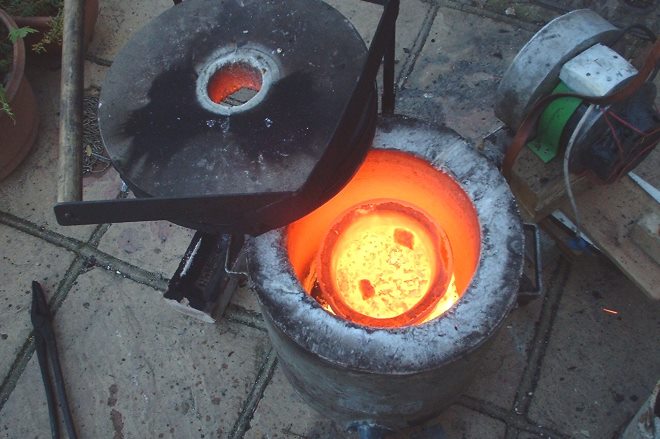
Bronze melting point and bronze casting at home
The melting point of bronze of a certain brand depends on it, what chemical elements are part of this alloy. In order to perform casting of bronze products at home, it is necessary to equip the workshop with the corresponding equipment and to adhere strictly to technological recommendations.
Melting bronze at home
Types of bronze alloys and differences in their melting temperature
The basis of such an alloy, like bronze, is copper, and as alloying additives are tin, aluminum, silicon, lead and beryllium. Bronze of any brand contains such elements in small quantities, as phosphorus, zinc, etc. In addition to bronze, modern industry also produces other alloys based on copper - cupronickel, copel, constantan and nickel silver (the main alloying element in them is nickel), brass (orichalc).
The number of basic alloying additives in bronze determines not only its physical and chemical properties, but also color.
Each of the brands of bronze, the melting point of which is in the range of 930-1140 °, marked by its labeling. Depending on its chemical composition, all bronze alloys are divided into:
- tin;
- unleaded.
Combine copper and tin, to get bronze, man has learned since ancient times. Lead, which is added to such an alloy, makes it firmer, if you compare it with pure copper, and also reduces its melting point. One of the brightest examples of such an alloy is bell bronze, from which bells have long been made by casting. It contains 80% copper and 20% tin. The most significant disadvantage of this type of bronze, due to the tin content, there is an increased fragility of products from them.
Processing temperature and technical properties of tin bronzes
Lead-free bronze, as their name implies, do not contain tin. Alloys of this type are presented on the modern market of one of the following categories of bronze:
- beryllium - the strongest, in many respects surpass high-quality steels;
- silicon-zinc, characterized by special resistance to abrasion (the great dignity of bronze in this category is that, that in the molten state they have high fluidity);
- alloys with the addition of lead, which are characterized by increased corrosion resistance;
- made on the basis of copper and aluminum, excellent characteristics of which are increased corrosion resistance and good antifriction properties.
Melting point and other physical properties of tin-free cast bronze
Although bronzes with the addition of tin are highly fragile, as mentioned above, they are still the most common today. Letters "K" are used for marking of any marks of bronze irrespective of their chemical structure., after which the designations of additives are listed, as well as their percentage. As an example, we can decipher the designation of bronze brand Br OTSSN3-7-5-1. In this bronze, which belongs to the tin type, contains 2.5-4% of tin, 6-9,5% zinc, 3-6% lead, 0,5-2% nickel. In the chemical composition of any bronze, as mentioned above, other elements may be included, which are denoted by the following letters:
- A - aluminum;
- B - beryllium;
- W - iron;
- K - silicon;
- Mts - manganese;
- F - phosphorus.
Chemical composition and purpose of common brands of bronze (click to enlarge)
If we talk about the most common brands of bronze, then they should be attributed:
- alloys of foundry type BrO5, BrO19, BrOC8-4, BrOC10-2, BROF10-1;
- malleable bronze alloy BrOS5-25.
For such a technological operation, as casting, especially performed at home, temperature is very important, at which it is possible to melt metal. Bronze, containing tin, melt at a lower temperature of 900-950 °, and those of them, which do not contain this metal, - at a temperature of 950-1080 °.
Bronze casting alloys have a high viscosity when heated to the melting point, if you compare them with brass. That is why, to perform high-quality casting of such alloys, they must be overheated. A significant advantage of the use of foundry bronzes is that, that the shrinkage of products from them is very insignificant. This allows you to make shaped alloys from such alloys.
Filling the mold with bronze cast iron
It is possible to cast bronze at home
To perform casting of bronze products at home, you need to create all the necessary conditions for this. The most important of these conditions is good ventilation in the workplace, as well as the use of funds, providing fire safety. If you are going to make bronze products of small size, there will be enough space for a small room, if you have plans to make large castings, then you need a spacious room (example, garage). The obligatory requirement for such premises is a floor made of non-combustible material.
To melt such material, like bronze, you need a muffle furnace. Preferably, that this device is equipped with a heating temperature controller. If such an oven is not at your disposal, then for melting bronze at home, an ordinary furnace is suitable.
Homemade furnace with a fan from the old hood
In addition to the furnace, which will melt the metal, for casting bronze products will be needed:
- crucible - a steel or cast iron vessel with a spout (for melting and pouring metal on forms);
- tongs, by means of which the crucible is removed from the furnace;
- hook;
- foundry mold, in which the molten metal is poured;
- charcoal, used as fuel (if a furnace is used for metal melting).
