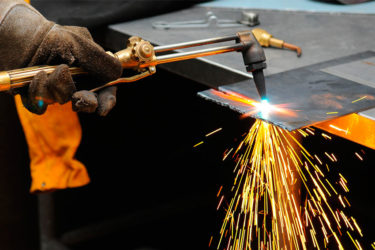
Cutting metal with oxygen propane cutter: pros and cons, technology, specifics
Gas cutting seems to be a simpler process, than gas welding, and therefore even a person can cope with it, who does not have special skills. For this reason, almost any of us can learn to work with a gas cutter. The main thing here is to learn the essence of gas cutting technology. In modern conditions, propane cutters are increasingly used. Working with them requires the use of both propane and oxygen, because the combination of such substances provides the maximum combustion temperature.
Advantages and disadvantages
Propane metal cutting has a number of advantages, among which we can highlight the following:
- Gas cutting is in demand in the situation, when there is a need to cut metal of considerable thickness or to create products according to templates, which involve the manufacture of curved cutting, which cannot be done with the help of a Bulgarian. Also do not do without a gas cutter and then, as is the task of cutting a disk of thick metal or making blind holes on 20-50 mm.
- The gas cutter is a very convenient tool and has a low weight. To all home builders, who had experience in handling gasoline models, known inconveniences, associated with heavy weight, size and noise. in addition, that significant inconvenience is created by vibration, the operator is forced to provide severe pressure during operation. Gas models are a more attractive alternative due to the lack of all the above disadvantages.
- The use of gas cutting metal allows in 2 times speed up work, which cannot be done with the device, equipped with a gasoline engine.
- Among most gases, including gasoline, propane is released at a lower price. For this reason, it is better suited to perform a significant amount of work, example, if there was a problem of cutting steel into scrap metal.
- When using propane cutting it is possible to create a narrower cutting edge, than when working with acetylene cutters. This method allows you to create a cleaner slice, than that, which can be done with gasoline burners or Bulgarian.
Among the disadvantages, which are possessed by propane cutters, only one should be singled out: they can only be used for a limited range of metals. They are suitable for cutting extremely low- and medium carbon steels, and besides, and malleable cast iron.
features of use
Such tools are not suitable for cutting high carbon steels for that reason, that they have a fairly high melting point, which is almost indistinguishable from the flame temperature. This leads to that, that instead of emitting scale, having the form of a pillar of sparks, on the back of the sheet, it is mixed with molten metal along the edges of the cut. As a result, oxygen cannot reach the thickness of the metal, due to which he fails to burn the material.
Difficulties in cutting cast iron are the shape of the grains, as well as graphite between them. Truth, this does not apply to malleable cast iron. It is impossible to solve the problem, if you have to deal with aluminum, copper and their alloys.
It is important to dwell on the next point: category of low-carbon steels are brands from 08 to 20D, medium carbon - brands from 30 up to 50G2. A characteristic feature of carbon steel grades is the presence of the letter B in front of their name.
Necessary equipment
As with any other job, even before the start of cutting the metal with gas should prepare the necessary equipment:
- Propane and oxygen cylinder - 1 PC .;
- High pressure hoses;
- cutter;
- Mundshtuk, which must have certain dimensions.
A gearbox must be present on all cylinders, with which you can adjust the gas supply. Keep that in mind, that the propane cylinder has a reverse thread, because of what to turn on it the additional reducer will not turn out.
In general, gas equipment for cutting metal has a similar device, regardless of the manufacturer. There are three valves in the design:
- the first provides propane;
- the second valve allows you to change the oxygen supply;
- the latter is the cutting oxygen valve.
Blue markings are usually used to indicate oxygen valves, and for valves, providing supply of propane - red or yellow.
Metal cutting provides a jet of hot flame, affecting the metal, which is created using a cutter. When it is turned on, in a special chamber of the mixer there is a mixing of propane and oxygen, which leads to the appearance of a combustible mixture.
With the help of a propane cutter you can cut metal, whose thickness does not exceed 300 mm. The detailed installation is completed with elements, which are mostly variable. For this reason, in the event of failure of a part of the operator is not difficult to perform repairs directly at the workplace.
The choice of mouthpiece should be approached with special care. The key parameter, to which you need to pay attention - the thickness of the metal. If you have to deal with the subject, providing elements of different thickness, ranging from 6 to 300 mm, then you have to prepare the mouthpieces, having internal numbers from 1 to 2, and external - from 1 to 5.
Preparation for work
The appliance must be inspected before starting gas cutting, make sure, that the propane cutter is in working order. Next you need to perform the following operations:
Preparation of the device for cutting begins with connection of hoses to it. Even before joining the sleeve, it is purged with gas - this will remove debris and dirt from it.
- The oxygen hose must be connected to the right-hand fitting, a nipple and a nut are used for this purpose. As for the hose, through which propane will arrive, then it is attached to the fitting with the left thread. Be sure to find out before connecting the gas hose, whether there is suction in the channels of the cutter. This problem can be solved by connecting an oxygen hose to the oxygen fitting, you need to make sure, the gas fitting will remain free.
- Next you need to set the oxygen supply level to 5 atmospheres, then you need to open the valves, which regulate the flow of gas and oxygen. Touch the free fitting with your finger to find out if there is an air intake. In its absence, you will have to clean the injector and blow the channels of the cutter.
