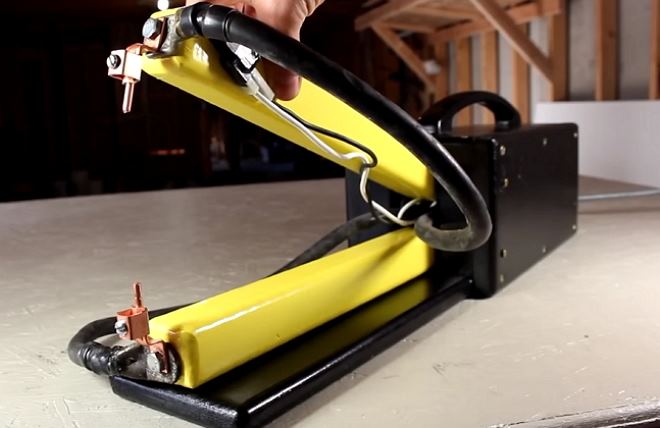
Spot welding with your own hands from the microwave - the scheme, video, Photo
Spot welding, as you know, performed on specialized equipment, however, such a device can not only be found in series production, but also do it with your own hands: this will require a transformer, taken out of an old microwave. Apparatus, obtained as a result, will give you the opportunity to perform high-quality spot welding with alternating current, the force of which is not regulated.
Self-made device for spot welding assembled
The transformer is the most important element of any such device for spot welding: his task is, to increase the input voltage to the required value. To cope with this, the device must have a high conversion factor. Large microwave ovens are equipped with such transformers, one of which you need to find. When you find such a model of microwave, it will be necessary to very carefully remove the transformer from it.
The scheme of work of graceful welding and the scheme of the welding machine
The assembly technology of the spot welding machine can be seen in more or less detail in the video below. An example of this homemade device will help us illustrate the process of creating spot welding from a microwave oven. For more detailed information on the details of the assembly, read the full article.
Remove the transformer from the microwave
If a transformer is used in a self-made spot welding machine, having power 700-800 W, then you can use it to connect metal sheets, the thickness of which reaches 1 mm. This transformer belongs to the category of devices of increasing type, to power the magnetron, it is able to produce voltage, equal 4 kV.
Magnetron, which is equipped with any microwave, requires high voltage for its operation. Due to this, the transformer connected to it has fewer turns on its primary winding and a large number on its secondary winding.. The latter creates a voltage of about 2 kV, then increases twice by using a special doubler. Check the operability of such a device by measuring the voltage, connected to its primary winding, it makes no sense.
Remove the transformer from the microwave
Carefully remove the transformer from the microwave. Do not pick up a hammer or other heavy object. Its base is unscrewed from the microwave, all fasteners are removed, and the transformer is carefully removed from the place of its installation. You will need the devices in the microwave oven, Firstly, its magnetic circuit, secondly, primary winding, which compared to the secondary is made of thicker wire and has fewer turns.
You will have to dismantle the secondary winding due to its uselessness, for which you will need a hammer and chisel. It is very important not to damage or crush the primary winding, therefore it is necessary to act with the maximum care. If when dismantling the secondary winding you find shunts in the transformer, which are used to limit the current, they also need to be removed.
The secondary winding can be cut with a chisel
If the transformer magnetic core is not glued, and welded construction, then it is better to remove the secondary winding from it with a chisel or ordinary hacksaw. If the winding is very tightly packed in the window of the magnetic circuit, then her, cutting the wire, it is necessary to drill or dig out. This should be done very carefully, since the magnetic circuit can break due to such manipulations.
After disassembly, a new secondary winding must be wound. To do this, you will need a wire with a diameter of at least 1 div. If you do not have such a wire in stock, it will have to buy. It is not necessary to buy a solid stranded wire of this cross section, you can use a bundle of several separate conductors, which in total will provide the required diameter. After installing a new secondary winding, your upgraded transformer will be able to generate current, whose strength is up to 1000 A.
The old winding can be cut with a hacksaw on the metal
If you want to make the spot welding machine more powerful, the technical capabilities of one transformer may not be enough for you. Here you need to use two such devices (in accordance, disassembling two microwaves).