The crucible for melting is easy to make from cutting a thick-walled steel pipe
The procedure for casting bronze products is as follows.
- Metal, which must be melted, grind and place in a crucible.
- The crucible is placed in the oven and heated to the desired temperature.
- After the metal is completely melted in the crucible, it is left in the oven still 4-5 minutes to warm up. Such warming up is necessary for that, so that the metal acquires maximum fluidity and well fills all the recesses in the mold.
- Crucible with molten metal, using hook and pliers, removed from the oven.
- Liquid metal through a special pouring hole is poured into the mold. It is important to monitor this, that the stream of the poured alloy was thin and was not interrupted.
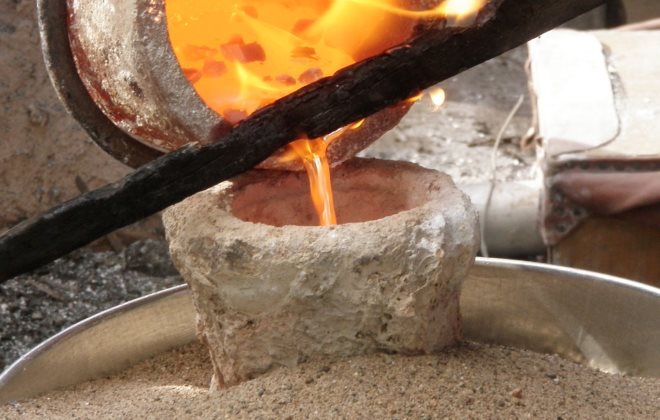
Pouring the bronze melt should be done quickly and accurately
The casting mold must be prepared in advance, which is its calcination in the oven. To carry out this procedure, the oven is heated to a temperature of 550-600 °, and only after that the casting mold is placed in it. Then the temperature in the furnace is increased to 900 ° and maintain the shape under its influence for 2-4 hours.
The larger the size of the foundry mold, the longer it must be kept in a hot oven. After the mold is completely calcined, it must be removed from the oven and cooled to 500 °, only then can it be used for casting.
The video of this process allows to get acquainted in more detail with the rules of bronze casting and the equipment used for these purposes..
How to properly pour metal into a foundry mold
If the molten metal is poured into large molds, then his own weight is enough for that, to expel from them all the air formed. If the casting is performed in small forms, it is almost impossible to displace air from all internal cavities of such structures due to the mass of molten metal. To obtain high quality castings in such cases, it is necessary to use special technological methods.
Foundry molds are placed in special centrifuges, operating from a manual or electric drive. Centrifugal forces are created during rotation, evenly distribute the molten metal throughout the internal cavities of the molds. This technology is effective only if, if the metal is in liquid, and not in a frozen state.
Homemade centrifuge for casting small parts
After the casting and cooling of the metal, the castings are removed, using the simplest mechanical devices. It should be borne in mind, that the surface of the products, just removed from the molds, not of high quality, therefore, they must be subjected to various types of machining.
Production of molds for casting
On the quality of products, obtained by casting from bronze alloys, seriously affects the correctness of the mold, which allows to create from the molten metal a detail of the necessary configuration and with the set geometrical parameters. For the manufacture of molds traditionally use special devices - crucibles. Flask, the dimensions of which should be about one and a half times the parameters of the finished product, consists of:
- upper limit;
- lower box.
The mold is made for a specific product
The upper and lower parts of the crucible, which are filled with molding mixture, can be reliably connected to each other for greater reliability, for which special clamps on their lateral surfaces are used.
The composition of the most commonly used molding mixture includes:
- fine sand - 75%;
- clay - 20%;
- coal dust - 5%.
As a result of mixing of these components homogeneous weight should turn out.
A model is also required to make the mold, which is made of wood or other soft material (you can use its role as a finished product of the required quality).
The self-made mold for casting consists of two halves
The manufacture of the mold is performed as follows.
- The molding mixture is poured into the lower box of the crucible and lightly compacted.
- The model is placed in the obtained compacted mass, the surface of which must be pre-coated with talc or graphite powder.
- On the lower part of the crucible put the upper frame and fill it to the top with the molding mixture, also ramming it. Before filling the upper half of the crucible, it is necessary to form a hole in the future shape of the spout, for which use a special conical plug.
- After ramming the molding mixture, the finished mold should be divided into two halves - top and bottom, for which you can use any sharp object.
- After removal from the obtained mold, the internal cavities of the model are carefully inspected and defects are corrected., who may be present at them.
The finished form must be dried, then it can be assembled and used for casting bronze products. The production of the mold is more clearly shown in the video below.
The gypsum form should be covered with a thin layer of graphite
Technology of casting bronze products of higher quality
To obtain by casting a bronze product of higher quality or to make a part of a complex configuration, you can use another technology, which involves the use of a model of refractory material. In this case, a paraffin model is used to create a one-piece mold, wax or any other fusible material. This model is simply melted from the finished mold, heating it or placing it in boiling water.
Wax model of complex configuration is made of several parts, which are then refined and soldered
To ensure high accuracy of shape and geometric parameters of the model, the finished product can be used to create it. With its help the plaster form is received, into which the copy is cast.
Get acquainted with the technology, that allows to carry out qualitative molding even very difficult on the configuration of products, It is also possible with numerous videos online.