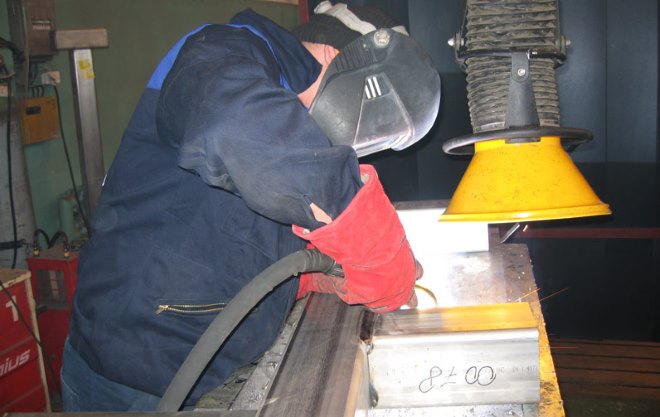
Welding of carbon steels: technology, electrodes
Execution of such technological process, as welding of carbon steels, associated with certain difficulties and has a number of features. The main reason for this situation is, that the main element, forming the characteristics of carbon steels and, in accordance, affects their weldability, there is carbon.
Duplex carbon steel welding
Features of welding of products from carbon steel alloys
Carbon, as you know, called such steel alloys, carbon content which can vary in the range of 0.1-2.07%. Depending on that, how much carbon in the composition of such alloys, they are divided into low- (to 0,25%), on average- (0,25–0,6%), as well as high carbon (0,6–2,07%). Welding of low-carbon steels, as well as medium-carbon and high-carbon, differs in certain features. However, there are general rules for such a process, which allow to receive high-quality and reliable connections of products from carbon steels.
Technological features of carbon steel welding
To ensure good weldability of the root of the seam when performing butt welds, made of carbon steels, this process is performed, holding the connected products on the weight. This recommendation is tried to follow when performing semi-automatic welding with flux cored and ordinary wire, as well as in the implementation of gas and manual arc welding, carried out using coated carbon. When using automatic equipment to perform welding of carbon steels try to create conditions to ensure the digestibility of the root of the seam and eliminate this phenomenon, as metal burning.
Tackers are made with full penetration of the joint and subsequent remelting when applying the main seam
Before welding products, made of carbon steels, they must be accurately positioned relative to each other and securely fastened, for which it is best to use special assembly devices. In the absence of such a device, you can ensure fixation with tack. Acceptances, the total length of which can reach one third of the length of the weld, it is desirable to apply from the side of the connection of parts, which is opposite to the seam. If it is necessary to perform a multi-pass weld, then the tack is applied on the other side of the joint, which is opposite to its first layer.
After performing the tack, they are carefully cleaned, inspect and correct defects, if they are detected. When performing welding of carbon steels it is necessary to achieve complete remelting of tack, which may otherwise become the focus of cracks at the weld.
Table of welding modes (on the example of low-carbon and low-alloy steels)
The technology of multilayer or double-sided welding of carbon steels is chosen, if the connection is formed, it must meet the increased requirements for its strength and reliability, whether it is necessary to connect parts of considerable thickness. If the inspection of the formed weld reveals defects (cracks, pores, undercuts, poorly cooked areas, etc.), then to eliminate them you need to do the following:
- remove the deposited metal in the area of defect detection;
- clean the defect area;
- boil the seam in the cleaned area.
Welding of this differential is performed by TIG welding, which provided high-quality boiling and no splashes
The peculiarity of the performance and automatic electroslag welding of carbon steel parts is, the connecting products are fixed with a gap, which should have some extension to the end. To carry out such fixing use assembly devices or special brackets. In order to ensure high quality of the initial and final areas of the weld when using the above technologies, the welding process does not start on the details, and on special bars, are fixed together with them.
Welding of products from low-carbon steel alloys
Welding of steels, belonging to the category of low-carbon, is not difficult for a specialist; any of the traditional technologies can be used for this. The choice of a specific method of obtaining a welded joint is made, focusing on the parameters of welded parts and requirements, which are presented to the finished connection.
Feature of welding of low-carbon steels, which additionally contain alloying additives, is, that the parent metal and the compound metal have a number of differences, which include the following:
- weld metal is characterized by reduced carbon content, but the proportion of manganese and silicon in it is increased;
- metal joining parts in the area, located next to the weld, exposed to overheating, accompanied by its slight strengthening; this situation is especially typical in those cases, when using manual arc welding technology;
- when welding parts, which are made of ageless alloy steels, there is a decrease in the toughness of the base metal in the area, located in close proximity to the weld;
- when performing multilayer welding, the weld metal may be highly brittle.
