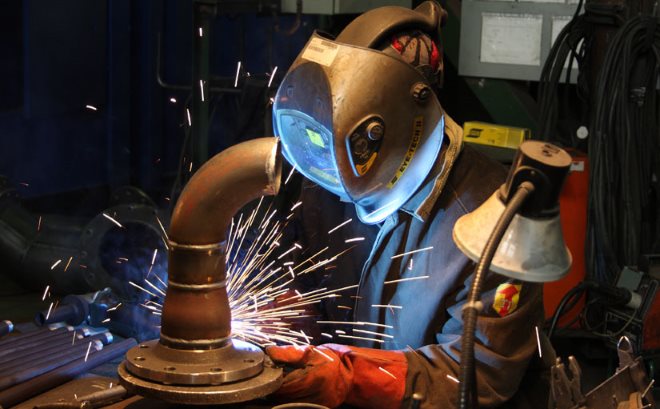
Welding of stainless steel with ferrous metal: electrodes, technology
Difficulties, associated with the welding of products, made of stainless steel, with ferrous metal, are explained mainly by that, that these materials, although they belong to steels, is, essentially, heterogeneous. In order to weld such metals, ie get a weld, which in its mechanical characteristics will be close to the base metal of the joining products, it is necessary to pick up electrodes correctly first of all. in addition, this parameter of the joining metals must be taken into account, as their weldability, that is, the ability to form high-quality and reliable one-piece connections, obtained by welding.
Welding of stainless steel flange with carbon steel outlet
Principles of welding stainless steels
The weldability of stainless steels is the ability to form high-quality welded joints (including ferrous metals) - certain characteristics of such alloys affect.
- Thermal conductivity of stainless steels, if we compare it with a similar parameter of low-carbon alloys, not high. Through those, that stainless steel is not able to dissipate heat quickly, during welding it is very hot, and this negatively affects the characteristics of the compound and the base metal. To avoid overheating of stainless steel products when welding with ferrous metal parts, it is necessary to reduce the strength of the welding current (on average on 20%).
- Stainless steel alloys have a high coefficient of linear expansion, which leads to significant deformation of the metal during welding. in addition, this factor is the cause of deformation of stainless steel products at that time, when they are already welded and cooled. To avoid this, it is necessary to provide wider gaps between the parts.
- High electrical resistance, which has stainless steel, causes significant overheating of the welding electrodes. This is especially true in that case, if electrodes are used for welding, made of high-alloy steel. To avoid these problems, welding as homogeneous, and heterogeneous steel alloys should be performed with short electrodes (not more 350 mm), the core of which is made of chromium-nickel alloys, characterized by low electrical resistance.
- Predisposition to the formation of intergranular corrosion, which is particularly prone to high-chromium steels, leads to deterioration of anticorrosive properties of stainless steel and the appearance of cracks in its internal structure. This type of corrosion also occurs due to overheating of the metal during welding. With such a phenomenon, the essence of which is, that solid carbide compounds are formed at the boundaries of the base metal crystals, fight in different ways. The most effective of these methods is the rapid cooling of the metal, subjected to significant heating during welding. However, it should be noted, that method of rapid cooling, for which ordinary water is used, effective only in those cases, when the material of manufacture of parts, the connecting ones are chromium-nickel steel.
Methods of welding stainless steel and ferrous metal products
To weld stainless steel and ferrous steel alloys, while obtaining high-quality and reliable connections, apply welding of the following types:
- coated with artificial electrodes in MMA mode;
- float, made of tungsten;
- in a protective gas environment, as which argon is mainly used.
If welding of products from ferrous metal and stainless steel is carried out on the first technology (MMA), then you need to take the electrodes, specially designed for the connection of non-ferrous metals and alloys.