Subtleties of modernization of the transformer from the microwave oven
To make a secondary winding, you need to wind it on the core 2-3 loop, which will provide an output voltage of about 2 V, and the forces of short-term welding current - more 800 A. This is sufficient for efficient operation of the spot welding machine. Winding so many turns can be difficult, if wire is used it has a thick layer of insulation. Solving this problem is quite simple: it is necessary to remove the standard insulation from the wire and wrap it with insulating tape, having a fabric basis. Very important, to cord, used for secondary winding, had the minimum possible length, which will avoid an unjustified increase in its resistance and, in accordance, reducing the current.
The new secondary winding has taken its place
If you need to weld metal sheets up to 5 mm, keep in mind, that this requires a spot welding machine, which has more power. To make it with your own hands, it is necessary to use two transformers connected in one circuit. It is mandatory to follow the relevant rules when making such a connection. If you make a mistake and incorrectly connect the terminals of the primary and secondary windings of the two transformers, a short circuit may occur. Correct connection of windings, if there is no marking on their conclusions of the same name, checked with a voltmeter.
After the correct connection of the same terminals of the two transformers, you need to measure the value of the current, which they form together. Usually, homemade transformers, are intended for spot welding machines, which are planned to operate in home workshops, limit the strength of the current - no more 2000 A. Exceeding this value will cause power outages not only in your home, but also in your immediate neighbors. And that, naturally, will lead to conflicts. The value of current, issued by connected transformers, as well as the presence of a short circuit in their circuit is checked with an ammeter.
Another example of assembly of spot welding is presented in the video below:
Recommendations for connecting two transformers
What results can be achieved, if two transformers are connected according to the rules, do not have much power? If you take two identical devices with the following characteristics: power - 0,5 kw, input voltage - 220 V, output voltage - 2 V, rated current 250 A, - then, by connecting their primary and secondary windings in series, at the output you will get twice the rated current, that is 500 A.
Short-term welding current will increase in almost the same way, but during its formation there will be significant losses, due to the high resistance of such an electrical circuit. Both ends of the secondary winding are wires O 1 cm - are connected to the electrodes of the spot welding machine.
Connection of 2 transformers according to scheme №1
If you have two powerful transformers, but their output voltage is not enough for a homemade device, their secondary windings can be connected in series, which must have the same number of turns. To such an extent they succeed, if you just wind the turns on the secondary winding is impossible due to the insufficient size of the window on the magnetic circuit.
This connection must be monitored, so that the direction of the turns on the secondary windings of the connecting devices is agreed, otherwise the antiphase may come out, and the output voltage of such a combined device will be close to zero. To experimentally determine the correctness of the connection, it is desirable to use thin wires.
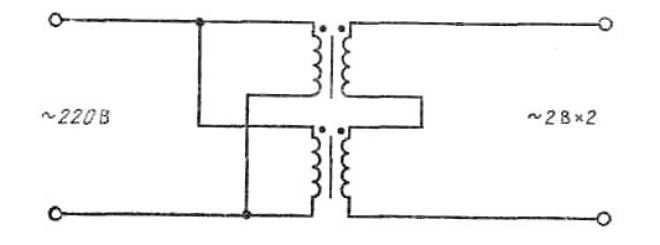
We connect two transformers according to the scheme №2
How to determine the conclusions of the same name transformers
If the terminals of the windings of the connecting devices are not marked, it is necessary to determine among them the same name, to connect them. This problem can be solved in the following way: the primary and secondary windings of two or more transformers are connected in series, voltage is applied to the input of such a combined device, and to the output conclusions (conclusions from series-connected secondary windings) connect an AC voltmeter.
Depending on the direction of connection, the voltmeter may behave differently:
- show one or another voltage value;
- do not show any voltage in the circuit at all.
If the voltmeter emits some voltage, means, in the circuit of connection and primary, and secondary windings have different conclusions. If the windings are connected in the wrong way, the following processes take place: High-voltage, coming to the input of the primary windings of two connected transformers, decreases by half; voltage increase occurs on the secondary windings, each of which has the same coefficient of transformation. The voltmeter at the output will register the total voltage, whose value is twice the value of the input.
Determine the conclusions of the transformers in this diagram
If the voltmeter shows a value of "0", that means, that voltage, emanating from each of the series-connected secondary windings, levels in value, but have different signs, so, they compensate each other. In other words, at least one of the pairs of windings, connected in a chain, connected by the same pins. In this case, the correct connection of the circuit elements is achieved by changing the order of connection of the primary or secondary windings, focusing on the voltmeter readings.
Electrodes for self-made spot welding
Choosing for spot welding machine, assembled with his own hands from the microwave, electrodes, you should pay attention to that, so that their diameter corresponds to the diameter of the wire, with which they are connected. Copper rods can be used as such elements, and for low-power devices stings from professional soldering irons will be suitable.
