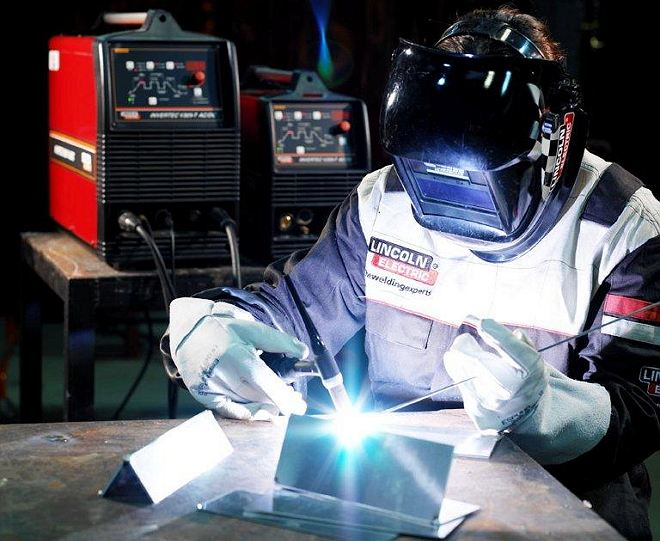
Argon welding of aluminum: step-by-step instructions for beginners, video
The most effective way to create a one-piece connection, made of aluminum and alloys based on this metal, as practice shows, is argon welding of aluminum. Any welding technology, which involves the use of shielding gas, involves the use of special equipment, as well as the welder has the relevant knowledge, qualifications and experience in performing such work. in addition, it is necessary to have at least basic knowledge in the field of metallurgy, to understand, what processes take place in the welding bath.
The process of argon arc welding of aluminum
What are the properties of aluminum should be considered when welding it
Understand the nuances of processes, flowing in the structure of aluminum when performing welding work with it, which is especially important for novice welders. To understand this well, it is necessary to get acquainted with chemical properties, which has this metal, characterized by a small specific weight, high strength and exceptional chemical activity.
The most significant characteristic of aluminum, about which not only experienced people should know, but also novice welders, is its ability to react quickly with oxygen, which leads to the formation on the metal surface of a refractory oxide film. What is characteristic, aluminum itself can melt at room temperature 650 degrees, and to melt the oxide film, covering its surface, required heating temperature, exceeding 2000 degrees. Unfused oxide film when welding by direct current can be immersed in molten metal, thereby deteriorating its internal structure.
Argon arc welding scheme
Another feature, which should be taken into account when performing welding of this metal, there is that, that it does not change its color during heating. Because of this, visually determine the degree of heating of the parts, which are quite difficult to connect, which often leads to burns and leakage of molten metal during welding.
Property of aluminum, which should be taken into account, if you are going to cook parts made of this metal, there is a significant coefficient of its volume shrinkage, which often leads to stresses and strains within the formed weld and, Consequently, to the formation of cracks in it. To avoid such unpleasant consequences, it is necessary to modify the weld or compensate for the shrinkage of the metal due to higher consumption of welding wire.
Any instructions for welding aluminum, as well as alloys based on it provides, performed by its specialist is aware of the characteristics of this metal, which should include:
- high chemical activity;
- low melting point of the metal itself;
- significant volume shrinkage.
Given all the above, can be argued, that thanks to welding of aluminum by argon receive qualitative, beautiful and reliable connections of details. And if you use to perform such welding semi-automatic equipment, then you can effectively solve two problems at once: protect the welding area from the harmful effects of the environment, as well as to compensate for the significant shrinkage of the metal due to the constantly supplied welding wire.
Of course, in addition to this technology, there are other methods of joining aluminum parts by welding, every specialist should know about the peculiarities of its use.
Modes of argon arc welding of aluminum and its alloys
Methods of welding aluminum
In addition to welding, which involves the use of argon as a shielding gas, it is possible to cook details from aluminum and by means of other technologies. The most common are:
- welding is performed using a gas burner;
- electric arc welding;
- argon arc welding.
The first of the above aluminum welding technologies involves the use of filler wire, which is fed into the welding zone, as well as a special flux, consisting of fluoride and chloride salts. Flux, which together with the filler rod is heated by the flame of a gas burner, corrodes the oxide film and opens the flame to the base metal, melting at a fairly low temperature. After welding, performed by this technology, it is necessary to wash surfaces of details at once, connecting, to wash away the remnants of caustic flux. The great advantage of this technology is that, that at its use the minimum expense of filler material is provided.
Equipment for semi-automatic welding in argon
An electric arc welding machine can also be used to connect aluminum parts, special electrodes made of aluminum or filler wire, on the surface of which is applied a plaster coating. Welding when using such a device is performed by direct current, connected to the opposite polarity.
However, as mentioned above, the highest quality connection allows to obtain argon arc welding of aluminum. Heating of details, connected when using this technology is provided by an electric arc, burning between the insoluble tungsten electrode and the connected blanks. The formation of the weld is due to the use of aluminum wire, supplied to the arc combustion zone manually or mechanically - when welding semi-automatic.
