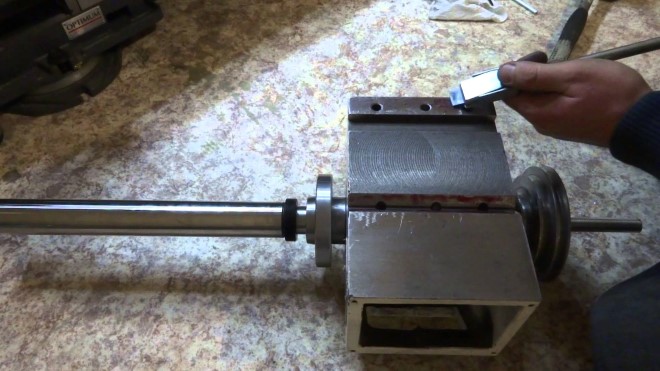
Scraping of metal: technology, see, tools
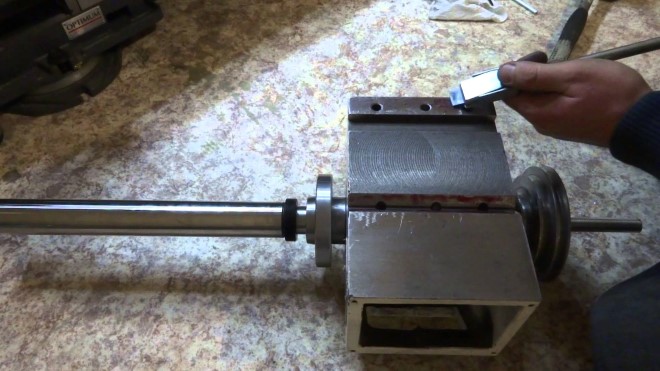
Scraping, which is also called scraping or scraping, Is a technological operation, that allows to carry out processing of surfaces of metal details with a high degree of accuracy and quality. It is no coincidence that experts consider such an operation one of the most complex and time-consuming, as it is practically not amenable to mechanization, and its implementation requires the performer appropriate skills and sufficient experience.
Scraping steel plate
Features of the operation and tools
Surface scraping is a finishing metalwork operation, the meaning of which is, to using a special tool, called scraper, scrape a thin layer of material from the part. The thickness of the material varies in the range 0,005-0,07 mm. With the help of this operation, metal products are mainly processed, quite rarely - plastic and wood parts.
Since scraping is a finishing operation, it is used to perform machining of parts, whose surface already has a low degree of roughness.
This process is just perfect for machining parts, which will later be combined and moved relative to each other. In such mobile connections, formed from parts with perfectly machined planes, the oil is reliably kept, and a tight fit of the elements is provided, which is a necessary condition for the accurate operation of the node. Using the scraping operation, perform processing:
- parts of devices for various purposes;
- elements of plain bearings;
- the outer part of measuring instruments and control devices: calibration plates, rulers, squares, etc. .;
- guide elements of different machines: lathe, drilling, etc. .;
- flat and curved surfaces for any other purpose, which are subject to increased requirements due to their roughness and accuracy of mutual location.
Scraping of details of the lathe
Scraping process, as mentioned above, practically not amenable to mechanization. Perform this technological operation using a hand tool, which is called a scraper. To date, the following types of tools are used to perform shabreniya:
- are classified according to the configuration of its cutting part into flat, shaped and triangular;
- are subdivided by the design into integral and components;
- one thing- and bilateral instruments, differing in the number of cutting parts.
Constructions of scrapers: and - one-sided flat, b - with a curved end, in - bilateral flat; g - multifaceted; d - sharpening angles
In the manufacture of tools, designed to perform shabreniya, tool steel is used as the main material. In those cases, when the tool has a composite structure, its working part can be equipped with carbide inserts or cutting elements, made of high-speed steel.
Scraper plate handle
On the geometric parameters of the tools, by means of which shabrovka is carried out, affects a number of parameters:
- material manufacturing parts, which will need to be processed;
- angle, under which the tool is located in relation to the surface of the part;
- surface characteristics, necessary to obtain in the process of processing.