During operation, the electrodes for spot welding are actively worn out. To adjust their geometric parameters, they must be constantly undermined. Naturally, that over time such elements will require replacement with new ones.
Option of making electrodes from thick copper wire
Wires, which electrodes are connected to the spot welding machine, must have a minimum length, otherwise they will lose a lot of device power. Power losses will be serious in that case, if the electrical circuit "electrode - spot welding device" has many connections. If you want to increase the efficiency of your homemade equipment, it is better on wires, which connect the electrodes, soldered copper tips. Using the following tips, you will avoid loss of power at the points of contact due to increased resistance of crimping or any other connections.
Wires, connecting the electrodes to the spot welding machine, have a fairly large diameter, therefore special tips will help to facilitate their soldering, pre-subjected to tinning. Because the electrodes for such a device are removable, soldering is not performed at the joints. Of course, in such places, constantly subject to oxidation, there is also a loss of power, but they are much easier to clean, than compressed tips.
Install the electrodes on the welding machine
As mentioned above, the electrode for contact welding can be made of copper wire or a soldering iron tip from a professional, if the power of the device is low. The wire from the device is connected to the electrode with a copper tip, which is connected to it by soldering.
Installation of the lower electrode
The tip is connected to the electrode by means of a bolted connection, which must be very reliable, so that the increase in resistance at the point of unreliable contact does not lead to a loss of power of the apparatus for spot welding. To make such a connection, holes of the same diameter are made in the electrode and the tip.
Bolts and nuts, which will connect the electrodes and terminals to the wires, it is best to choose from copper or its alloys, characterized by minimal electrical resistance. Elements of such compounds, which greatly simplify the maintenance of the apparatus for contact welding, quite easy to make with your own hands.
Controls for self-made spot welding
Control of the spot welding machine (especially made from the microwave with his own hands) is not particularly difficult. Two elements are enough for this: lever and switch. Compression force between the electrodes, for which the lever is responsible, must ensure reliable contact of parts at the point of welding, connecting. To fulfill these important requirements, lever mechanisms of such devices can be supplemented with screw elements, which provide even greater compression force. Naturally, such an element of the device for spot welding must have a very high reliability.
The design of the levers is simple. A simple eraser will add convenience, mounted above the upper lever
On serious production equipment, which is used to join sheets of steel of considerable thickness, set the compression elements, creating pressure from 50 to 1000 kg - depending on the need. And on spot welding machines, which are used for irregular and simple work in the home workshop, quite enough of that, that such a mechanism creates pressure on 30 kg For convenience and simplicity of work on the device of spot welding its clamping lever do longer, it will also increase the compression force to the required value.
A lever is enough for a homemade home appliance, the length of which will be 60 cm. With this lever you can increase the effort 10 times. In accordance, if you press the lever with effort 3 kg, electrodes and parts, connected by compressive force 30 kg. That such lever at pressing did not move from the place the device, the base of the equipment must be securely fixed to the surface of the desktop with a clamp.
Spot welding machine, made with his own hands, in work
Switch, which is responsible in the device for supplying current to the welding electrodes, connected to the circuit of the primary winding of the current transformer, current in which is much less, than in the secondary. If you connect the switch to the secondary winding, then it will create additional resistance, and its contacts under the influence of a strong current will be tightly welded.
If a lever is used as the clamping mechanism, then it is better to place the switch on it, then the other hand will be free (it can be used to support welded parts).
Features of work on the self-made equipment for spot welding consist in that, that current should be applied to the electrodes only then, when they are in a compressed state. Otherwise, you will encounter intense sincere electrodes and, Consequently, with their active burning. You can get the initial experience of working on such a device with the help of educational video.
The electrodes of spot welding equipment are actively heated during operation. in addition, the transformer and current-carrying elements of such device are subject to intensive heating. To avoid overheating, which can lead to failure of spot welding equipment, the simplest cooling system should be provided. An ordinary fan is often used for this purpose. You can also take breaks from work, necessary for cooling the elements of the device.
The exposure time of the electrodes under current in the compressed state during welding can be monitored visually, focusing on the color of the point at the junction, or use a special relay.
Obviously, that to make the device for spot welding on the basis of the transformer from a microwave is absolutely simple, having carefully studied the presented videos and photos of the assembly process and taking into account the voiced recommendations.