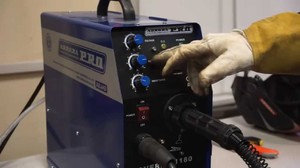
Semi-automatic welding technology for beginners in a carbon dioxide environment
Semi-automatic welding machine is available modern equipment, which is used in domestic work in the house and in the yard. Buying a device, novice welder gets the opportunity to easily learn to weld ferrous and non-ferrous metals. With the use of semi-automatic welding in carbon dioxide, it is possible to quickly connect the surfaces of metal parts without additional reinforcement. Other elements are used, which contribute to the welding of high quality metals.
For the operation of the semi-automatic welding machine, a mechanical method of feeding the wire into the working area has been developed, used as an electrode. The wire is made of a specially designed alloy. The equipment is easy to operate and can be successfully mastered by any beginner.
features of work
For those, who does not have much experience, The best way to master metal joints is semi-automatic welding for beginners. Video of the welding process with detailed comments can be viewed online. Semiautomatic device belongs to the type of devices, the efficiency of which depends half on the skill of the operator. The design of the semi-automatic welding machine consists of a number of components:
- device for converting voltage in the network to the desired parameters;
- welding torch for carbon dioxide environment;
- mechanism for constant movement of the wire;
- automatic gas supply system.
Principle of action
A burner is a very important working device, which forms a certain environment for welding and a protective atmosphere of gases, which are used for operation of the semiautomatic welding machine. Without the use of inert gases increases the spray of hot metal droplets and reduces the brightness of the electric arc. Given the performance of the semiautomatic welding machine, we can talk about the indispensability of devices for certain technological cycles in the production process when working with metals of any quality.
An inert environment is created by the use of certain gases. These include argon, helium, carbon dioxide or their mixed compositions. Argon and carbon dioxide are most often used to give the welding process an inverter method, if necessary in the process. The working power source is a direct current of the return direction, at the same time a negative impulse is applied to the part. The use of gas complicates the process itself, but the quality of the resulting seam is covered by a slight inconvenience. The gas mixture is used in the specified proportions, which are determined for each inert carrier separately.
Varieties of semi-automatic welding machines
There are several types of wire feed, different from each other. In some units the principle of action is provided, other semi-automatic welding machines push the wire into the working area. Those machines are effective in their work, which provide for two principles of work - pushes and pulls.
Steel wire is sometimes used to weld various metals, connecting other parts requires the use of aluminum wire. Some responsible production stages require the use of universal wire, defined in the production documents. Seam protection during its creation is performed in three main ways:
- the method of using the flux reaction is selected;
- the semiautomatic welding machine works in the environment of carbon dioxide;
- welding is performed using a powder electrode in the form of a wire.
The classification of the selected equipment distinguishes three types, which distinguishes the units from each other:
- depending on the type of wire used;
- from the option of protection of the obtained weld;
- by type of movement of wire and burner.
Characteristics of work allows to divide the welding equipment for welding into three types:
- stationary units, installed for long-term use;
- mobile equipment for short distances;
- portable compact appliances for household use.
Semi-automatic metal joining
Getting Started
For high-quality welding process are determined by the name of the tools, necessary for work. The welder prepares an angle grinder (grinder) with the established circle on metal for cleaning of a surface. You will need a hole punch and two - three clamps and the device for welding metal in a medium using carbon dioxide. Portable manual non-industrial welding allows you to connect metal surfaces up to 6 mm.
Before welding, clean the seam, the edges are smoothed with a Bulgarian. First, install a bay with a wire and check the possibility of unimpeded normalized ingress of flux. Join the two surfaces in the planned places and press them with clamps. After that it is necessary to let an electric negative charge on one of the prepared surfaces.
welding process
We put the switch of the semiautomatic device in position "three" and we choose optimum giving. Semi-automatic butt welding, first make small areas of tack at intervals, then weld the joined plane of the parts with a solid seam. When performing the seam, the tip of the device is placed obliquely to the surface at an angle of about 20 ?. In a similar way weld surfaces overlapping or at the set angle.