Scraping of flat surfaces is preferably performed using one- and a two-way instrument, cutting part of which may have a rectilinear or curvilinear configuration. Depending on the type of processing, the end section of the tool is sharpened at different angles to its axis:
- when performing roughing - 75-90 °;
- for finishing type - 90-100 °;
- scrapers for finishing - 90 °.
scraper sharpening
The parameters of this angle are also affected by the hardness of the metal, the surface of which must be treated. So, scraping of details, made of soft materials, is made by the tool, the end part of which is sharpened at an angle 35-40 degrees relative to the axis of the tool, steel products - 75-90 degrees, of bronze and cast iron - 90-10 ° degrees.
Important parameters of the tool, by means of which shabrovka is carried out, is the length of the cutting edge of the tool and the radius of its rounding.
The value of such parameters is also mainly influenced by the hardness of the processed metal and the type of processing. Those, who is a professional locksmith, probably know, that harder metals are processed by the tool with a narrow working part and the minimum radius of rounding of a cutting edge. Depending on the type of processing and requirements, presented to the degree of roughness of the workpiece, the width of the cutting edge of the scraper is selected within the following limits:
- roughing - 20-30 mm;
- clean shabruvannya - 15-20 mm;
- finishing - 5-12 mm.
Manual adjustment of the scraper
Scraping of flat surfaces is the simplest technological operation. A tool with a more complex shape of its cutting part is used to process the elements of the curvilinear configuration. So, parts of plain bearings are machined with scrapers, having an annular structure, and concave surfaces - a tool, which has three cutting edges at the same time. Such tools, which are quite easy to fill and sharpen with your own hands, have longitudinal grooves on the cutting part, and the angle of sharpening of their cutting part is 60 °.
Scraping of curved surfaces
Scraping of flat details
Operation of scraping of surfaces of details, having a flat shape - the most common technological operation, the algorithm of which has been well developed for several decades. In this manner, in particular, perform processing of elements of a bed, lathe guides and machines of any other type.
Tool, by means of which operation of a saber is carried out, can move manually "on itself" or "from itself". Almost all experts in metalwork confirm, that more productive scraping is obtained in that case, if the tool moves "on itself". Proper surface preparation is a very important point for high-quality finishing, which will be exposed to it.
techniques of scurvy
Paint is an integral part of this technological process, necessary for better performance of saber. So paint, which is a mixture of engine oil with red lead, blue or blue, first applied to the test plate, from which it is then transferred to the surface of the workpiece by means of circular motions. With the help of the paint applied in this way, the specialist detects the most protruding areas on the surface of the part, subject to scraping in the first place.
Preparation for scraping
Algorithm, which is performed by scraping with the movement of the scraper "on itself", looks as follows:
- detail, which will need to be processed, fixed in the vise;
- the scraper is taken with both hands in its middle part and bring its cutting part to the surface of the part, clamps for the team, so that the angle of inclination relative to the surface of the product was close 80 °;
- cutting edge tool, with which the operation will be performed shabreniya, is brought to the border of the painted spot, then it is scraped off;
- performed directly sabering, first draft or previous, and then - clean.
The sequence of scraping by the method of "three plates"
Naturally, dimensional elements of a lathe or any other machine, which are not possible to remove and fix in the vise, processed locally. When performing saber, as well as any other metalwork, safety requirements must be strictly observed.
Quality control of the executed saber is carried out by means of a special frame with a transparent window, the dimensions of which are 25 on 25 mm. In such a window, if the operation is performed qualitatively, ??should be clearly calculated 12-16 paint stains, distributed evenly over its entire area. The technique of performing such control is as follows:
- the frame with the window is placed on the surface of the machined part;
- consider the number of spots of paint on the surface area, limited window frame;
- this procedure is repeated in several places on the surface of the part;
- calculate the arithmetic mean of the number of spots of paint in the window and compare it with the normative indicator - 12-16 spots.
Calibration of planes with a digital caliper
Such a device, like a frame with a window, not suitable for checking the quality of curved surfaces. Therefore, for such purposes, use a flexible polymer film, on which the grid with the sizes is put 25 on 25 mm. The convenience of using such a film is, that you can easily add that configuration, which has the surface of the machined part. Satisfactory processing is considered in that case, if the number of paint stains in the window corresponds to the normative value on 75 sections of the surface of the part.
After the operation, usually, the grinding procedure is carried out, which allows you to align the treated surface with an accuracy of 0,0001 mm. This process is performed not only with the help of various tools, but also with the use of abrasive materials: powders and pastes.
Technological operations for finishing the surface of parts after scraping, mentioned above, despite its complexity and many nuances of their implementation, can be quite successfully and quickly mastered by educational videos, are located on the Internet.