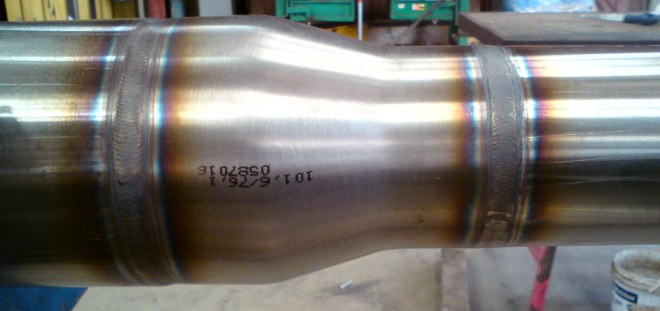
Stainless steel welding: what and how best to cook stainless steel at home
Performing such a technological operation, as stainless steel welding, it is important to consider both the physical properties of the material, and its chemical composition. Only in this case you can count on it, that the connection will be made efficiently and reliably.
Argon welding of stainless steel
Difficulty factors for welding stainless steel parts
Stainless steel welding complicates that, that this material belongs to the category of high-alloy alloys, so, it contains a fairly large number of elements, affecting its basic properties. In stainless steel, in particular, such an element is chrome. Its content in this alloy may be 12-30%. Chrome along with such elements, like nickel, titanium, manganese, molybdenum, forms anticorrosive properties of stainless steel, but at the same time endows it with other features, affecting weldability.
For those, who does not like to read long articles and delve into the technical details, we suggest you watch two videos at once with the most relevant options for stainless steel welding for a home builder - an electrode with an inverter and again an inverter, but already in a shielding gas environment (argon).
Stainless steel welding should be performed taking into account the following specific characteristics of this material.
Quite a high coefficient of linear expansion
For this reason, the welding of stainless steel is always accompanied by significant deformation of the parts, connecting. In some cases, when the welded parts have a significant thickness and there is no gap between them, such deformations can even lead to large cracks.
Low thermal conductivity
The thermal conductivity of stainless steel is 1.5–2 times lower, than low-carbon alloys. This feature of the material leads to that, the connecting parts in the welding zone are melted even at smaller (on 15-20%), than when welding low-carbon steel products, current strength.
Intergranular corrosion
At strong heating (over 500 degrees Celsius) in stainless steels there is a so-called intergranular corrosion. This is why it happens, that along the edges of the grains of the metal structure begin to form layers, consisting of chromium carbide and iron. This phenomenon can be avoided not only by careful selection of the welding mode, but also by forced cooling of welded stainless steel parts, for which you can use ordinary water. However, it should be borne in mind, that only details can be cooled by water, made of chromium-nickel steels, which have an austenitic internal structure.
Overheating of electrodes with chromium-nickel rods
Due to the low thermal conductivity of the materials to be joined and their increased electrical resistance, the welding of stainless steel parts is accompanied by strong heating of the electrodes., rods which have chromium-nickel composition. To avoid this undesirable phenomenon, use electrodes for welding stainless steel up to 35 div.
Welding electrodes Sabaros ME 101 3,2 mm for welding stainless steels
The most common methods of welding stainless steel
Welding of stainless steel products, characterized by high chromium content can be performed using several technologies. Here, in particular, the following types of welding belong:
- argon arc (using a tungsten electrode and AC / DC TIG modes);
- performed in MMA mode with coated electrodes;
- semi-automatic electric arc welding in argon, which is carried out in the MIG mode and with use of a wire from stainless steel;
- so-called cold welding of stainless steel, performed under high pressure (the name of this technology is due to the fact, that it does not involve melting the metal in the process of its connection);
- suture technology and contact spot welding.
Technology of welding of details from stainless steel provides careful degreasing of surfaces by means of acetone or aviation gasoline. This is done for that, to reduce the porosity of the seam is performed, make the welding arc more stable, carefully clean the edges of the parts, connecting. Only after thorough stripping can the operation be performed in the chosen way. There are several basic ways to weld stainless steel parts, as well as technology, which are used quite rarely. In any case, make a decision about it, how to cook stainless steel, should be based on specific conditions and requirements, presented to the molded joint.
Coated electrode welding (MMA)
Welding of stainless steel parts by MMA technology, involving the use of coated electrodes, is the most common technology. This method is quite simple, it can be used at home, but it does not allow to receive a seam of the highest quality.