Electrodes for welding steels with alloying additives
Welded joints of products, made of carbon steels with low carbon content, if they are performed in compliance with all the necessary requirements, are of high quality and reliability.
Gas welding of carbon steel products, which contains up to 0,25% carbon, also does not cause much difficulty. When performing welding on this technology does not require the use of flux, and its feature is that, that in its implementation in the right way consumes more fuel gas.
Carbon steel products, which contain a small amount of carbon, well welded and using electric arc technology. Types of electrode coatings, which are optimal for the practical implementation of this method, is rutile (E46T) and calcium fluoristorutyl (Э42А). exept this, Many welders use electrodes to weld carbon steel alloy parts., coating which added some amount of iron powder.
Electrodes for welding low-carbon steels
For welding of details from low-carbon steels by means of electroslag welding use such brands of fluxes: AN-8, AN-8M, AN-22, FC-1 and FC-7. The type of welding wire is traditionally selected depending on, what is the chemical composition of the material of the elements, which need to be connected.
Flux welding modes
How to perform welding of parts made of medium carbon steel
Because of that, that carbon in such steels contains more, than in low-carbon, they weld a little worse. The following problems may occur when welding carbon alloy products in this category:
- the base metal and the weld metal may have different degrees of strength;
- in metal, located in the immediate vicinity of the seam, cracks may form and structures may form, characterized by low plasticity;
- weld metal and base metal, located near the connection point, are low resistance to the appearance of crystallization defects in them.
Incorrect choice of welding type and welding material leads to the absence of a weld as such
In order to avoid similar problems when welding carbon steels with high carbon content, you can use the following technological techniques:
- use of electrodes, which contain a small amount of carbon;
- execution of welding by two-arc technology, when the weld is formed simultaneously in several baths of molten metal;
- processing of edges of products, connected in this way, to ensure minimal penetration of the parent metal;
- pre-heating and associated heating of the connecting parts.
As for electric arc welding of parts, made of medium carbon steels, then in its implementation it is necessary to follow such recommendations:
- use electrodes with fluoride-calcium coating (UONI 13/45 and 13/55), which not only increase the strength of the weld, but also increase its resistance to the formation of crystallization cracks;
- The following technological methods also allow to minimize the risk of cracks in the area of the welded joint, as the implementation of longitudinal, rather than transverse oscillations of the electrode during welding, be sure to weld the craters of the formed weld;
- when performing welding it is necessary to use a short arc and apply a seam in the form of narrow rollers;
- to increase the ductility of the formed weld, you can use heat treatment of the resulting connection.
Electrodes for welding of medium carbon steels
Carrying out gas welding of products, made of medium carbon steels, preferably use the left method and use a standard or carbon-saturated flame, whose power is within 75-100 dm3 / year. To improve the quality of the weld obtained in this way, after its receipt it is possible to subject parts to heat treatment or to execute their forging. If necessary, perform gas welding of parts, whose thickness exceeds 3 mm, they must be exposed to the general (to 3500) or local heating (to 6500).
Welding of details, made of carbon steels of this category, can be performed at relatively low ambient temperatures: to -300. That the formed connection at its reception in such conditions differed in high quality and reliability, the welded structure must be subjected to heat treatment and ensure constant heating of the welding zone during the technological operation.
High quality welded joints of high carbon steels
High-carbon steel alloys have a significant carbon content in their composition, which eliminates the possibility of obtaining a quality welded connection of parts, which of them are made. Meanwhile, periodically there is a need to perform welding of such parts, so you should know, how to properly carry out such a technological process.
Carbon steels with a high carbon content are relatively well welded by methods, used for products of medium carbon steels, but the following recommendations should be followed during this procedure: do not perform welding during and at ambient temperatures below +50.
Modes of gas welding of carbon steels
Gas welding of carbon steel alloys with high carbon content is performed only by the left way and with the use of slightly carburized or normal flame. Prerequisite, which provides high-quality performance of gas welding of high-carbon steels, there is a preheating of the connecting parts to a temperature not lower than 3000.
If we talk about general recommendations for ensuring high quality welded parts, made of carbon alloys (all of the above categories), then for this purpose it is necessary to choose correctly electrodes for welding of carbon and low-alloy steels, welding wire, flame type and power, as well as strictly adhere to technological recommendations.