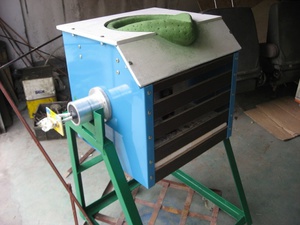
Method and technology for metal smelting in induction furnace
Induction furnace is used for melting non-ferrous and ferrous metals. Aggregates of this principle of action are used in the following areas: from the finest jewelry to industrial smelting of metals in large sizes. This article will discuss the features of different induction furnaces.
Induction furnaces for melting metal
The principle of operation
Induction heating is the basis of the furnace. In other words, electric current creates an electromagnetic field and heat is released, which is used on an industrial scale. This law of physics is studied in the last grades of secondary school. But the concept of electric unit and electromagnetic induction boilers can be confused. Although the basis of work here and there is electricity.
How it happens
The generator is connected to an AC source, which enters it through an inductor, inside. The capacitor is activated to create an oscillation circuit, which is based on a constant operating frequency, to which the system is configured. With increasing voltage in the generator to the limit 200 The inductor creates a magnetic field of variable action.
The circuit closes, most often, using a core of ferromagnetic alloy. The alternating magnetic field begins to interact with the workpiece material and creates a powerful flow of electrons. After entering the inductive action of the conductive element in the system there is a residual voltage, which in the capacitor promotes eddy current. The energy of the eddy current is converted into thermal energy of the inductor and is heated to high melting points of the desired metal.
Heat, produced by the inductor, apply:
- for melting soft and hard metals;
- for hardening of a surface of metal details (example, tool);
- for heat treatment of already manufactured parts;
- household needs (heating and cooking).
Brief description of different furnaces
types of devices
Crucible induction furnaces are used for melting metals, their main principle, different from the operation of other units, there is a lack of core.
- Channel units of induction action are a kind of transformer, which has a steel tip - a magnetic drive. The load is applied through the secondary winding, performed in one turn.
- Induction devices of vacuum action, which process of melting is performed in conditions of complete vacuum, which literally removes all impurities from the metal.
- Melting furnaces of crucibles - inductors on the mass of melting from 5 to 200 kg with a transistor-based converter.
Induction crucible furnaces
Is the most common type of induction furnace heating. Distinctive feature, different from other species is that, that an alternating magnetic field appears in it in the absence of a standard core. The crucible in the form of a cylinder is placed inside the inductor cavity. Oven, or the crucible is made of material, which resists fire well and connects to alternating current.
positive aspects
energy is released when loading metal, there is no need to install intermediate elements;
- metal alloys, consisting of several components, after melting, a homogeneous consistency and the same chemical composition are obtained in any selected volume;
- with the help of pressure regulators it is possible to carry out recovery, oxidative or neutral process;
- the average frequencies of alternating current show high values of specific power, which puts crucible furnaces in a number of high-performance units;
- the furnace can operate with breaks between metal loads, the next swimmer will not be affected, the transition from one type of metal to another occurs without prolonged readjustment of parameters;
- crucible units are easy to put on automatic control, they are easy to operate and easily rebuilt to any of the modes;
- the process results in quality fame, consisting of many components, the temperature is constant and the same value within the bath, and residues and waste melt quickly, no overheating.
Crucible units are environmentally friendly heat sources, the environment is not polluted by melting metals.
There are shortcomings in the operation of crucible furnaces:
- at technological processing slags of the lowered temperature are used;
- produced lining of crucible furnaces has low resistance to destruction, this is most noticeable at sharp temperature jumps.
The existing shortcomings are not particularly difficult, the advantages of the crucible induction unit for melting metal are obvious and have made this type of device popular and in demand among a wide range of consumers.
Channel induction melting furnaces
This type is widely used in the smelting of non-ferrous metals. Effectively used for copper and brass-based copper alloys, cupronickel, bronze. Aluminum is actively melted in duct units, zinc and alloys in the composition of these metals. Extensive use of furnaces of this type is limited due to the inability to perform lining, resistant to destruction, on the inner walls of the chamber.
Molten metal in duct furnaces of the induction type performs thermal and electrodynamic motion, which provides constant homogeneity of mixing of components of an alloy in an oven bath. The use of duct furnaces of the induction principle is justified in cases, if the molten metal and manufactured ingots have special requirements. Alloys are of high quality in terms of gas saturation coefficient, the presence of organic and synthetic impurities in the metal.