Which is convenient, such welding of stainless steel can be performed even at home, but for this you will need a special welding machine, which is called an inverter. To allow the stainless steel to be welded with an inverter, which has high reliability, it is necessary to choose the right electrode for a particular brand of stainless steel. All electrodes, by means of which welding of products from stainless steels is carried out, are divided into two main types:
- with rutile coating based on titanium dioxide (welding with such electrodes, providing a small spray of metal and a stable arc, performed on direct current and reverse polarity);
- with a coating based on magnesium and calcium carbonate (such electrodes stainless steel is welded to a direct current of reverse polarity).
To understand, what electrodes to cook stainless steel, just look in GOST 10052-75, which presents all types of such consumables, and also stipulates, which of them should be used to work with metal of a specific chemical composition. To choose stainless steel electrodes, that meet the requirements of this Guest, it is enough to know the brand of metal, parts to be connected from.
All requirements for electrodes for welding stainless steel can be found by downloading free GOST 10052-75 in pdf format at the link below.
GUEST 10052-75 The electrodes are coated with metal for manual arc welding of high-alloy steels with special properties
Download
Manual and semi-automatic welding of stainless steel in argon (AC/DC TIG, ME)
Tungsten electrodes are used to perform manual welding of stainless steel in argon. This technology allows you to get quality and reliable product connections even at home, differing in small thickness. Welding of such electrodes on stainless steel is used mainly for installation of communications from pipes, on which gases or liquids will be transported under pressure.
Austenitic stainless steel should be welded especially carefully and with care
This technology has certain features.
- To tungsten, from which stainless steel electrodes are made, did not get into the molten metal in the welding zone, the arc is ignited in a non-contact manner. If you do it directly on the details is not possible, then the arc is ignited on a special charcoal plate and carefully move it to the mating workpiece.
- Welding of stainless steel in this way can be performed as a permanent, and on alternating current.
- Modes are selected depending on the thickness of the connected parts. To such modes, in particular, tungsten electrode cross-sectional parameters are included, wire diameter, used as an additive, current parameters (strength and polarity), shielding gas consumption, welding speed.
- Very important, that the level of doping of the filler wire was higher, than the connected parts.
- Stainless steel electrodes must not oscillate during welding. If you ignore this requirement, this can lead to disruption of the welding zone and oxidation of the metal in its area.
When using this technology, you can reduce the consumption of tungsten electrode. This takes some time (10-15 seconds) do not turn off the argon supply after the welding process. This procedure helps protect the hot tungsten electrode from active oxidation.
In semi-automatic welding of stainless steel in argon, essentially, little different from the usual manual method. Its main difference is, that the supply of wire to the welding zone is carried out using special equipment. Thanks to mechanization, the process proceeds much more accurately and with greater speed.
Thanks to the use of semi-automatic equipment, the following techniques of welding stainless steel parts can be implemented:
- jet transfer method, which allows you to efficiently weld large thick parts;
- short arc welding - to connect small parts;
- pulse welding is a universal technology, which allows you to get quality and reliable connections and is the most cost-effective option.
Argon arc welding of stainless steel
Other stainless steel welding technologies
There are several ways to weld stainless steel, who perform better in certain situations, that is, they are not universal. These include the following methods, which involve the use of special equipment.
Stainless steel welding using a laser beam
This method of welding, which even in the video looks very impressive, has a number of significant advantages: the metal in the welding zone does not lose its strength due to excessive temperature exposure, cools down quickly, it does not crack, and in its structure grains of the minimum size are formed. Laser welding equipment and the technology itself are widely used in various industries (car and tractor construction, installation of communications from pipes, etc.).
Cold welding under high pressure
This technology does not involve melting the material in the welding zone, and metal parts are connected at the level of their crystal lattices. Depending on the connection obtained and the configuration of the parts, the pressure can be applied to one or both metal workpieces. It is very interesting to watch a video of this process: two details, being in a cold state, as if pressed into each other.
Contact welding of stainless steel products
Such welding can be performed by spot or roller technology. As a result, thin sheets of stainless steel with a thickness of no more can be joined 2 mm The same equipment is used, as for other metals.
The video below explains in detail and clearly demonstrates the nuances of the filler rod when welding stainless steel with a non-fusible electrode in argon and other nuances of work.