The model of the device and the type of wire are important, used as electrodes, which are selected under the type of metal. The optimal and most common types of electrodes are MP-3 and OZS-12. They can cook metal of different thickness, but have the disadvantage of a large mass of slag.
To prevent leakage of slag into the bath from the burned welding flux, as in standard classical welding with use of usual type of electrodes, it is recommended to clean it after the seam and put another on top. This will help to get a good tight connection.
Powder wire has a high brittleness and low wall thickness, so, low rigidity of a design. At performance of work apply the mechanism, feeding with a small compression, and turn the hose slowly, without sharp turns. Be sure to keep the phases on the parts and holders. The combustion of an electric arc and the release of a protective gas layer depends on this.
Selection of semi-automatic welding mode
When working on a semi-automatic welding machine, the operating mode is determined, but this requires exploring all possible options available. The mode indicator is determined, mainly based on the thickness of the weld metal and its type. To perform welding of metal to 5 mm used a single seam, and the connection of surfaces with a thickness of 5 and 6 mm will require laying the second seam, which goes exactly on the projection of the cleaned first seam. Such welding is carried out in two stages.
Gas consumption and flow must be monitored to weld the metal. The gas pressure does not become large. He only blows the welding spot with a low hiss, but does not fly out of the burner under pressure. Gas consumption is accepted for high-quality welding, which is determined by seven liters per minute. This consumption allows you to effectively perform semi-automatic welding without distortion or deformation of the metal. Proper consumption reduces the area of thermal action on the work surface, and the seam is perfect as required. An experienced craftsman independently determines the speed of operation and selects the required height of the weld.
Quarrel with their hands
At the beginning of the work should determine and select the strength of the current, depending on the thickness of the metal to be joined. This work is done using a table, printed in the instructions for the unit. Reducing the current leads to a decrease in the productivity of the semi-automatic welding machine.
Adjust the required wire feed speed to the machine, this is done by selecting different types of gears, sold together with the unit. Choose the required amount of voltage.
To determine the correctness of the selection of the above parameters make a test welding on a metal section with similar characteristics. The correct settings will allow the machine to give a stable arc and emit a sufficient amount of flux.
Select the "forward" position on the wire feed switch and fill the receiving hopper with flux. Install the holder, lining the mouthpiece in the working welding area. Open the flux damper, press "start" and make tangential movements to the place of the intended seam to ignite the arc.
Features of aluminum welding
Aluminum oxide film is usually formed on the aluminum surface during welding in conditions of oxygen supply., melts slowly and has a higher density, than the metal base. For successful welding of aluminum, the edges and the place of application of the seam are treated with chemical solvents to remove the film or cleaned by abrasive mechanical means.
It is very difficult to monitor the quality of the seam when welding aluminum, strong heating leads to brittle edges, which are destroyed. It is very difficult to trace the degree of heating of the metal, as it does not change color when heated. The fluidity of aluminum leads to leakage of metal through the seam, and it is difficult to control the size of the bath. To avoid metal burns, use gaskets made of ceramic or other metal to correct the size of the seam.
Aluminum and its alloys have a high coefficient of expansion, but at the same time have low elasticity. To avoid deformation, parts are preheated or welded with optimal parameters.
In the process of cooling the weld metal cracking occurs, caused by deformation during cooling of the bath material. To avoid a destructive phenomenon, plasticizers are added to the seam material, and the aluminum joints are not close together.
For aluminum welding it is better to use the mechanism of giving of a wire of pulling type. The depth of boiling directly depends on the strength of the welding current. The width of the seam does not depend on the magnitude of the electric current. The increase in boiling depth is affected by a decrease in the diameter of the electrode, which is especially evident at low currents. With increasing current, the dependence on the diameter of the electrode is not so obvious. As the diameter of the electrode increases, the weld becomes wider.
The use of semi-automatic welding machines in everyday life is very effective, since it does not require large power consumption, can cook all metals without exception and use such a unit can anyone who wants to learn how to weld.