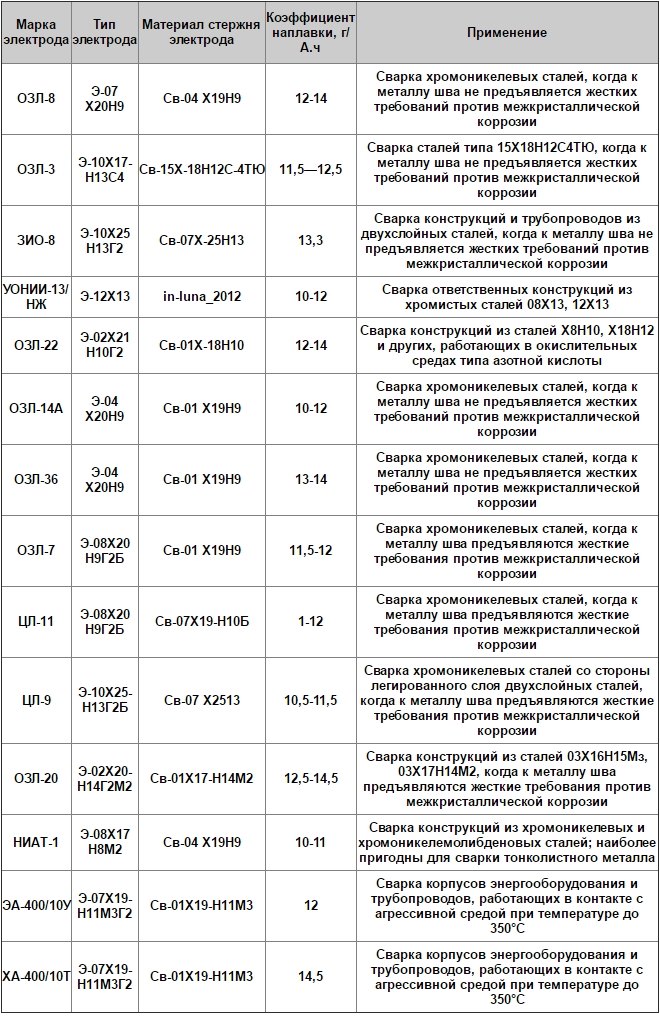
Brands and applications of high-alloy electrodes
However, it is best to cook stainless steel and ferrous metal in a protective argon gas environment. For this, naturally, will require a special welding machine. Argon in this case provides reliable protection of the formed weld zone from excessive saturation of the metal with nitrogen and its oxidation. If you do not provide such protection, then the metal of the formed weld will be very brittle, which will significantly reduce the reliability of the resulting connection.
Argon stainless steel welding scheme
To qualitatively weld products from stainless steel and ferrous metal, the position of the electrode must be monitored during the operation. Last, that the weld turned out qualitative and reliable, should be kept perpendicular to the surface, connecting workpieces.
choice of electrodes
To securely weld the product, made of stainless steel, to a detail from usual ferrous metal, a number of important nuances should be taken into account. First of all, they concern the choice of filler wire of a certain chemical composition. In the filler wire metal, the degree of doping which should be higher, than a similar material parameter is welded, must contain the following elements, like manganese, nickel and sometimes chrome.
Brands and chemical composition of high-alloy welding wire (click to enlarge)
An important condition for the formation of high-quality welded joints is the presence in the molded seam of some part of the base metal. Depending on the welding technology used, the amount of base metal in the weld material may be 30-40%.
Before cooking the stainless steel blank with a ferrous metal part, the chemical composition of welding steels should be determined, to choose the right type of electrodes.
Heterogeneous materials, which must be connected by welding, may differ in a number of parameters:
- ability to form integral connections (weldability);
- thermal conductivity;
- mechanical characteristics;
- degree of doping;
- chemical composition.
At the same time steel alloys, products from which it is necessary to weld among themselves, may belong to one of the following categories:
- carbon;
- low-alloy;
- heat-resistant;
- alloyed;
- characterized by a high degree of doping - high-alloy.
Approximate choice of welding material depending on the purpose of the weld
The main problem, which is associated with the welding of dissimilar steels (stainless steel and ferrous metals), is the formation of cracks in the formed weld. Very often, to avoid such a problem, Specialists use high-alloy electrodes to weld stainless steel products with ferrous metal parts, allowing to form a weld with high characteristics of durability parameters.
The result of arc welding of stainless steel with black steel electrode OZL-6. Although the seams are darker, but did not rust for several months
In general, for welding stainless steel products with parts, made of ferrous metals, use several basic types of electrodes:
- E50A - for steels, characterized by high heat resistance;
- OZL-25B - for steel alloys, belonging to the category of heat-resistant;
- NIAT-5 - for steels, differing in austenitic internal structure;
- CT-28 - for steel alloys, containing a significant proportion of nickel in its chemical composition.