Induction duct furnaces work on the type of mixer and are designed to level the composition, maintaining a constant process temperature, and choosing the rate of pouring into molds or molds. For each alloy and casting composition there are parameters of a special charge.
advantages
- the alloy is heated at the bottom, to which there is no air access, which reduces evaporation from the upper surface, heated to a minimum temperature;
- duct furnaces are economical induction furnaces, since the melting is provided by a small consumption of electricity;
- the furnace has a high efficiency due to the use of a closed loop magnetic wire;
- constant circulation in the furnace of molten metal causes acceleration of the melting process and promotes uniformity of mixing of the alloy components.
shortcomings
- the resistance of the inner lining of the stone is reduced by the use of high temperatures;
- lining is destroyed by melting chemically aggressive bronze alloys, tin and lead.
- when melting the contaminated low-grade charge, the channels become clogged;
- surface slag in the bath is not heated to high temperatures, that does not allow to carry out operations in the interval between metal and a shelter and to melt shavings and scrap;
- duct units do not tolerate breaks in work, which forces to keep constantly in a furnace throat a considerable quantity of a liquid alloy.
Complete removal of molten metal from the furnace leads to its rapid cracking. For the same reason, it is impossible to perform a quick adjustment from one alloy to another, it is necessary to do some intermediate swimming trunks, which are called ballast.
Vacuum induction furnaces
This type is widely used for melting high quality steels and nickel, cobalt and iron alloys of heat-resistant quality. The unit successfully copes with the melting of non-ferrous metals. Glass is boiled in vacuum units, process high temperature parts, produce single crystals.
The furnace is a high-frequency generator, located in an inductor isolated from the environment, transmits high frequency current. To create a vacuum, air masses are pumped out of it by pumps. All operations on the introduction of additives, loading the charge, issuance of metal is carried out by automatic mechanisms with electrical or hydraulic control. Alloys with small impurities of oxygen are obtained from vacuum furnaces, hydrogen, nitrogen, organic. The result is far superior to open induction furnaces.
Heat-resistant steel from vacuum furnaces is used in tool and weapon production. Some nickel alloys, containing nickel and titanium are chemically active, and getting them into other types of furnaces is problematic. Vacuum furnaces pour metal by turning the crucible in the inner space of the casing or rotating the chamber with a fixed furnace. Some models have a hole in the bottom to drain the metal into the installed tank.
Crucible furnaces with transistor converter
Used for limited weight of non-ferrous metals. They are mobile, are lightweight and easily moved from place to place. The complete set of the furnace includes the high-voltage transistor converter of universal action. Allows you to choose the power, recommended for network connection, and accordingly to her type of converter, which is necessary in this case with a change in the parameters of the weight of the alloy.
Transistor induction furnace is widely used for metallurgical processing. With its help details in blacksmithing are heated, harden metal objects. Crucibles in transistor furnaces are made of ceramic or graphite, the first are designed to melt ferromagnetic metals, such as cast iron or steel. Graphite is installed to melt brass, copper, silver, bronze and gold. They melt glass and silicon. Aluminum melts well with cast iron or steel crucibles.
What is the lining of induction furnaces
Its purpose is to protect the furnace casing from the destructive effects of high temperatures. A side effect is heat retention, so, the efficiency of the process increases.
The crucible in the design of the induction furnace is performed in one of the ways:
- method of excavation in small furnaces;
- printed method of refractory material in the form of masonry;
- combined, combining ceramics and buffer layer in the gap between the masonry and the indicator.
The lining is made of quartzite, corundum, graphite, fireclay graphite, magnesite. Additives are added to all these materials, improving the characteristics of the lining, reducing volume changes, that improve sintering, increasing the resistance of the layer to aggressive materials.
A number of concomitant conditions are taken into account when choosing a material for lining, namely, type of metal, price and refractory properties of the crucible, service life of the warehouse. Properly selected lining composition should provide the technical requirements for the process:
- obtaining high quality ingots;
- the largest number of full-fledged smelting without repair work;
- safe work of specialists;
- stability and continuity of the melting process;
- obtaining quality material using economical resources;
- use for lining common materials at a low price;
- minimal impact on the surrounding space.
The use of induction furnaces allows to obtain alloys and metals of excellent quality with a minimum content of various impurities and oxygen, which increases their application in complex areas of production.