Equipment for manual argon arc welding
High temperature, which is created by burning an electric arc, which allows you to destroy the oxide film on the surface of the parts, connecting, and so that the aluminum does not have time to enter the liquid phase and flow out of the area of the formed joint, the welding electrode is moved at a fairly high speed. The great advantage of this welding method is that, that electrode, made of refractory tungsten, serves for a long time, and this saves on consumables.
To weld, performed by a semi-automatic machine using filler wire, possessed high quality and reliability, the maximum correspondence of chemical composition of such wire of structure of connected preparations is necessary.
Today devices are used to perform welding with this technology, producing direct or pulsed current, and there are devices, welding on which is carried out by alternating current.
Argon welding technology
Argon welding, which falls under the definition of welding in a protective gas environment, implies strict adherence to instructions, in which the sequence of actions is determined, performed by a specialist. From that, how correctly all these actions will be performed, depends on the quality of the molded joint, and material consumption, which are not cheap. If you have never performed such welding work, then you need to not only learn the step-by-step instructions, but also watch the video tutorials carefully, in which the whole technological process is reflected in detail.
To cook aluminum and alloys based on this metal in argon, not only the welding machine itself is needed, but also additional equipment, which provides storage and supply of consumables. Naturally, the technical condition of such equipment and the quality of all materials used directly affect the reliability of the formed connection.
The following equipment will be required to perform argon welding of aluminum parts and alloys based on this metal.:
- source of electric current, to which the welding machine and all other equipment will be connected;
- balloon, in which the protective argon gas is stored;
- mechanism, which is responsible for supplying filler wire to the welding area.
When performing argon welding at large industrial enterprises, the shielding gas is supplied to the welding machine from a centralized network.. Used on semi-automatic welding wire is pre-wound on special spools, installed on such a device. Working surfaces of workbenches, on which welding operations are performed, according to the instructions, must be made of stainless steel.
How to prepare for welding the parts are connected
The quality of welding with aluminum argon is affected not only by the technical condition of the semi-automatic machines and other devices used, but also the thoroughness of the preparation of the joined blanks.
The step-by-step video below demonstrates all the stages of such preparation:
To obtain a good connection, the connecting parts must be thoroughly cleaned of dirt, grease and traces of machine oil. For such cleaning it is best to use any solvent. If, if the thickness of the joined sheet blanks exceeds 4 mm, it is necessary to perform edge processing, and the welding of aluminum itself to perform only butt. To remove the refractory oxide film from the surface of the workpieces, their joint should be treated with a file or brush with metal bristles. If the connection location has a complex configuration, then such cleaning can be performed using a grinder.
Some features of argon welding
Welding is performed in argon, has some technological features, which can not always tell the training video. As mentioned above, for such welding, performed semi-automatically or with manual feed additive, tungsten electrodes are used, the diameter of which is chosen in the range of 1.5-5.5 mm. Such an electrode, forms a welding arc, is located at an angle 80 degrees to the surface of the parts to be joined. If the supply of filler wire is not semi-automatic, and manually, then it is placed at an angle 90 degrees relative to the electrode. If you look closely at the video of argon welding of aluminum, then pay attention, that the filler wire moves in front of the electrode.
Modes of welding aluminum with a tungsten electrode
Performing argon welding, it is very important to monitor this, so that the length of the arc was within 3 mm. A characteristic feature of such welding is that, that when it is performed with filler wire, there are no transverse movements.
Argon welding, if it is used to connect small aluminum sheets, performed with a substrate, as which you can use a stainless steel sheet. This improves heat dissipation from the welding zone, avoid burns and leakage of molten metal. Application of the substrate, to everything else, saves energy, since such welding in argon can be performed at a higher speed.
Pros and cons of welding, performed in argon
Argon welding of aluminum parts and alloys of this metal has a number of significant advantages, if you compare it with other technologies. When using this method, the connecting parts heat up very slightly, which is especially important in those cases, when it is necessary to cook workpieces of complex configuration. Connection, obtained by welding in argon, differs in high durability and uniformity of a weld, in which there are no pores, impurities and foreign inclusions. Very important, that seam, obtained by argon welding, differs in the uniform depth of penetration along its entire length.
Scheme of argon welding using a non-melting tungsten electrode
Naturally, has argon welding of aluminum and disadvantages, which you should know about. The main disadvantage is the use of complex equipment. To ensure high efficiency of welding operations and the required quality of the weld is necessary, that the welding machine itself and all accessories are set up correctly.
One of the most important parameters, which should be set correctly when performing welding in argon and other shielding gases, there is speed, as well as the uniformity of the supply of filler wire. If the feeder is set up incorrectly, then the wire in the welding zone will come intermittently, the welding arc will be interrupted, which will eventually lead to increased consumption of electricity and argon.
Argon welding is a rather difficult process, but, if you follow all the instructions and have the appropriate qualifications, it will achieve a good result.