a split working part, cone and sliding device, provides the ability to change its diameter.
For processing of details of a cylindrical form, it is not necessary to use a specialized lathe, universal turning or drilling equipment is quite suitable for this purpose. The workpiece in such cases can be fixed in the centers or the cartridge of the equipment, depending on, what part of its surface must be ground.
Use of the manual grinding and grinding machine at repair of flat-seat fittings
Machines, which were originally designed for grinding, are divided into general purpose equipment and specialized models. On general purpose machines, which can be equipped with one or two lapping tools, mainly machined parts with flat and cylindrical surfaces. Smaller parts when processed on such machines in the free state are placed in a special separator, where they undergo grinding, located between two rotating lapping discs. Large parts are fixed on the machine with a special device and machined with a single abrasive disk.
Lapmaster flat grinding machine, designed for processing various materials, including metals and ceramics
Specialized machines are more complex in design and less versatile, the device of which is specially designed to grind parts of a certain configuration: valve seats, camshafts, crankshaft necks, gears, etc..
Such machines, having high productivity and providing high quality of grinding, used in large-scale and mass production, therefore, innovative technical solutions are often implemented in their designs: self-centering centrifugal cartridges, devices for automatic adjustment of pressing force, etc..