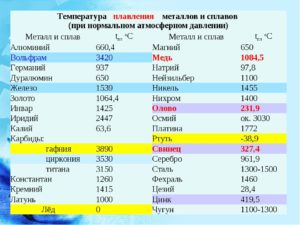
Properties of aluminum: specific gravity and thermal conductivity, production, application, alloys and melting point
Aluminum is a well-known element of the Mendeleev table from the school chemistry course. In most compounds, it is trivalent, but in conditions of high temperatures reaches some degree of oxidation. One of its most important compounds is alumina.
The main characteristics of aluminum
Aluminum is a silver metal with a specific gravity of 2.7 * 103 kg / m3 and a density 2,7 g / cm3. Light and plastic, good, as a conductor of electricity, thanks to that, that the thermal conductivity of aluminum is quite high - 180 kcal / m * year * deg (the specified coefficient of thermal conductivity). The thermal conductivity of aluminum is five times higher than that of cast iron and three times that of iron.
Due to its composition, this metal can be easily rolled into a thin sheet or pulled into a wire. Upon contact with air on its surface, an oxide film is formed (alumina), which is a protection against oxidation and provides its high anti-corrosion properties. Thin aluminum, example, foil or powder of this metal burns instantly, if they are heated to high temperatures and become alumina.
The metal is not particularly resistant to aggressive acids. For example, it can be dissolved in sulfuric or hydrochloric acid even, if they are diluted, especially, if they are heated. However, it does not dissolve in dilute in concentrated and cold nitric acid, thanks to the oxide film. Aqueous solutions of alkalis have a certain effect on the metal - the oxide layer dissolves and salts are formed, containing this metal in the anion - aluminates.
It is known, that aluminum is the most common metal in nature, but for the first time in its pure form he was able to get a physicist from Denmark X.. Oersted will c 1925 year of the XIX century. This metal is the third most common element in nature and is a leader among metals. 8,8% aluminum contains the earth's crust. It was found in mica, feldspars, clays and minerals.
Production and use of aluminum
The production process is very energy-intensive and therefore the first large plant in our country was built and launched in the XX century. The main raw material for this metal is alumina. To get it, need minerals, containing aluminum or bauxite, clean from impurities. Next, the electrolyte is melted natural or artificially obtained cryolite at a temperature slightly lower 1000 ?WITH . Then begin to gradually add alumina and related substances, necessary to improve the quality of the metal. In the process, the oxide begins to decompose and aluminum is released. Purity of the obtained metal 99,7% and above.
This element has found its application in food production as foil and cutlery, its alloys with other metals are used in construction, in aviation, electrical engineering as a substitute for copper for cables, as an alloying additive in metallurgy, aluminothermy and other areas.
What is the melting point of metals?
Melting temperature of metals - the value of the heating temperature of the metal, at which the process of transition from the initial state to another begins, that is, the process opposite to crystallization (hardening), but inextricably linked to it.
so, for melting the metal is heated from the outside to the melting temperature and continue to heat to overcome the limit of the phase transition. The point is, that the melting point is the temperature, in which the metal is in phase equilibrium, that is, between liquid and solid. In other words, it exists simultaneously, as in that, and in another state. And for melting it is necessary to heat it more than border temperature, that the process went in the right direction.
It is worth mentioning, that only for pure compositions the melting point is constant. If the metal contains impurities, then this will shift the boundary of the phase transition, a, in accordance, and the melting point will be different. This is due to the fact, that the composition with impurities has a different crystalline structure, in which atoms interact with each other differently. Based on this principle, metals can be divided into:
- easy melting, such as mercury and gallium, example, (melting point up to 600 ° C)
- sredneplavkie are aluminum and copper (600-1600° C)
- refractory - molybdenum , tungsten (more than 1600 ° C).
Knowledge of the melting point is necessary, as in the production of alloys for the correct calculation of their parameters, and in the operation of products from them, as this indicator determines the limitations of their use. For a long time, for convenience, physicists have summarized these data in one table. There are tables of melting temperatures as metals, and their alloys.
Melting point of aluminum
Melting - the process of processing metals, usually in special furnaces to obtain an alloy of the desired quality in the liquid state . As mentioned above, Aluminum belongs to the medium-melting metals and melts when heated to 660?WITH. In the manufacture of metal products, the melting point affects the choice of melting furnace or unit and, in accordance, used for casting refractory molds.
This temperature refers to the process of melting pure aluminum. Since in its pure form it is used less often, and the introduction of impurities in its composition changes the melting point. Aluminum alloys are made for this purpose, to change any of its properties, increase strength, heat resistance. As additives used:
- zinc
- copper
- magnesium
- silicon
- manganese.
The addition of impurities entails a decrease in electrical conductivity, deterioration or improvement of corrosion properties, increase in relative density.
Usually the addition of other elements to the metal leads to this, that the melting point of the alloy decreases, but not always. For example, adding copper in volume 5,7% leads to a decrease in melting point to 548?WITH. The resulting alloy is called duralumin, it is subjected to further thermal hardening. And aluminum-magnesium compounds melt at temperature 700 — 750?WITH.
Strict control of the melt temperature is required during the melting process, as well as the presence of gases in the composition, which are detected through technological tests or by the method of vacuum extraction. At the final stage of production of aluminum alloys they are modified.