- Then you need to make sure, whether the detachable connections are tight. If a leak can be detected, it is removed by tightening the nuts or replacing the seals. You should also make sure of that, whether gas tight fastenings are sufficiently tight, manometers are in working order or in good condition.
Let's get to work
First you need to move the oxygen reducer in position, appropriate 5 atmospheres, gas - 0,5. You also need to make sure, that each valve is in the closed position.
Then you need to take a propane cutter and slightly open the propane, and then set it on fire. The cutter nozzle should be positioned as follows, so that it rests on the metal, then you need to slowly open the regulating oxygen. Next, adjust these valves one by one, this will provide the required flame supply force. During this setting, you need to open the gas sequentially, oxygen, gas, oxygen.
When choosing the strength of the flame, you need to focus on the thickness of the metal. As the thickness of the sheet increases, the strength of the flame will increase, which will increase the consumption of oxygen and propane. After adjusting the flame strength, you can start cutting the metal. The nozzle must be held in relation to the edge of the metal in this way, so that it is removed from the cut object at a distance 5 mm, namely, it must be at an angle 90 degrees. In some cases, you may need to cut a sheet or product in the center. In this case, the starting point is chosen that place, from which the incision will go.
The essence of the procedure is to heat the upper edge to temperature 1000-1300 degrees Celsius. The exact temperature is determined taking into account the metal. In practice, such work will look like, when the surface seems to "get wet". It will take no more to warm up 10 seconds. Waiting for the metal to ignite, you need to open the cutting oxygen valve, after which a powerful narrow-minded will begin to arrive ??jet.
features of cutting
When opening the propane cutter valve, do not rush. In this case, the ignition of oxygen will occur naturally as a result of interaction with the heated metal. Acting in this way, you eliminate the risk of backfire, during which cotton can be observed. You need to slowly conduct the oxygen jet strictly parallel to the specified line. Here it is important not to be mistaken with the angle of inclination.
At first it is maintained by size 90 degrees, then you need to create a slight deviation on 5-6 degrees in the direction, which is opposite to the movement of the cutter. If you have to deal with metal, whose thickness is more than 95 mm, it is allowed to increase the deviation to 70 degrees. Once the slot in the metal reaches 15-20 mm, the angle of inclination begins to increase to 20-30 degrees.
Nuances of cutting metal
It is important to maintain the required speed when cutting metal. Its selection is carried out visually, for which the speed of sparks is estimated.
If the speed is optimal, then the flow of sparks will fly at an angle of about 88-90 degrees relative to the surface, cutting. In the situation, when the flow of sparks tends in the direction, which is opposite to the movement of the cutter, it is possible to draw a conclusion, that is installed ??cutting speed too low. In some cases, the flow of sparks takes off at a smaller angle 85 degrees. This is a hint, that the current cutting speed is too high.
It is important to take this parameter into account when cutting with gas, as the thickness of the metal. If it matters more 60 mm, it is desirable to place the sheets at this angle, that slags easily went aside.
If you have to work with metal, which have a considerable thickness, then a special approach must be taken here. It is inadmissible to move the cutter to the moment, when the metal is cut to its full thickness. As you finish cutting it is important, reduce the speed of advancement and maintain the angle of the cutter more on 10-15 degrees. The cutting procedure itself should be performed as follows, so that there are no significant pauses during it. If so, that had to stop at a certain section, then no need to go back to cutting at that point, in which work was interrupted. It starts first, and choose a new starting point.
After cutting, you need to shut off the supply of cutting oxygen, then do the same with the regulating oxygen. The final action should be the shutdown of propane.
Surface and figured cutting
In some situations, it may be necessary to create a relief on the surface by cutting grooves on the sheet. If you decide to use a similar method of cutting, then the metal will be heated by more than one cutter flame. Molten slag will also contribute. Becoming liquid, it will spread over the entire surface, which will lead to heating of the lower layers of metal.
The first step in the implementation of surface cutting is the heating of the selected area to the ignition temperature. After the start of the supply of cutting oxygen, you will create a zone of combustion of the metal, and due to the uniform movement of the cutter, the cut line will get a clean edge. The operation itself must be performed as follows, so that the cutter is at an angle 70-80 degrees relative to the sheet. When the cutting oxygen starts to flow, the cutter is arranged as follows, so that it forms an angle from the treated surface 17-45 degrees.
To create grooves of appropriate size, you must change the cutting speed: to get more depth, the speed increases, and for the smaller - reduce. To create more depth, you need to increase the angle of the mouthpiece, cutting should be performed at a slow pace, the oxygen pressure will also have to be increased. You can influence the width of the groove with the right diameter of the cutting oxygen jet. It should be borne in mind, that the difference between the depth of the groove and its width must reach 6 times. And the advantage should be in the latter. Otherwise, you may encounter such an unpleasant phenomenon, as the emergence of measures on the surface.
conclusion
Despite the fact that against the background of gas welding gas cutting has its advantages, this work should be approached with the same responsibility. In addition to preparing the necessary equipment, it is necessary to get acquainted with the basic nuances of performance of this work. And although this operation seems quite simple, however, if you make mistakes when cutting with gas, this can lead to serious problems, associated with the continued use of the product.